立放井架车检测:保障石油钻井作业安全的核心环节
立放井架车作为石油钻井作业中用于起升、运输和固定井架的核心设备,其性能直接关系到钻井作业的效率和安全性。随着钻井深度和作业环境复杂性的增加,定期对立放井架车进行系统性检测已成为石油行业规范作业的强制性要求。通过科学严谨的检测流程,能够有效发现车体结构疲劳、液压系统泄漏、机械传动异常等潜在隐患,避免因设备故障导致的停工事故甚至人员伤亡,为高负荷、高风险作业场景提供可靠保障。
一、主要检测项目与技术标准
1. 结构完整性检测:包括车架主体焊缝探伤、关键受力部位应力测试、伸缩臂变形量测量,需符合SY/T 6725.3《石油天然气工业钻井和采油设备》标准要求,确保承重结构无裂纹或塑性变形。
2. 液压系统检测:采用压力传感器监测主油缸工作压力稳定性,使用超声波检漏仪排查管路渗漏点,要求系统保压30分钟压降不超过额定值的5%。
3. 安全装置验证:重点测试过载保护阀、防倾覆报警装置、紧急制动系统的响应灵敏度和可靠性,模拟超载10%工况下安全装置应自动触发停机。
4. 动态性能测试:通过加载试验验证井架车在最大工作高度下的抗风摆能力,风洞模拟8级风速时偏移量须小于设计允许值。
二、特殊工况下的专项检测
针对极寒、高湿或沙漠等特殊环境,需增加以下检测项目:
- 金属材料低温冲击韧性测试(-40℃环境下)
- 液压油黏温特性曲线测定
- 电气系统绝缘阻抗及防尘防水等级验证
- 防腐涂层附着力与耐盐雾试验(按ISO 9227标准执行)
三、智能化检测技术的应用
现代检测体系已引入三维激光扫描技术建立车体数字孪生模型,通过应变片组网实现关键部位应力状态的实时监测。基于物联网的预测性维护系统可对液压油污染度、轴承振动频谱等参数进行趋势分析,提前预警部件失效风险。检测数据自动录入区块链平台,确保检测报告的可追溯性和防篡改性。
四、检测周期与管理规范
根据API Spec 4F标准,常规检测应每500作业小时或6个月实施一次(以先到为准),大修后需进行150%额定载荷的破坏性试验。所有检测记录须包含:检测时间、项目清单、测量数据、问题描述及整改措施,并由三级责任人员(检测员、工程师、安全主管)联签确认。
通过全方位、多维度的检测体系,立放井架车的使用寿命可延长30%以上,重大故障率降低至0.2次/万小时以下,为石油钻井行业实现本质安全提供了坚实基础。
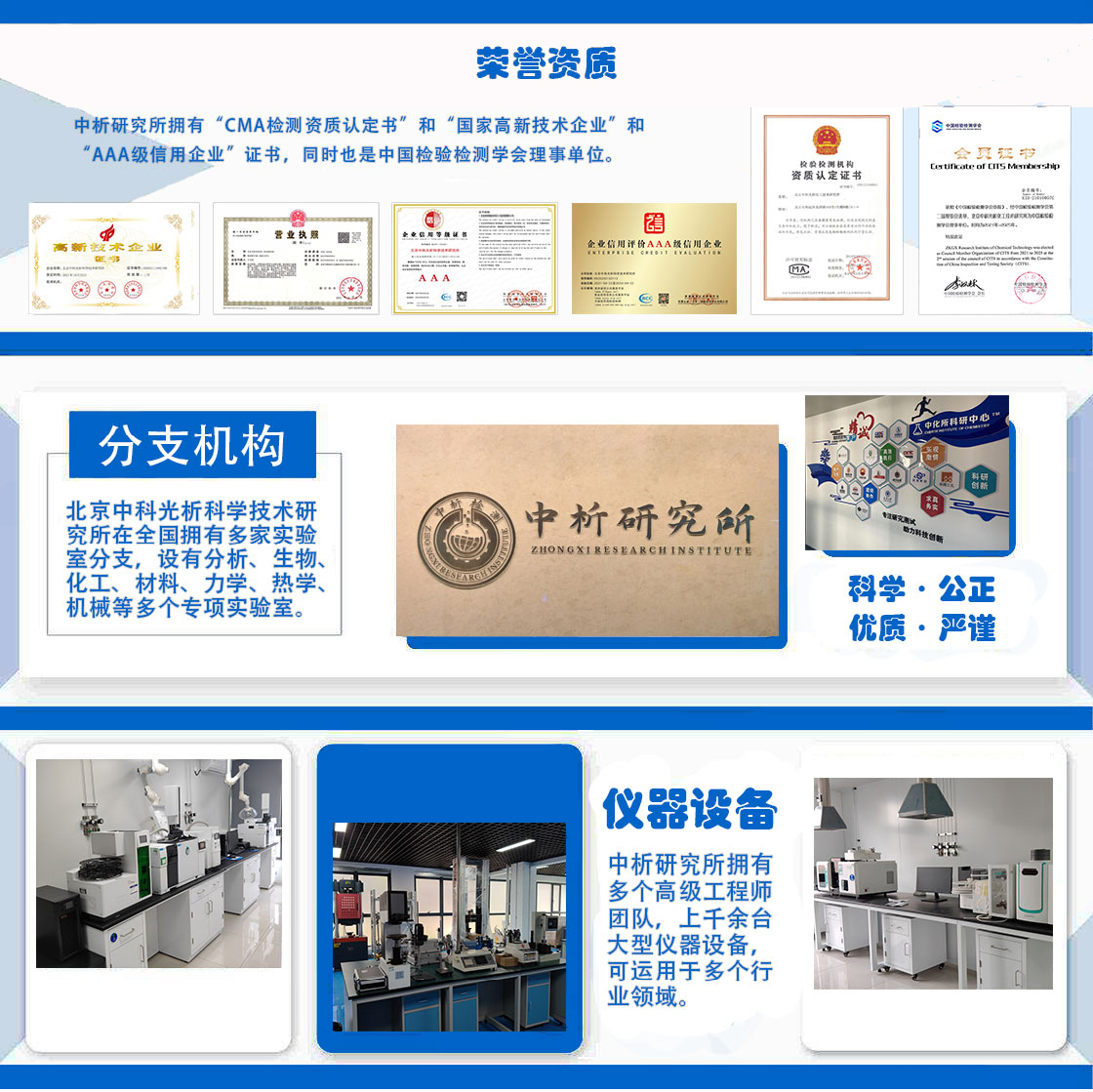
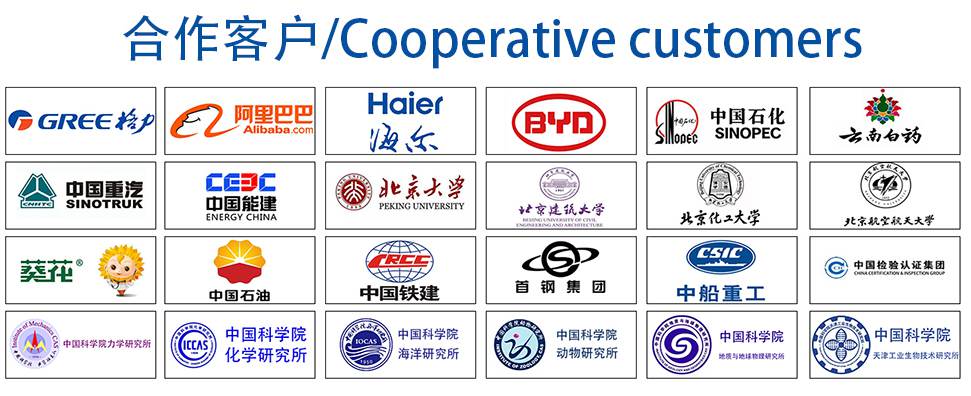