液化气体汽车罐车检测的重要性与技术要求
液化气体汽车罐车作为危险化学品运输的核心工具,其安全性和可靠性直接关系到公共安全与环境保护。由于罐体长期承受高压、低温或高温环境,以及运输过程中振动、碰撞等复杂工况,定期开展全面检测是保障运营安全的关键环节。根据《压力容器安全技术监察规程》及相关国家标准,液化气体汽车罐车需至少每年度进行一次全面检验,新罐车首次使用前还需通过型式试验和出厂检测。
核心检测项目及内容
1. 罐体结构完整性检测
通过目视检查、超声波测厚仪、磁粉探伤等手段对罐体焊缝、封头、接管等关键部位进行检测,重点关注腐蚀、裂纹、变形等缺陷。罐体壁厚测量需覆盖典型部位,实测值不得低于设计厚度的90%。
2. 安全附件功能性验证
包括安全阀爆破压力测试(需达到标称压力的1.05-1.1倍)、紧急切断阀响应时间检测(≤5秒)、压力表精度校验(误差≤±1.6%)。同时检查液位计、温度计等附属仪表的灵敏度与可靠性。
3. 材料性能评估
对罐体母材及焊接接头进行金相分析、冲击试验和硬度测试,确保材料在低温(-40℃)工况下的韧性指标符合GB/T 18442标准。重点监测应力腐蚀开裂倾向,尤其是LNG罐车使用的奥氏体不锈钢材料。
4. 密封性试验
采用0.2MPa气压进行保压试验,30分钟内压降不得超过试验压力的10%。真空夹层罐需额外进行真空度测试,年泄漏率应小于2×10^-3Pa·m³/s。
5. 装卸系统可靠性检测
检查液相/气相管路阀门密封性能,测试紧急脱离装置在设定拉力(通常为2000N)下的分离功能。对装卸软管进行1.5倍工作压力的强度试验,保压时间不少于5分钟。
6. 环境适应性测试
通过振动试验台模拟运输工况,监测罐体固有频率是否避开常见路面激励频率(3-25Hz)。对防护栏、防波板等安全装置进行碰撞能量吸收测试,确保其能承受不低于50kJ的冲击能量。
检测结果判定与后续管理
检测机构需依据TSG R0005-2011标准出具分级报告:Ⅰ类缺陷(立即停用)、Ⅱ类缺陷(限期整改)、Ⅲ类缺陷(观察使用)。所有检测数据应录入车载电子标签系统,并与交管部门监管平台实时对接。对于使用超过15年的罐车,建议增加检测频次至每半年一次。
通过系统化的检测流程,可有效预防因材料疲劳、机械损伤导致的泄漏事故。据应急管理部统计数据显示,规范开展检测的罐车运营单位事故率较未检测单位降低87%,充分证明科学检测对保障特种设备安全运行的核心作用。
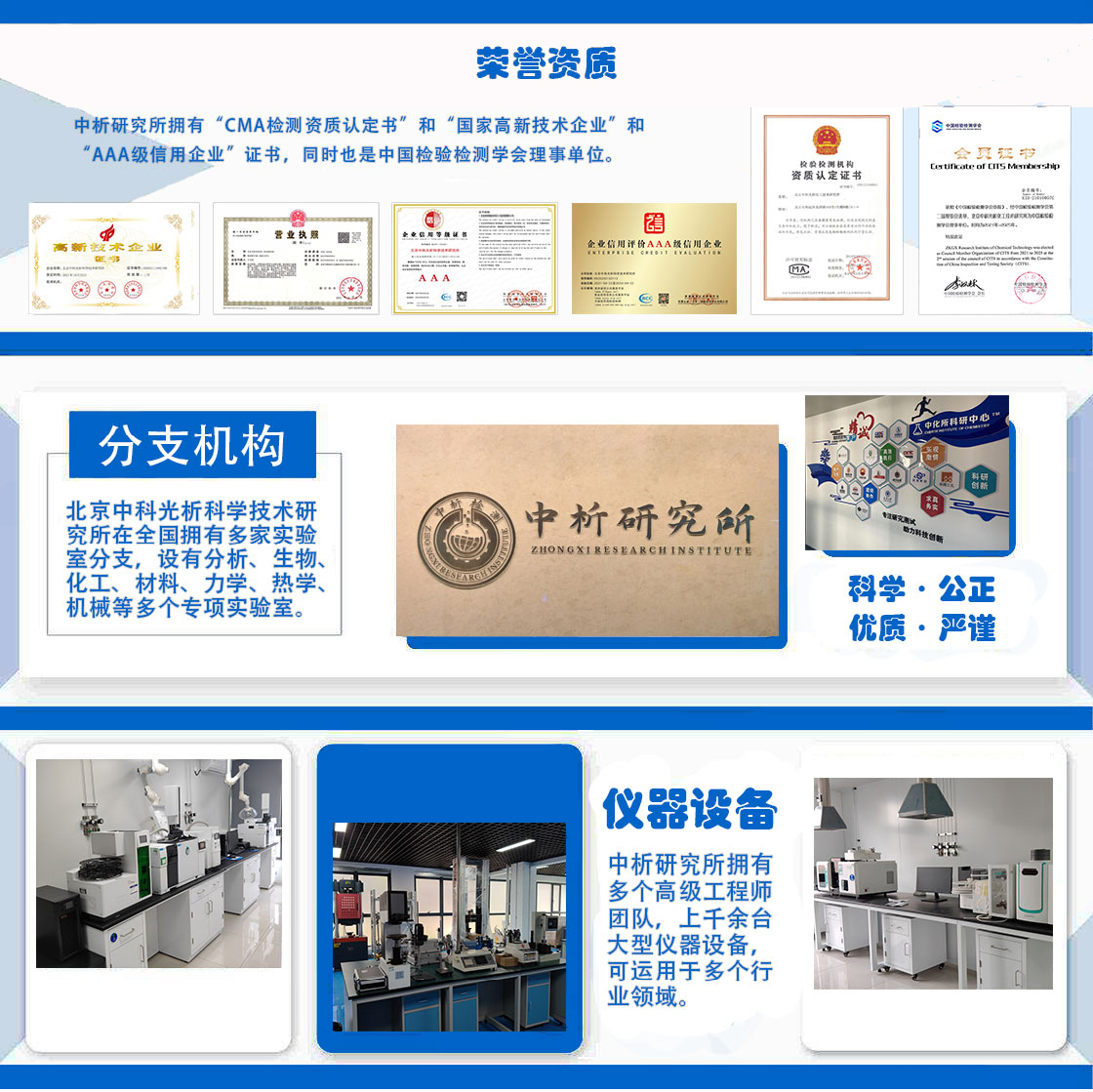
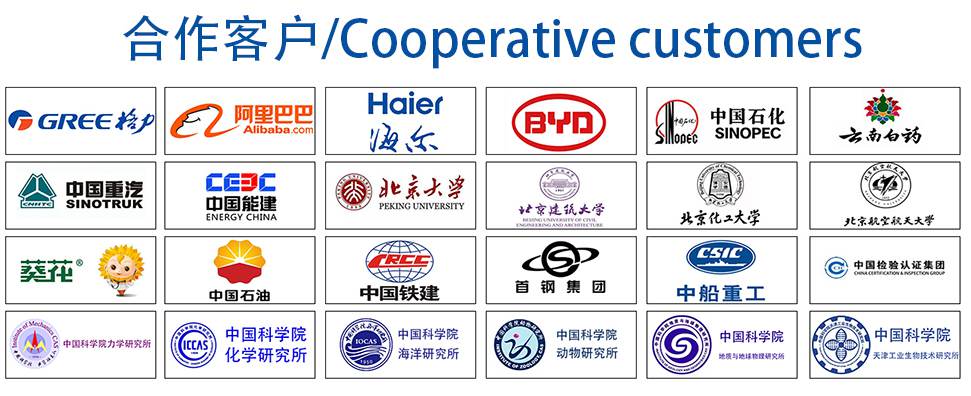