压裂成套装备检测的意义与技术要点
压裂成套装备作为油气田增产改造的核心设备,其性能稳定性和安全性直接关系到作业效率与施工安全。随着非常规油气资源开发规模的扩大,压裂装备正朝着大功率、智能化和连续作业方向发展,对检测技术提出了更高要求。通过系统性检测,不仅能保障设备在高压、高腐蚀等极端工况下的可靠运行,还能降低非计划停机风险,提升能源开发的经济效益。
主要检测项目概述
压裂成套装备检测体系包含四大核心模块:动力系统、流体处理单元、控制单元和辅助装置。每个模块需执行超过60项专项检测,涵盖机械性能、电气安全、材料强度、密封性能等关键指标。采用动态监测与静态测试相结合的方法,确保设备在全生命周期内满足API 6A、ISO 13534等国际标准要求。
动力系统专项检测
针对压裂车柴油发动机和传动装置,重点检测:功率输出稳定性(±2%误差范围)、曲轴箱压力波动(持续监测2小时)、燃油喷射精度(0.01mm级测量)。采用振动频谱分析和热成像技术,可提前发现轴承磨损等潜在故障。涡轮增压器效能检测要求达到额定增压值的95%以上。
高压管汇完整性检测
包含三级检测流程:宏观检查(100%表面磁粉探伤)、壁厚测量(每米5个测点)、爆破压力试验(1.5倍工作压力保压30分钟)。运用超声波相控阵技术检测焊缝质量,要求缺陷回波低于DAC曲线20%。法兰密封面平面度需控制在0.05mm/m以内,确保万向节连接处的零泄漏。
智能控制系统验证
对PLC控制模块进行72小时不间断压力闭环测试,验证PID调节响应时间(≤0.5s)。数据采集系统需满足2000个测点/秒的采样频率,精度等级达到0.25级。冗余通信系统的故障切换时间应小于50ms,HMI界面响应延迟不超过0.2秒。特别要验证极端工况下的自动急停功能可靠性。
检测技术创新方向
当前重点发展基于数字孪生的预测性检测技术,通过植入200+个智能传感器实现实时状态监控。应用机器学习算法分析历史检测数据,可提前30天预警关键部件失效风险。新型声发射检测装置能捕捉到0.1mm级的裂缝扩展信号,检测效率较传统方法提升40%。
第三方检测认证体系
权威检测机构执行第三方验证时,需依据SY/T 6128-2022标准建立检测矩阵。对检测设备要求包括:压力校准装置精度0.05级(国家级计量认证)、流量计标定系统不确定度≤0.2%、数据记录仪采样间隔≤10ms。检测报告必须包含完整的原始数据链和趋势分析图表。
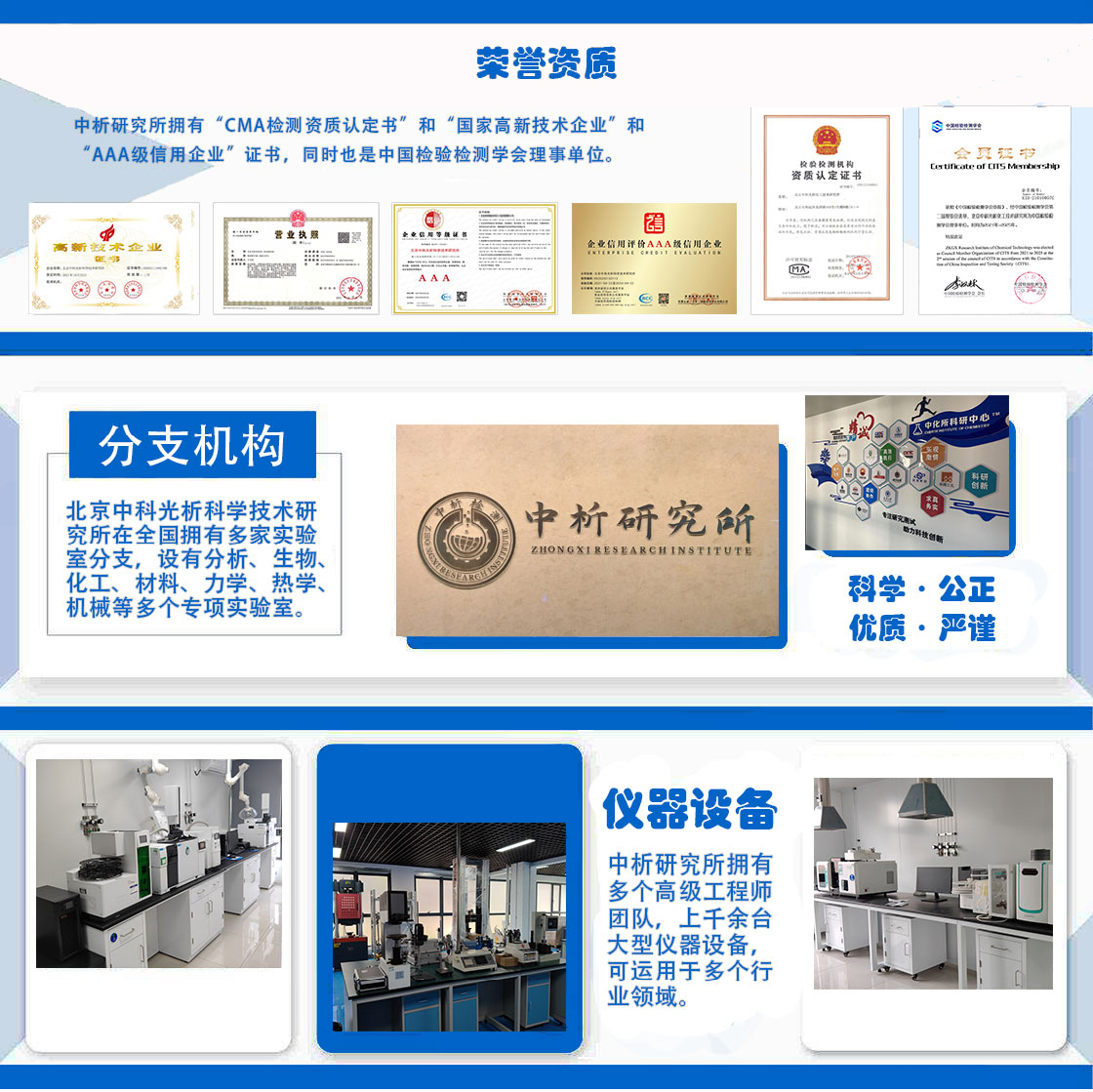
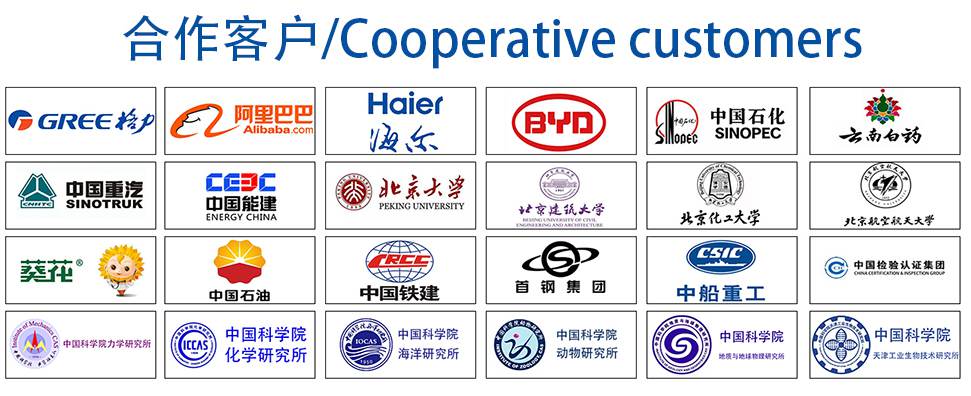