引出端及整体安装件检测的重要性
在工业制造与设备安装中,引出端及整体安装件作为连接系统与外部环境的关键组件,其可靠性直接影响到设备的运行安全、使用寿命及整体性能。引出端通常用于电力、信号或流体传输的接口,而整体安装件则承担机械支撑与结构固定的功能。若这些部件存在尺寸偏差、材料缺陷或安装不当,可能导致漏电、泄漏、振动超标甚至结构失效等严重后果。因此,通过科学系统的检测项目确保其质量符合标准,已成为工程验收和日常维护的核心环节。
核心检测项目及实施方法
1. 几何尺寸与形位公差检测:使用三坐标测量仪、激光扫描仪等设备,对引出端的孔径、螺纹精度、安装件的平面度、垂直度等参数进行数字化分析,确保与设计图纸的误差控制在±0.05mm以内。
2. 材料性能验证:通过光谱分析仪检测金属材质成分,结合硬度计、拉伸试验机评估材料的抗拉强度、屈服强度和延伸率,避免因材质不达标导致的应力断裂风险。
3. 密封与绝缘性能测试:对流体引出端进行气压/水压密封试验(通常要求1.5倍工作压力保持30分钟无泄漏),电气引出端则需通过2500V耐压测试和绝缘电阻测量(≥100MΩ)。
4. 动态负载模拟:利用振动试验台模拟实际工况,检测安装件在频率5-2000Hz、加速度10g条件下的抗振性能,同时监控引出端连接处是否出现松动或位移。
特殊环境适应性检测
针对极端工况还需开展专项检测:在盐雾试验箱中模拟海洋环境(5%NaCl溶液,35℃持续96小时),评估镀层耐腐蚀性;通过高低温循环试验(-40℃至+85℃循环10次)验证材料热膨胀系数匹配性。对于航空航天领域,还需增加真空出气试验,检测材料在低压环境下的挥发物含量。
数据化检测与趋势分析
现代检测中普遍采用数字孪生技术,将实测数据与3D模型动态比对,实现缺陷可视化定位。同时建立检测数据库,通过统计过程控制(SPC)分析尺寸参数的CPK值,预测工艺波动趋势,为工艺优化提供量化依据。例如某汽车零部件企业通过该体系将安装件不良率从0.8%降至0.12%。
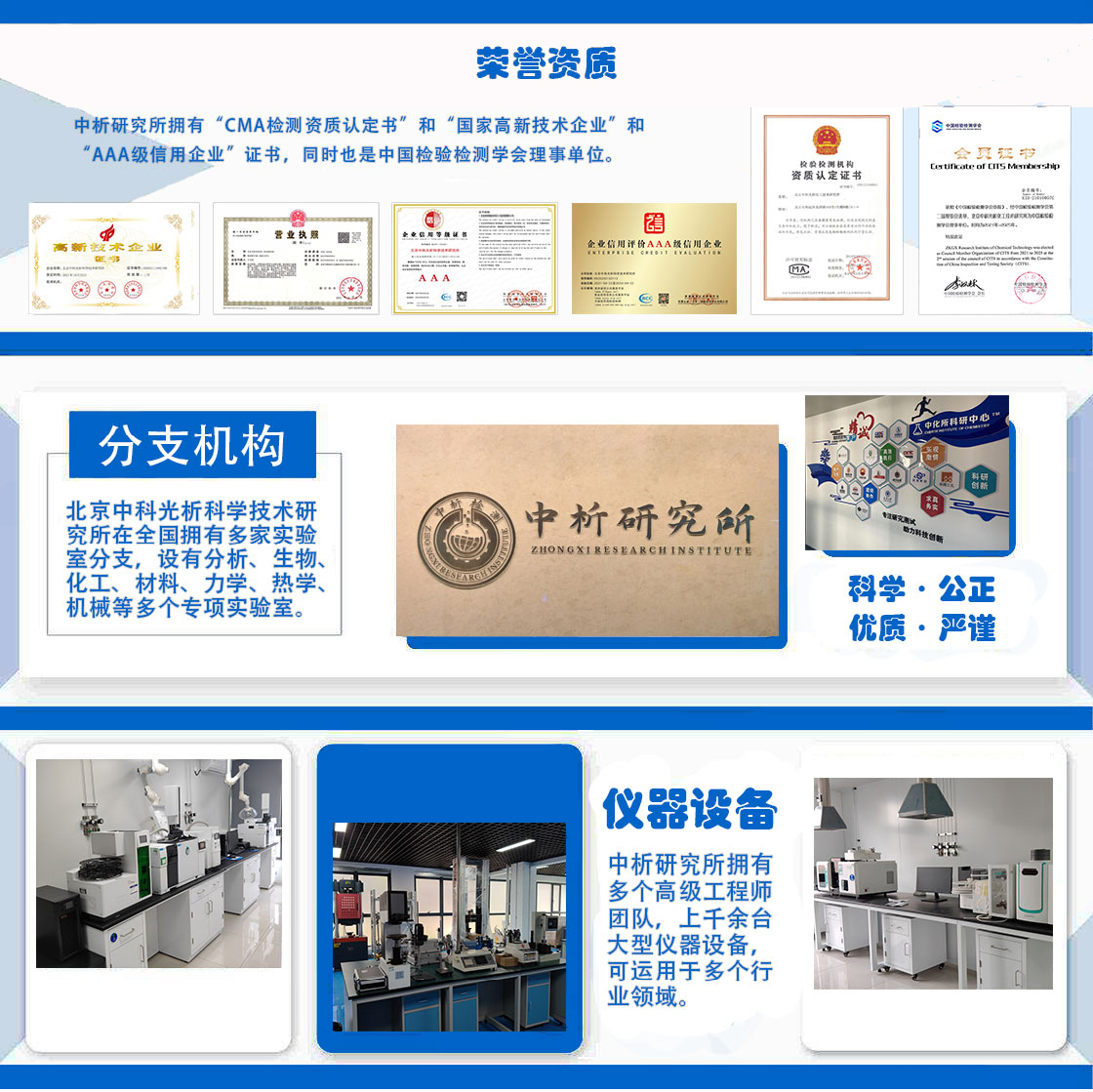
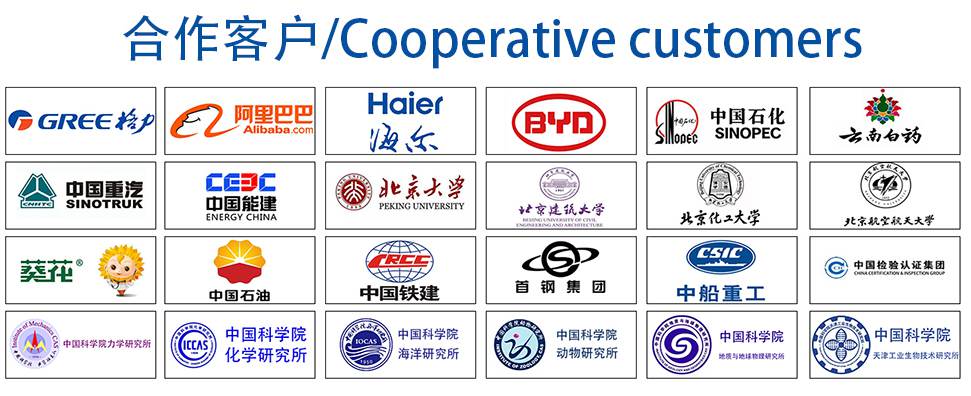