金属切削机床检测的重要性与核心内容
金属切削机床作为制造业中加工零部件的核心设备,其精度、稳定性和安全性直接关系到产品质量和生产效率。随着工业自动化水平的提升,机床的复杂度日益增加,定期开展系统性检测成为保障设备性能、延长使用寿命的必要手段。通过科学的检测项目规划,可及时发现机床潜在故障,避免因设备异常导致的生产停滞或安全事故,同时为工艺优化提供数据支撑。
检测项目分类与技术要点
1. 几何精度检测
通过激光干涉仪、电子水平仪等精密仪器,检测机床导轨直线度、主轴径向跳动、工作台平面度等几何参数。依据ISO 230-1标准,验证机床静态精度是否符合加工要求,确保各运动部件配合误差在允许范围内。
2. 动态性能检测
包含主轴转速稳定性测试、进给系统定位精度验证及加速度响应分析。采用球杆仪测量圆周运动轨迹误差,通过频谱分析诊断传动链异常振动,确保机床在高速加工时的动态精度达标。
3. 安全防护装置检测
检查急停按钮、防护罩联锁装置、过载保护系统的有效性。模拟异常工况触发安全机制,验证防护装置响应时间和动作可靠性,符合GB/T 15706机械安全标准要求。
4. 切削性能综合评估
使用标准试件进行实际切削试验,测量表面粗糙度(Ra≤1.6μm)、尺寸公差(IT6-IT7级)及刀具磨损量。同步记录主轴功率波动和切削力变化,评估机床在不同负载下的能效表现。
5. 电气与控制系统检测
验证伺服驱动器参数匹配性、PLC程序逻辑正确性及传感器信号反馈精度。通过温度巡检仪监测电机温升是否异常,排查线路绝缘老化风险,确保控制系统稳定运行。
6. 润滑与冷却系统检测
采用油液颗粒计数器分析润滑油污染度(NAS 7级以上需更换),检测冷却液pH值(8.5-9.5为合格范围)和流量压力参数。通过红外热像仪观察导轨、丝杠等摩擦副的温升分布,确认润滑效果。
7. 振动与噪声监测
使用加速度传感器采集机床空载/负载状态下的振动频谱,对比ISO 10816振动烈度限值。噪声测试点距设备1米处声压级应≤85dB(A),高频异响需排查轴承或齿轮箱缺陷。
8. 软件功能验证
针对数控系统(如FANUC、SIEMENS)进行G代码解析测试、反向间隙补偿功能验证及多轴联动精度校准。模拟断点续切、刀具半径补偿等复杂工况,确保人机交互界面无逻辑冲突。
检测周期与实施建议
常规检测建议每6个月开展一次,高负荷生产线需缩短至3个月。检测后应生成包含偏差数据、修正方案及趋势分析的综合报告,并建立设备健康档案。通过PDCA循环持续优化检测流程,可降低30%以上的非计划停机损失。
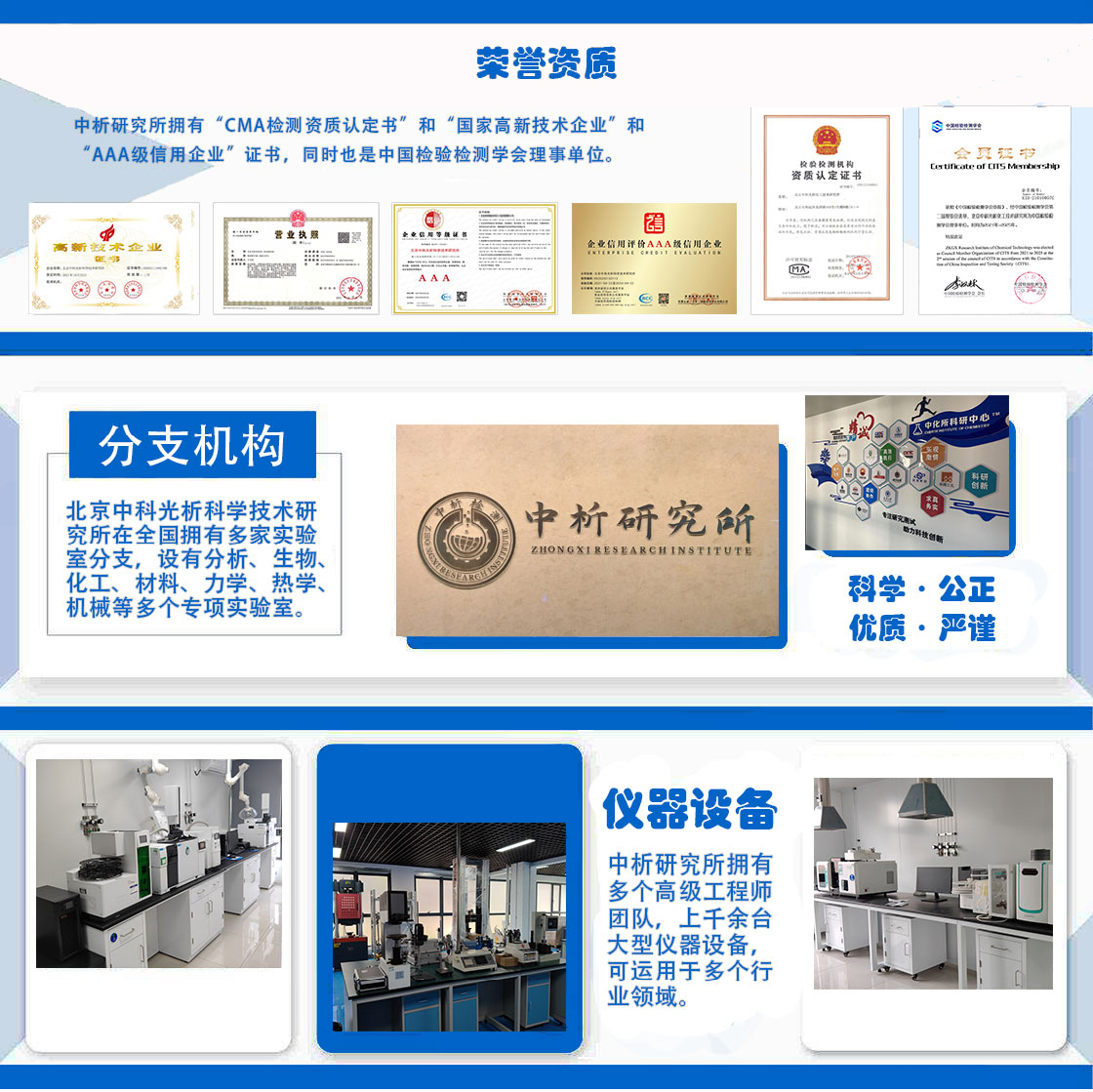
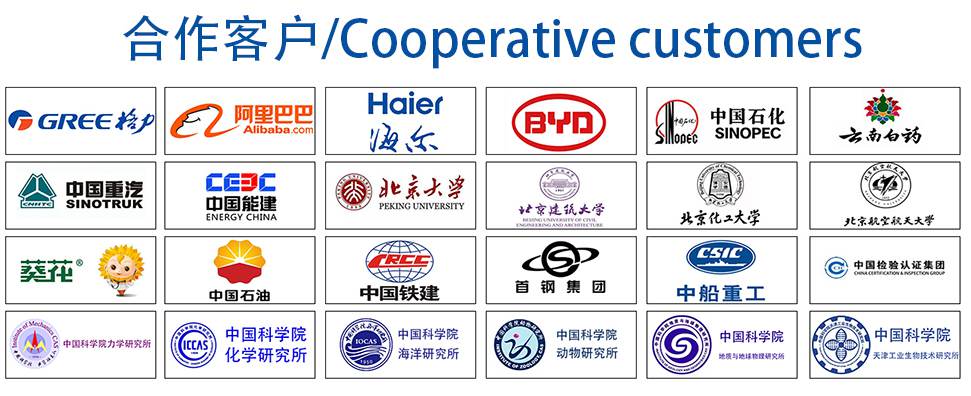