材料及焊缝质量检测的重要性
在工业制造、建筑安装及设备运维领域,材料及焊缝质量直接影响工程安全性与使用寿命。金属材料若存在内部缺陷或成分偏差,焊接工艺若不符合规范,可能导致结构强度不足、耐腐蚀性下降甚至突发性失效。通过系统化的检测手段,可精准识别材料缺陷、焊接工艺问题及服役损伤,从而规避安全隐患,延长设备寿命。尤其对于压力容器、管道系统、桥梁钢构等关键设施,质量检测已成为保障安全运行的强制性要求。
核心检测项目分类
1. 材料成分与性能检测
包括光谱分析(OES)、化学滴定、碳硫分析等,验证材料是否符合设计要求的元素配比。同时需进行力学性能测试(拉伸、冲击、硬度试验)以及金相组织观察,确保材料具备合格的强度、韧性和微观结构稳定性。
2. 焊缝无损检测技术
采用射线检测(RT)、超声波检测(UT)、磁粉检测(MT)和渗透检测(PT)四大主流方法: - RT:通过X/γ射线成像发现焊缝内部气孔、夹渣等缺陷; - UT:利用高频声波定位未熔合、裂纹等深层缺陷; - MT/PT:针对表面及近表面裂纹进行可视化检测。 检测过程需符合ISO 5817、GB/T 3323等标准要求。
3. 焊接工艺评定与质量评估
通过宏观断面分析、弯曲试验和断裂韧性测试,验证焊接接头的力学性能。使用3D扫描仪或工业CT对焊缝几何尺寸(余高、错边量)进行数字化测量,确保符合ASME BPVC或EN ISO 15614规范。对于高温高压环境,还需进行蠕变试验和应力腐蚀测试。
4. 服役状态监测技术
针对在役设备,采用TOFD超声衍射时差法、相控阵超声(PAUT)等齐全技术进行在线监测。结合金属磁记忆检测(MMMT)和声发射技术(AE),可动态捕捉材料应力集中区域和微裂纹扩展趋势,实现预测性维护。
检测标准与智能化发展
检测过程需严格遵循ASTM、ASME、GB/T等国内外标准体系。随着AI技术的应用,基于深度学习的缺陷自动识别系统已逐步替代传统人工判读,检测效率提升50%以上。数字孪生技术的引入,更实现了全生命周期质量数据的可视化追踪。
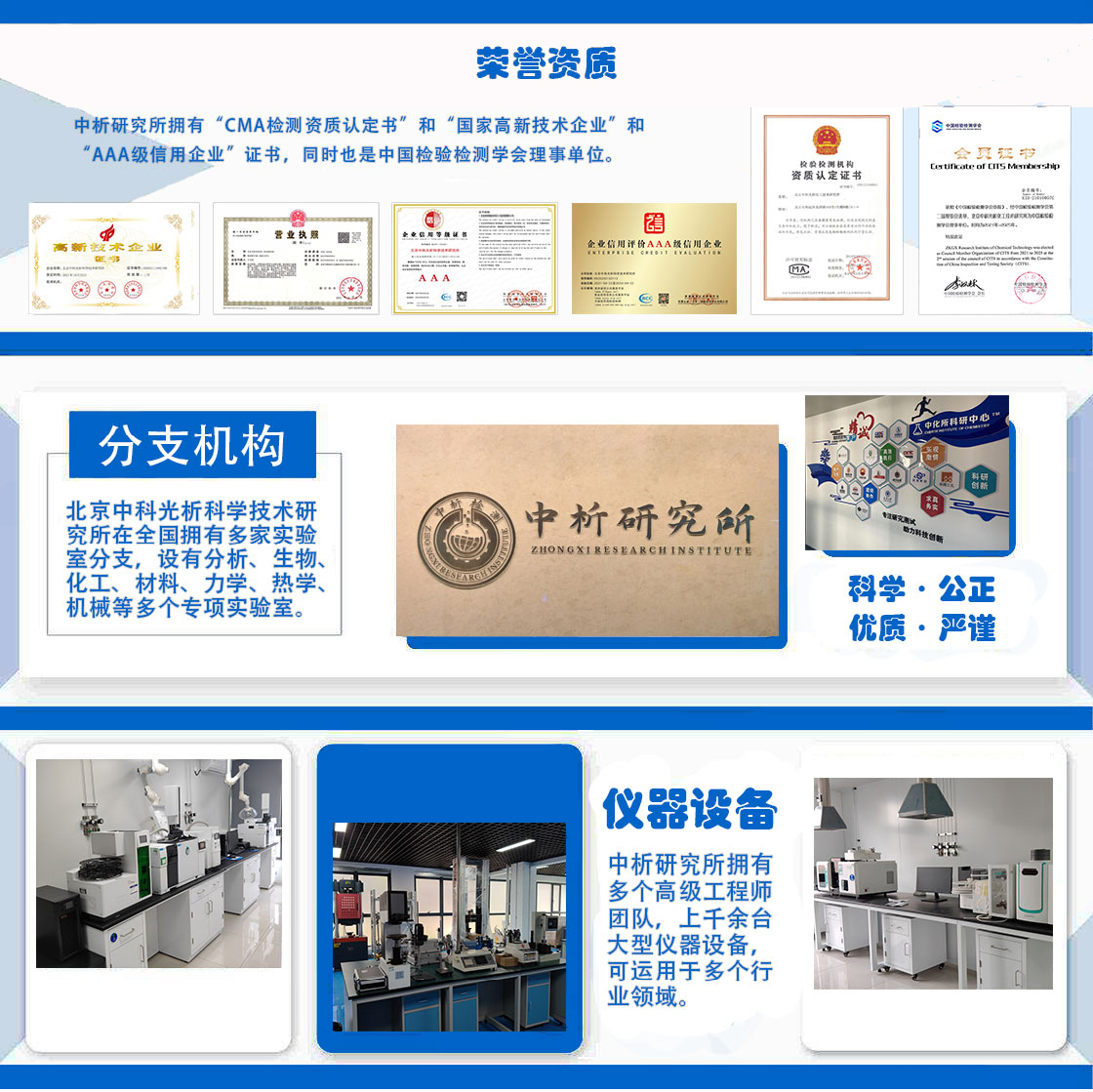
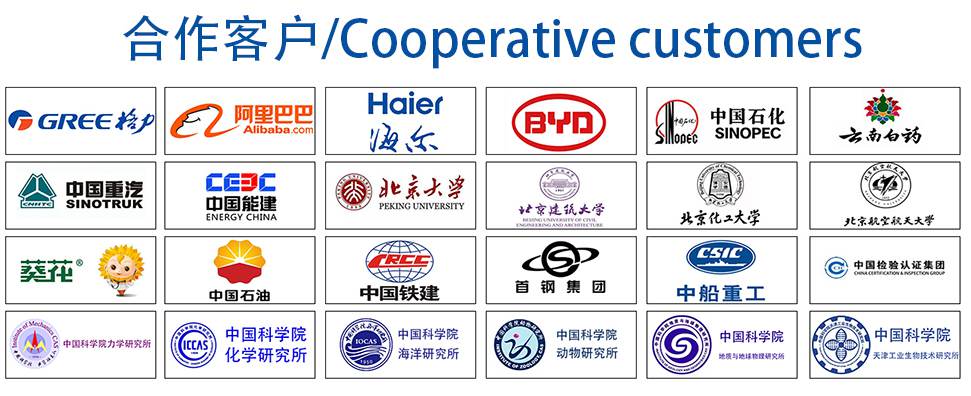