铁路隧道防水板检测的重要性与实施要点
铁路隧道作为交通基础设施的核心组成部分,其防水性能直接影响隧道结构安全、运营寿命及行车环境。防水板作为隧道防水体系中的关键材料,承担着阻隔地下水渗透、保护混凝土结构的重要任务。然而,防水板在施工过程中易受机械损伤、焊接缺陷或材料老化等因素影响,导致防水失效。因此,针对铁路隧道防水板的系统性检测成为工程验收与运维阶段不可或缺的环节。通过科学的检测手段,可有效识别潜在缺陷,保障隧道工程的整体防水效果。
一、外观质量检测
外观检测是防水板质量控制的基础环节,需对防水板的表面完整性、均匀性及施工贴合度进行全面检查。重点观察是否存在划痕、孔洞、褶皱或局部剥离现象,同时核查防水板与基面之间是否密贴无空鼓。对于接缝部位,需使用显微镜或放大镜辅助检查焊接/粘结质量,确保无虚焊、漏焊或黏结不牢等问题。
二、厚度与物理性能检测
防水板厚度直接影响其抗渗能力,需使用超声波测厚仪或机械式测厚仪进行多点抽样测量,确保满足设计要求(通常≥1.2mm)。同时需通过实验室测试验证其物理性能指标,包括拉伸强度(纵向≥16MPa)、断裂伸长率(≥550%)、低温弯折性(-35℃无裂纹)等,这些参数直接反映材料的环境适应性和耐久性。
三、焊缝强度与气密性检测
防水板接缝质量是渗漏风险高发区域,需采用双焊缝热熔焊接工艺并严格检测。使用气压检测仪向焊缝腔内充入0.2MPa压缩空气,保压3分钟后压力下降不超过10%为合格。对于T型接头和十字焊缝,需进行剥离强度试验,要求剥离强度≥6N/mm且破坏模式为母材撕裂。
四、耐水压及渗漏点定位
在隧道衬砌结构完成后,需开展整体防水效果验证。通过注水试验模拟地下水压环境,使用电火花检测仪对全断面进行扫描,利用高压脉冲原理精准识别微小渗漏点。对于发现的缺陷区域,需采用红外热成像技术辅助定位,并结合钻孔取芯法验证渗漏路径。
五、施工过程动态监测
在防水板铺设阶段实施全过程质量跟踪,包括基面平整度检查(凹凸差≤50mm/m²)、缓冲层铺设质量、固定点间距(拱部0.5-0.8m,边墙1.0-1.5m)等。采用数字化监测系统记录施工参数,结合BIM模型进行三维可视化质量管控,实现缺陷的可追溯性管理。
通过以上多维度检测技术的综合应用,可系统评估铁路隧道防水板工程的施工质量,为后续运营维护提供可靠数据支撑。随着智能检测装备(如隧道检测机器人、分布式光纤传感技术)的推广,未来防水板检测将向自动化、智能化方向持续升级,进一步提升检测效率和精度。
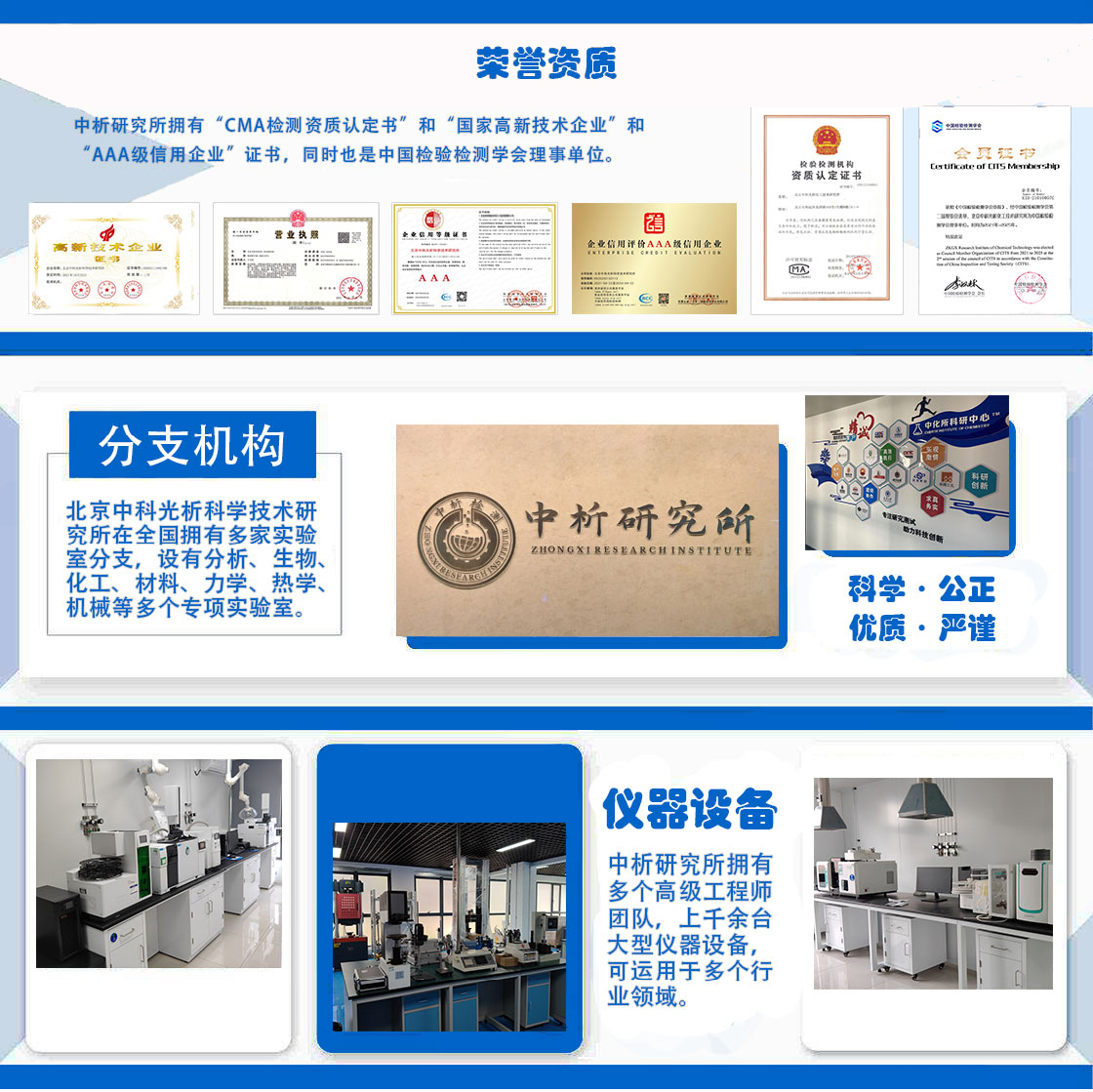
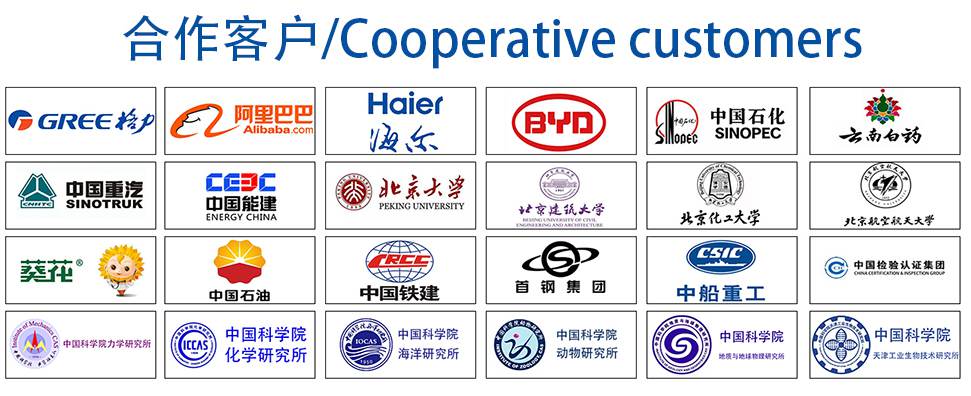