铜管路连接件作为制冷、燃气、供水等系统中的核心组件,其质量直接影响系统的密封性、耐用性与安全性。随着工业标准与用户需求的提升,对铜管连接件的检测已从传统的外观检查延伸至材料性能、力学强度、化学成分等多维度综合评估。规范的检测流程不仅能够筛选出不合格产品,更能通过数据追溯工艺缺陷,为产品改良提供科学依据。
一、外观质量检测
通过目视或10倍放大镜观察表面光洁度、氧化斑点及机械损伤,使用三坐标测量仪检测螺纹精度与管口平整度,依据GB/T 11618标准判定是否存在裂纹、凹陷等缺陷。重点检查焊接部位是否存在虚焊、气孔等影响密封性的问题。
二、材料成分分析
采用光谱分析仪对铜材进行元素测定,要求铜含量≥99.9%,铅、硫等杂质含量需符合ASTM B88标准。同时进行金相分析,观察晶粒尺寸分布是否均匀,避免因晶间腐蚀导致的结构强度下降。
三、力学性能测试
使用万能材料试验机进行拉伸、压缩试验,检测抗拉强度(≥200MPa)和延伸率(≥40%)。通过洛氏硬度计测定维氏硬度值,确保材料在装配过程中具备足够的抗变形能力。
四、密封性能验证
在1.5倍工作压力下进行气密性试验,保压30分钟压力降不超过5%。对于焊接连接件需额外进行氦质谱检漏,漏率应小于1×10⁻⁶ Pa·m³/s。动态模拟测试需包含2000次以上热循环负载。
五、耐腐蚀性评估
参照ISO 9227标准进行盐雾试验,240小时表面无红锈产生。酸性盐溶液浸泡试验中,72小时质量损失率需小于0.15g/m²。特殊应用场景需增加应力腐蚀开裂(SCC)专项检测。
六、尺寸公差检测
使用激光扫描仪对关键尺寸进行全尺寸测量,包括管径公差(±0.05mm)、螺纹中径偏差(≤5μm)、法兰平面度(≤0.02mm/m)等参数,确保与管路系统的兼容匹配性。
通过上述系统性检测,可精准识别铜管路连接件的质量风险点。建议生产企业建立全流程质量追溯体系,第三方检测机构应定期对检测设备进行 认证校准,确保检测数据的准确性与国际互认性。
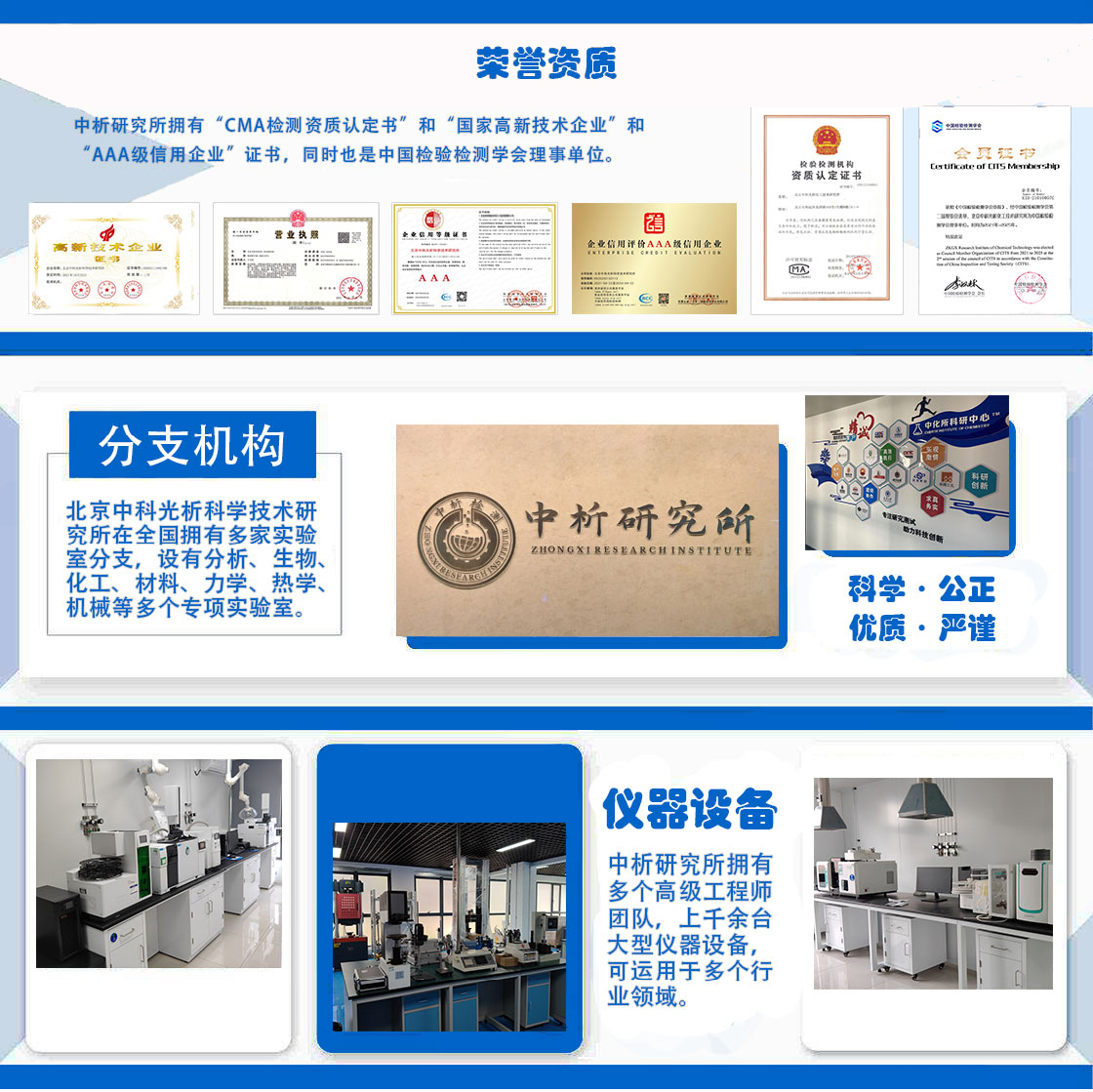
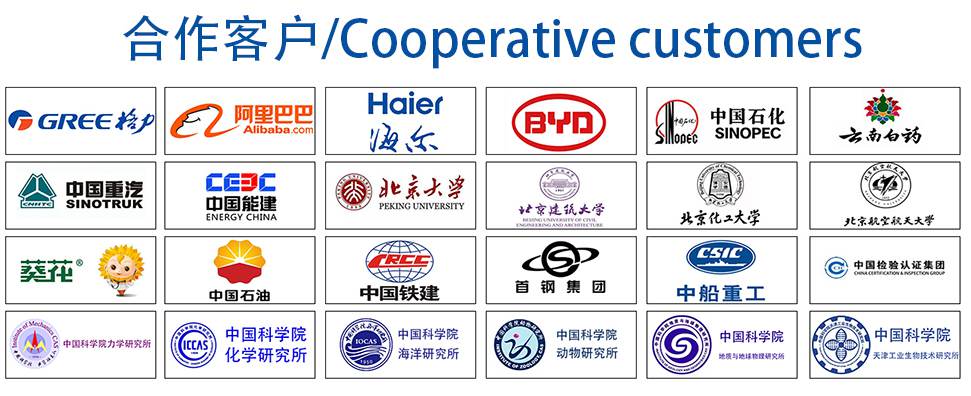