腐蚀环境中涂漆或涂层检测的重要性
在化工、海洋工程、石油炼化等腐蚀性环境中,涂漆或涂层是保护金属基材免受腐蚀的关键屏障。然而,长期暴露于高温、高湿、酸碱性介质或盐雾等恶劣条件下,涂层性能可能因老化、破损或失效而失去防护作用,进而引发设备腐蚀、结构强度下降甚至安全事故。因此,针对腐蚀环境中的涂漆或涂层开展系统性检测,既是保障设备安全运行的必要措施,也是延长设施寿命、降低维护成本的核心环节。
核心检测项目及方法
1. 涂层厚度检测
涂层厚度直接影响其抗渗透性和机械强度。使用磁性测厚仪(针对钢铁基材)或涡流测厚仪(非铁金属)进行多点测量,确保符合设计要求(如ISO 2808标准)。厚度不足易导致防护失效,过厚则可能引发开裂风险。
2. 附着力测试
通过划格法(ASTM D3359)或拉开法(ISO 4624)评估涂层与基材的结合强度。在腐蚀环境中,附着力不足的涂层易发生剥落,导致局部加速腐蚀,需确保测试值≥5MPa(根据应用场景调整标准)。
3. 孔隙率与缺陷检测
采用高压电火花检测(适用于导电基材)或湿海绵法(低压涂层),识别涂层中的针孔、裂纹等缺陷(ASTM D5162)。腐蚀介质可通过孔隙直接接触基材,形成点蚀或缝隙腐蚀。
4. 耐化学介质性能测试
通过浸泡试验(ASTM D1308)或盐雾试验(ASTM B117),模拟实际工况评估涂层的耐蚀性。重点关注涂层起泡、变色、软化等失效现象,并结合电化学阻抗谱(EIS)量化防护性能变化。
5. 老化与耐候性评估
利用紫外加速老化试验(ASTM G154)、循环腐蚀试验(ISO 11997)等,检测涂层在光氧老化、热胀冷缩等复合作用下的耐久性。需监测光泽度变化率、粉化等级等参数(ISO 4628系列标准)。
现场检测的特殊要求
在工业现场检测中,需考虑环境温度、湿度对仪器精度的影响,优先选择防爆型设备。对于无法停机区域,可采用超声波测厚仪(带延迟线探头)或红外热成像技术进行非接触式检测。同时结合目视检查(SSPC-VIS标准)快速筛查明显缺陷,建立动态监测数据库以实现腐蚀防护的全生命周期管理。
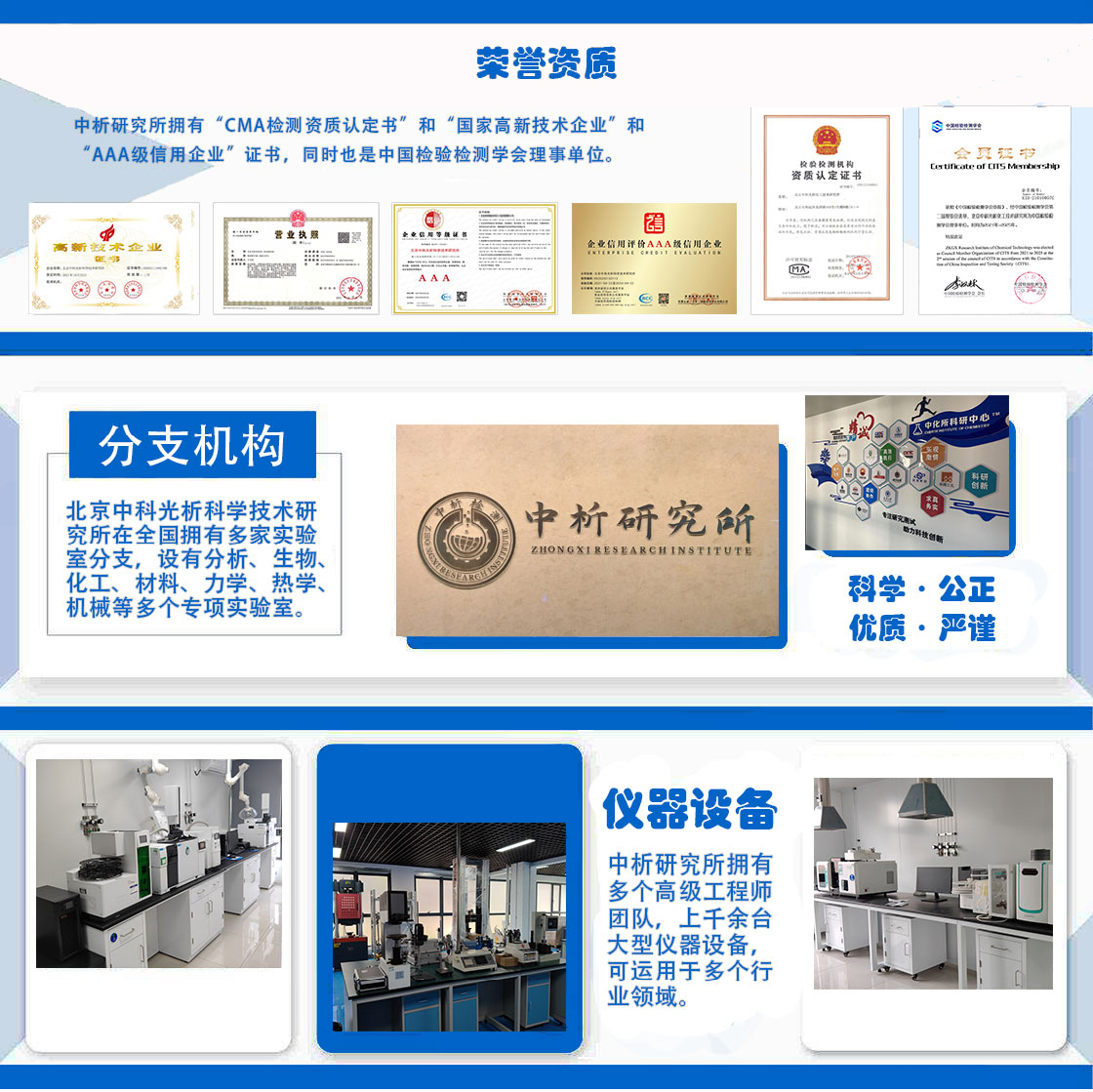
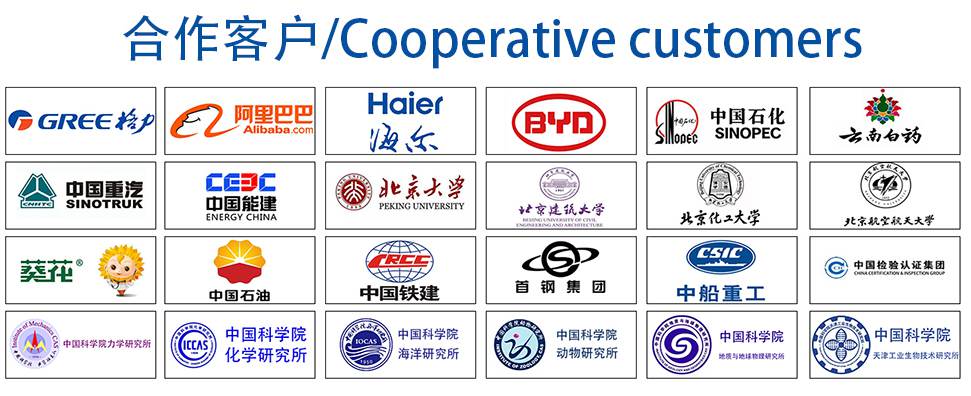