矿用辅助绞车检测的重要性与核心内容
矿用辅助绞车作为矿山井下作业的关键设备,主要用于物料运输、设备牵引及人员升降等场景,其运行安全性和可靠性直接影响矿井生产效率和作业人员生命安全。由于矿井环境复杂,长期处于高湿度、高粉尘、腐蚀性气体等恶劣工况下,绞车易出现机械磨损、电气故障或结构变形等问题。因此,定期开展矿用辅助绞车检测不仅是国家安全生产法规的强制要求,更是预防事故、延长设备寿命的必要手段。
矿用辅助绞车检测的核心项目
1. 结构与机械性能检测
包括绞车机架变形量测量、齿轮箱啮合精度分析、滚筒磨损及裂纹检测、轴承运行温度监测等。通过超声波探伤、磁粉检测等技术对关键焊接部位进行无损检测,确保无疲劳裂纹或材料缺陷。
2. 制动系统安全性测试
重点验证工作制动器与紧急制动器的响应时间、制动力矩及协调性。按照GB/T 3811标准要求,进行空载制动、1.5倍额定载荷制动试验,检测制动盘摩擦系数是否达标,液压/气动系统是否存在泄漏。
3. 电气系统及保护装置检测
涵盖电动机绝缘电阻测试(≥50MΩ)、过载保护装置动作值校验、限位开关灵敏度检查等。通过模拟过卷、松绳等故障状态,验证声光报警装置、紧急断电功能的可靠性。
4. 钢丝绳及导向装置评估
采用磁检测法对钢丝绳断丝率、直径缩减量进行量化分析,检查滑轮组衬套磨损量是否超限(>原厚度30%),确保绳道无异常变形或卡阻风险。
5. 动态性能综合试验
在额定载荷下连续运行4小时,监测振动加速度(≤4.5mm/s²)、噪声水平(≤85dB)及温升参数(轴承温度≤80℃),验证设备在持续作业工况下的稳定性。
检测标准与周期要求
检测工作需严格遵循《煤矿安全规程》(AQ 1029)和《矿山机械安全技术规范》(GB/T 26548),常规检测周期为每6个月一次,新安装或大修后设备需进行72小时满载试运行检测。第三方检测机构还需核查设备防爆认证、MA标志等合规性文件。
通过系统化的检测流程,可及时发现矿用辅助绞车潜在隐患,避免因设备故障导致的停产事故。企业应建立数字化检测档案,结合物联网监测技术实现预测性维护,切实提升矿山安全生产水平。
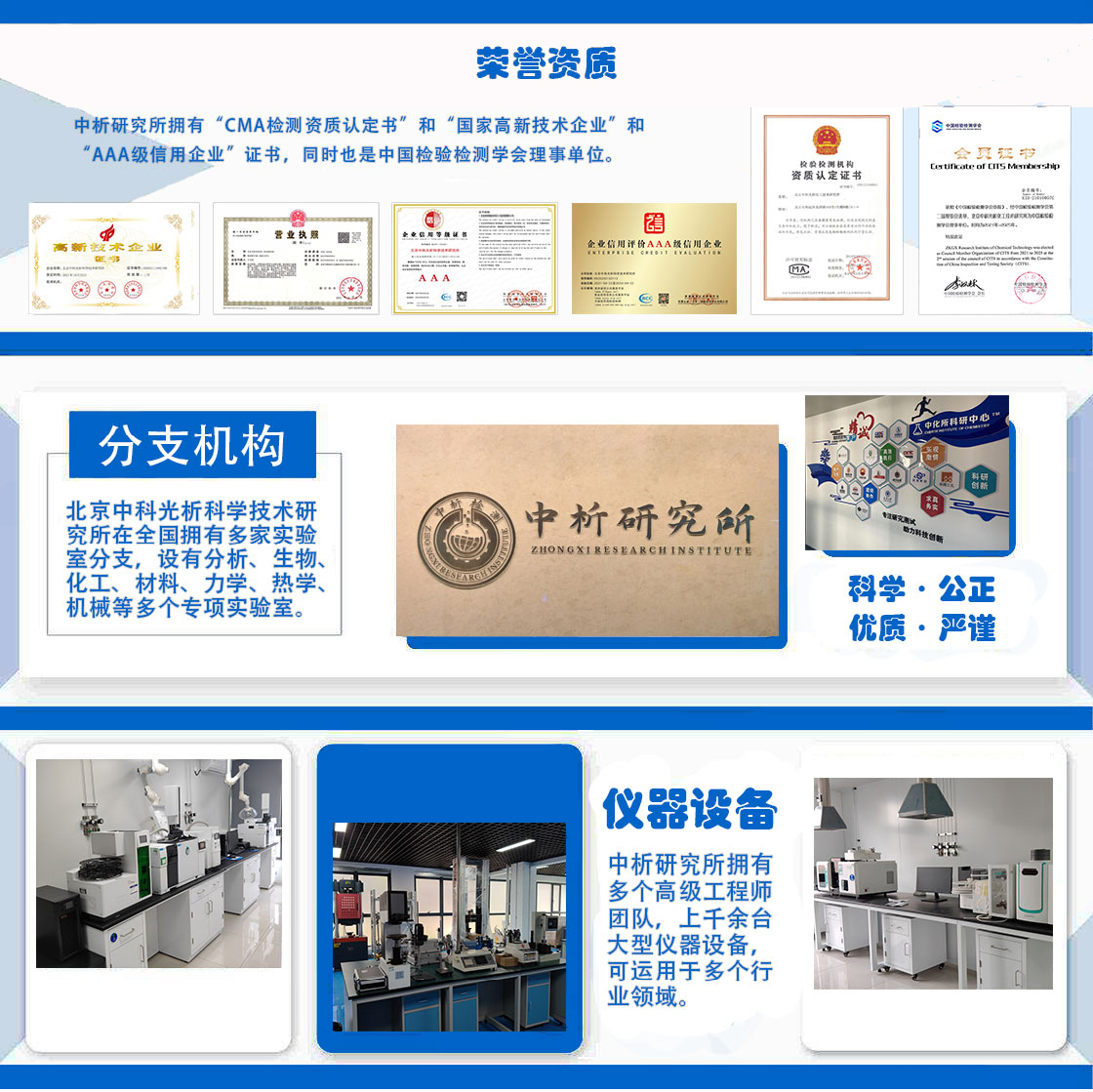
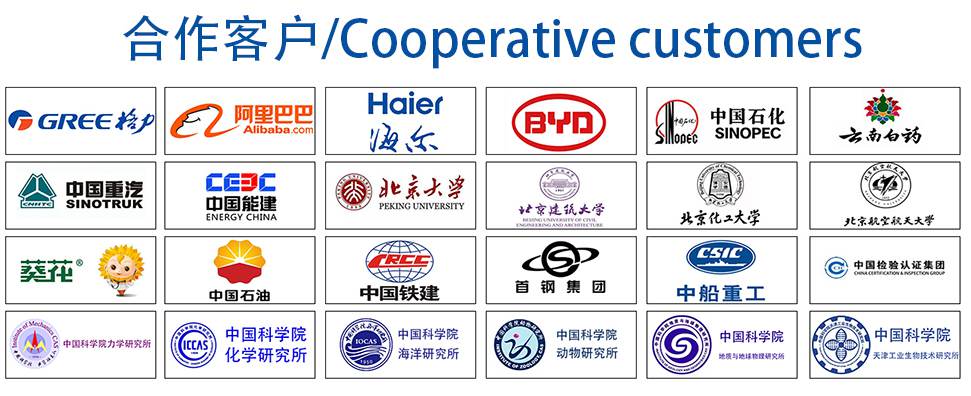