铝及铝合金作为现代工业应用最广泛的金属材料之一,其化学成分直接影响材料的机械性能、耐腐蚀性、焊接性及加工性能。化学成分检测是铝材生产、加工及质量管控的核心环节,贯穿原料验收、熔铸工艺控制、成品检验全流程。通过精准分析元素含量,可确保材料符合GB/T 3190、ASTM B209等国内外标准要求,满足航空航天、汽车制造、电子设备等高端应用场景对材料性能的严苛要求。
一、主元素成分分析
主元素检测涵盖铝基体中占比超过1%的合金元素,包括硅(Si)、铜(Cu)、镁(Mg)、锰(Mn)、锌(Zn)、铁(Fe)等核心成分。通过光电直读光谱法(OES)或X射线荧光光谱法(XRF)进行快速定量,误差范围可控制在±0.02%。例如6061铝合金要求Mg含量0.8-1.2%、Si含量0.4-0.8%,精确配比直接影响T6热处理后的强度指标。
二、杂质元素限量检测
严格控制铅(Pb)、镉(Cd)、汞(Hg)、铬(Cr)等有害元素含量,需采用电感耦合等离子体质谱法(ICP-MS)检测至ppm级精度。特别是食品包装用3003铝合金,要求Pb≤0.01%、Cd≤0.002%,符合GB 4806.9食品安全标准。杂质超标将导致材料脆性增加或引发重金属迁移风险。
三、气体元素检测
熔铸过程中易混入氢(H)、氧(O)、氮(N)等气体元素,使用惰性气体熔融-红外吸收法测定氢含量(≤0.15ml/100g),氧氮分析仪检测氧氮总量(通常≤30ppm)。航空用7075铝合金若氢气含量超标,将产生皮下气泡导致锻件开裂。
四、微量元素分布检测
通过电子探针(EPMA)或扫描电镜-能谱联用(SEM-EDS)进行微区成分分析,评估钛(Ti)、锆(Zr)等晶粒细化剂的分布均匀性。例如添加0.1-0.3%Ti可细化2024铝合金铸态组织,但偏析超过5%会降低时效强化效果。
五、特殊性能关联检测
针对耐蚀铝合金需测定铜当量(Ceq=Cu%+Mn%/6),船用5083铝合金要求Ceq≤0.1%;导电铝材检测铁硅比(Fe/Si>1.7),确保1350电工铝杆电阻率≤0.028μΩ·m。此类专项检测需结合化学成分与物理性能建立数学模型。
现代检测实验室通常配备火花光谱仪、ICP-OES、GD-OES深度剖析仪等设备,结合金相制样与标准物质校准,实现从ppm级到百分比的全元素覆盖检测,为铝合金产品研发与质量管控提供精准数据支撑。
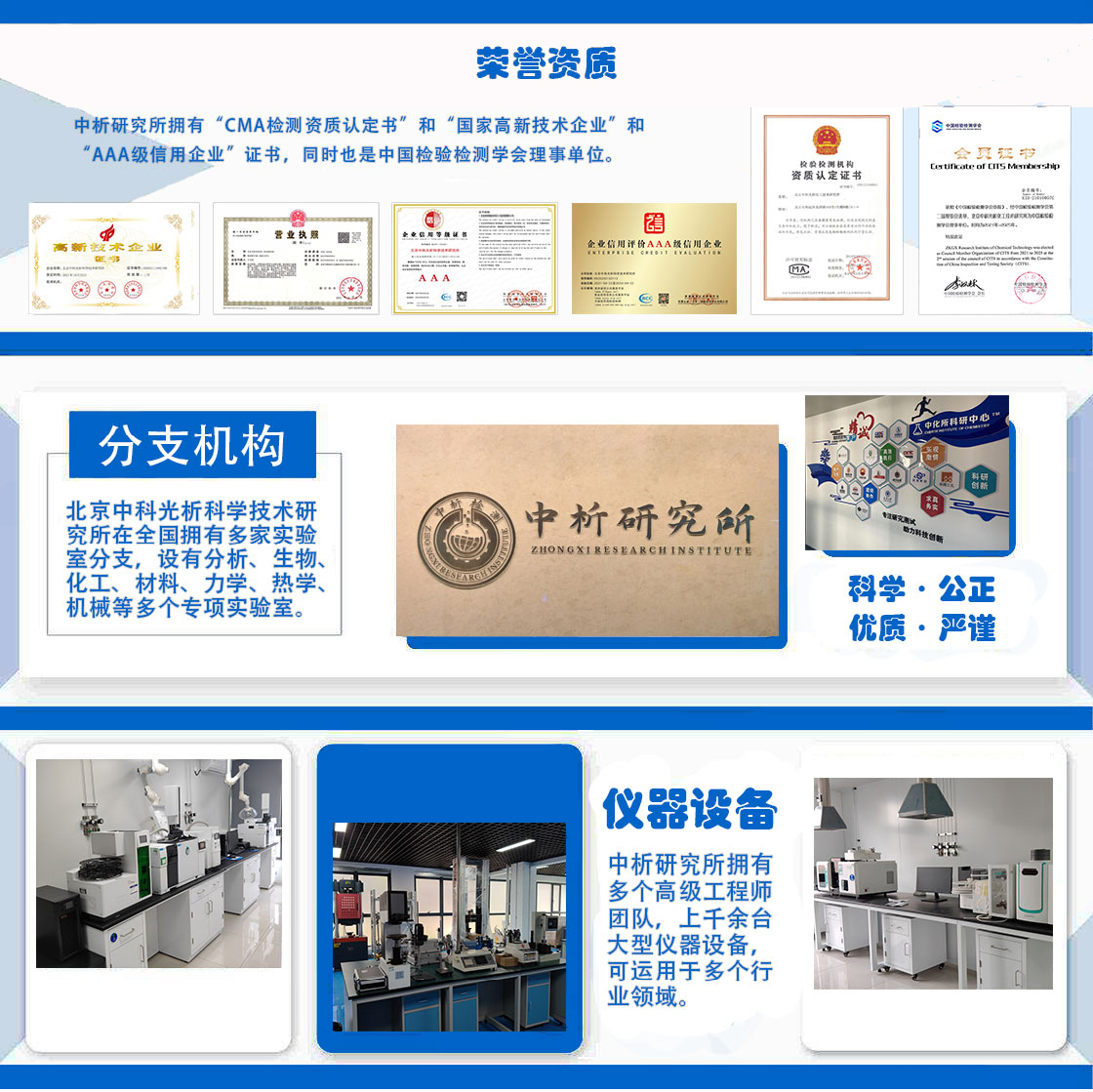
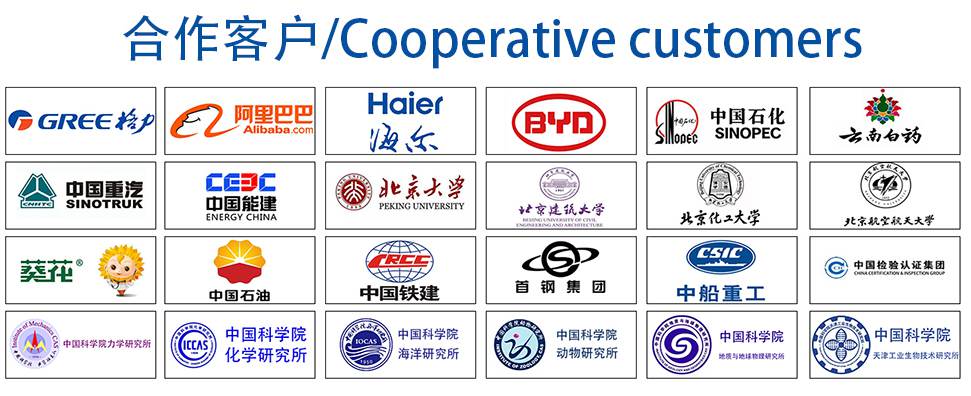