铜及铜合金化学成分检测的重要性
铜及铜合金因优异的导电性、导热性、耐腐蚀性和加工性能,被广泛应用于电力、电子、建筑、机械制造等领域。其性能的稳定性与合金成分的精确配比密切相关,因此化学成分检测成为材料质量控制的核心环节。通过精准的检测分析,可以验证材料是否符合国标(如GB/T 5231、GB/T 2040等)或行业标准要求,避免因成分偏差导致的产品失效、安全隐患或经济损失。
主要检测项目及意义
铜及铜合金的化学成分检测通常包含以下核心项目:
1. 铜含量测定:作为基体元素,铜的纯度直接影响材料的导电性和机械性能。例如纯铜(T2、T3)要求铜含量≥99.90%,而黄铜(H62、H65)则通过降低铜占比并添加锌来提升强度。
2. 合金元素分析:包括锌、锡、镍、铅、铝等元素的定量检测。以锡青铜(QSn6.5-0.1)为例,锡含量需精确控制在6.0%~7.0%,过高会降低塑性,过低则影响耐磨性。
3. 杂质元素检测:对铁、硫、磷、铋、锑等有害杂质的浓度进行严格限制。例如铋含量超过0.002%会导致铜材热脆性,影响轧制加工性能。
4. 气体元素分析:氧、氢等气体含量影响材料的致密性和抗氢脆能力,尤其在无氧铜(TU1、TU2)中要求氧含量≤0.003%。
常用检测方法及原理
1. 火花直读光谱法(OES):通过电弧激发样品表面产生特征光谱,快速测定铜基体中多元素含量,适用于批量检测,精度可达0.001%。
2. X射线荧光光谱法(XRF):无损检测技术,通过X射线激发原子内层电子跃迁,检测特征X射线能量强度,特别适用于镀层或微小样品的成分分析。
3. 电感耦合等离子体发射光谱法(ICP-OES):对溶液样品进行多元素同时测定,检测限低至ppb级,能精准分析微量杂质元素。
4. 化学滴定法:传统湿法分析,通过氧化还原反应或络合反应测定主成分含量,如碘量法测定铜纯度,结果可靠但耗时较长。
检测结果的应用场景
化学成分检测数据不仅用于来料验收和生产过程控制,还可为失效分析提供依据。例如在电缆断芯事故中,通过检测铜导体的氧含量是否超标,可判断是否为材料氧化导致的脆性断裂;在黄铜阀门开裂案例中,铅含量分布不均的检测结果可能揭示铸造工艺缺陷。
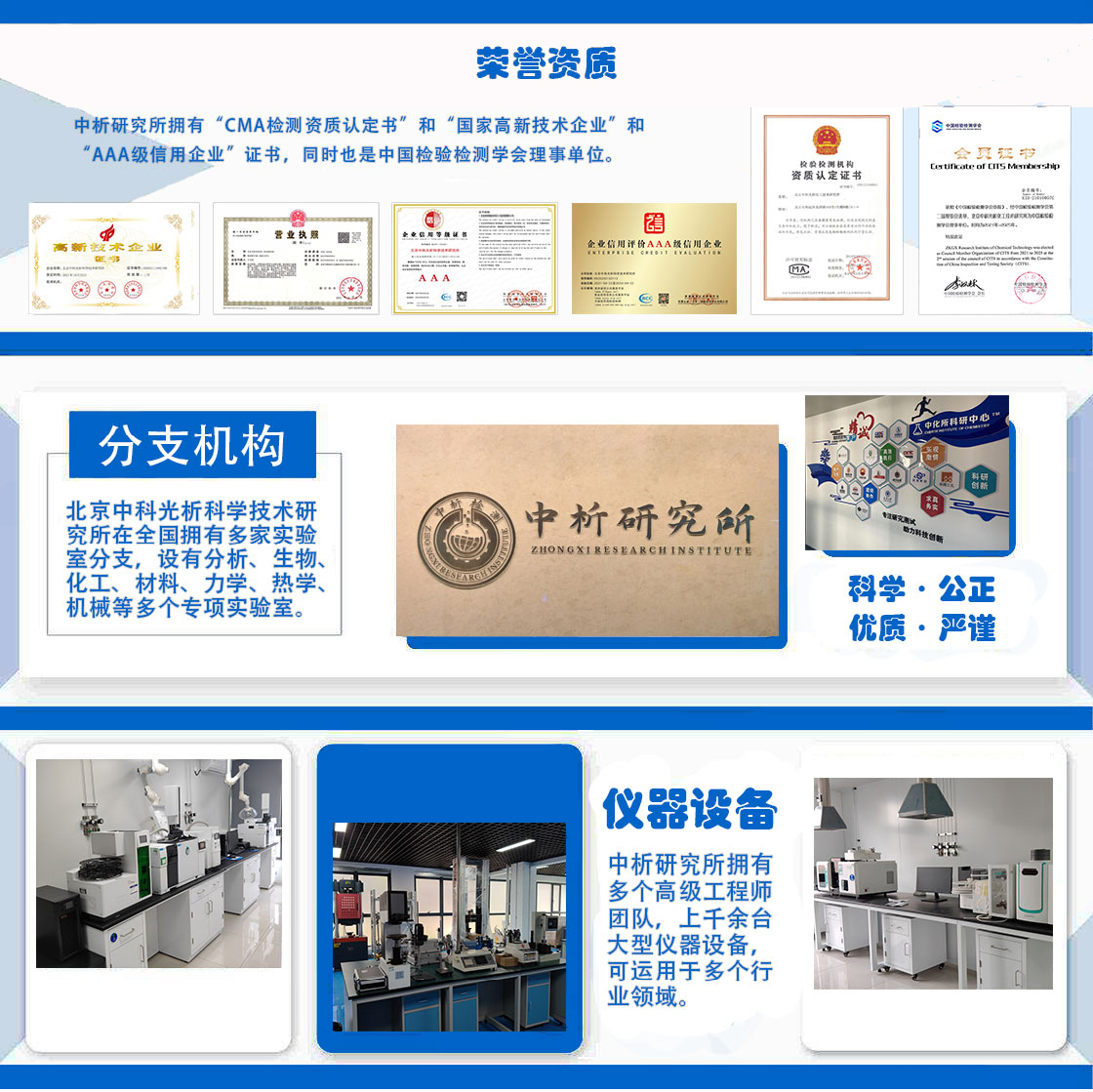
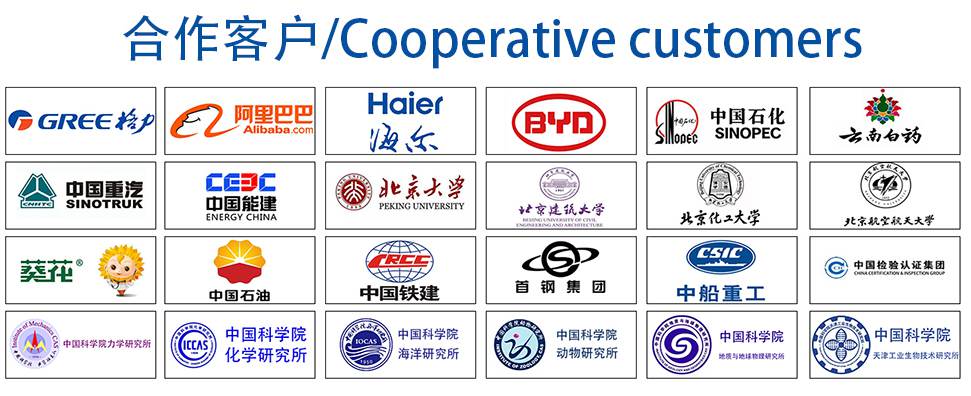