车辆电气/电子部件检测的重要性
随着汽车智能化、电动化趋势的加速,车辆电气/电子部件的复杂性与集成度显著提升。从动力电池管理系统到车载信息娱乐系统,从ADAS传感器到车身控制模块,这些部件的性能直接关系到车辆的安全性、可靠性和用户体验。据统计,现代汽车中电子设备成本占比已超过整车成本的40%,而70%以上的车辆故障与电气/电子系统相关。因此,系统化的电气/电子部件检测成为整车生产、售后维护及质量管理中不可或缺的环节。
核心检测项目分类
车辆电气/电子部件检测主要围绕功能性、安全性及耐久性展开,具体可分为以下关键项目:
1. 电源系统检测
涵盖蓄电池、发电机及配电系统的电压稳定性测试,包括启动瞬间压降、动态负载波动响应(如空调/大灯开启时的电压变化),以及充放电效率验证。通过模拟极端温度(-40℃至85℃)下的性能表现,确保电源系统在全工况下的可靠性。
2. 信号传输与传感器检测
针对CAN/LIN总线、摄像头、雷达、超声波传感器等,需进行信号完整性分析、抗干扰能力测试及响应延迟测量。例如,毫米波雷达需在雨雾、强光等干扰环境下验证目标识别精度,而温度传感器需在快速温变场景中校准数据偏差。
3. ECU(电子控制单元)功能验证
通过HIL(硬件在环)测试台架模拟发动机工况、变速箱换挡逻辑等,验证控制策略的准确性与故障诊断覆盖率。重点检测软件版本兼容性、OTA升级稳定性及网络安全防护能力,防止因程序漏洞导致的功能失效。
4. 线束与连接器耐久测试
使用机械振动台模拟10万公里路试的振动频率,检测线束绝缘层磨损、端子插拔力衰减及接触电阻变化。同时进行盐雾试验(500小时以上)评估防水接插件在腐蚀性环境中的密封性能,避免短路风险。
5. 照明与显示系统评估
针对LED大灯、液晶仪表及HUD抬头显示,需测量光通量维持率(1000小时老化测试)、色温一致性及屏幕刷新延迟。特殊场景下(如隧道进出、强逆光)的自动调光逻辑和响应速度也被纳入关键指标。
6. 电磁兼容性(EMC)测试
依据ISO 11452标准,在电波暗室中执行辐射发射(30MHz-1GHz)与抗扰度测试,确保车载设备在高压电机、无线充电等强电磁场中正常工作。同时验证部件对静电放电(±15kV)、电压瞬变脉冲的防护能力。
检测技术发展趋势
随着域控制器架构的普及,检测重点正从单一部件向系统集成测试转移。AI驱动的故障预测模型、基于数字孪生的虚拟标定技术,以及支持千兆以太网的高速通讯协议测试工具,正在重塑车辆电气/电子检测的效率和精度边界。
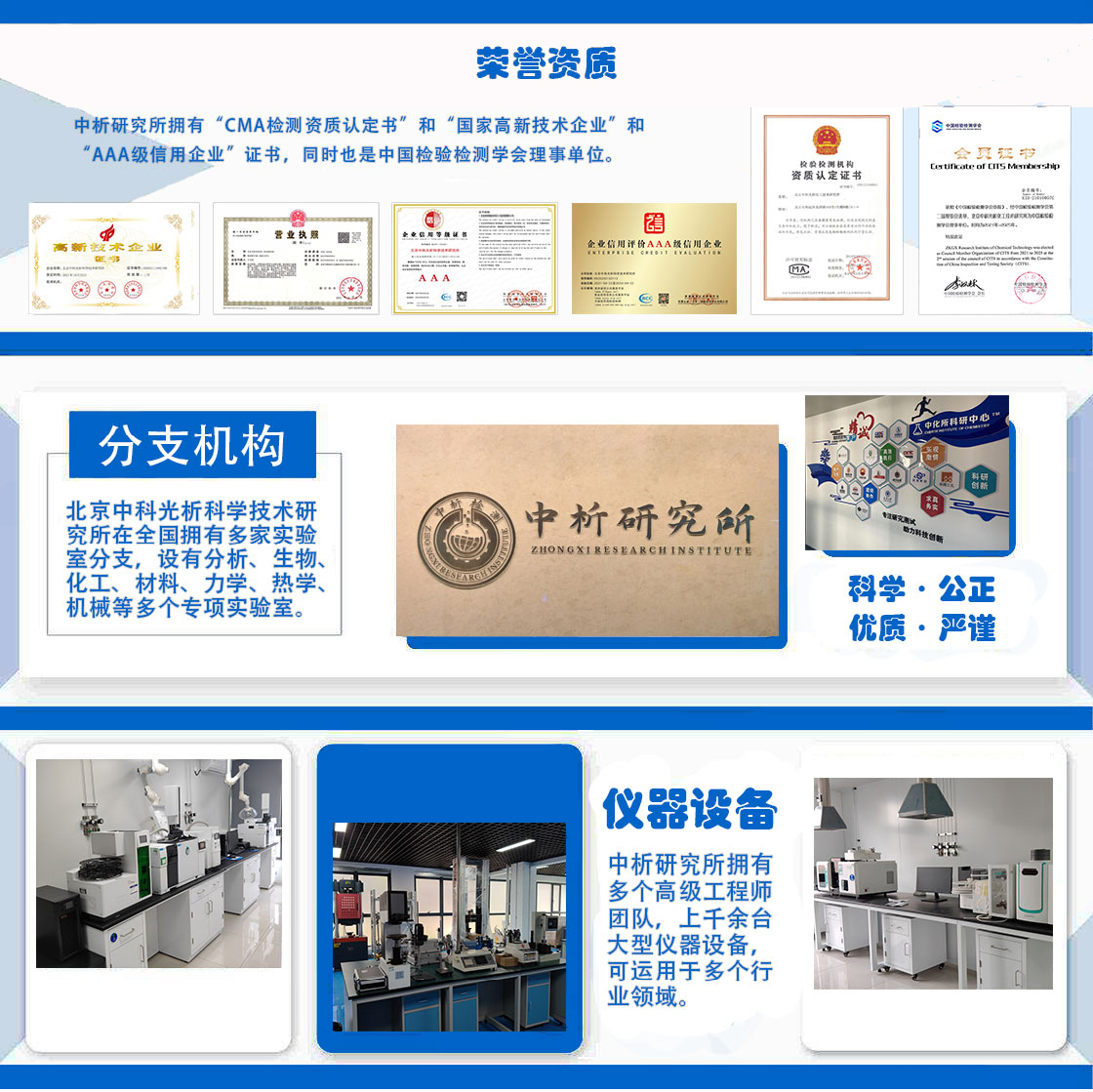
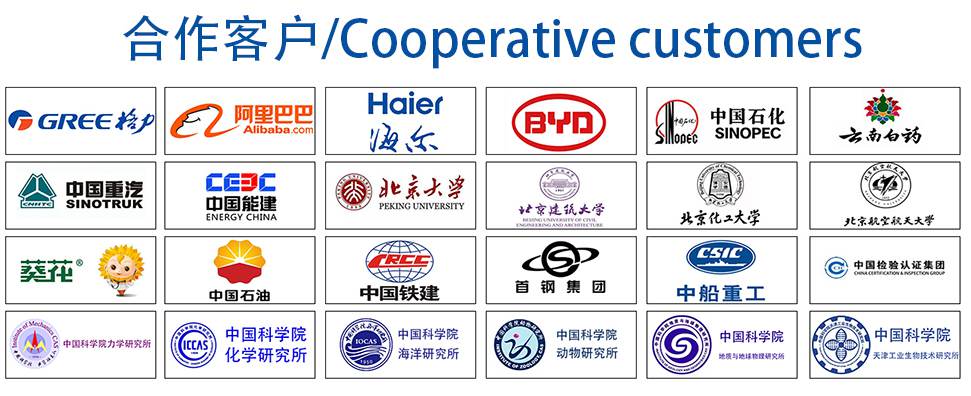