工业燃气检测:以天然气为原料的增效燃气质量控制关键
随着工业燃气应用场景的不断扩大,以天然气为基础原料制备的增效燃气因其清洁、高效的特点,在金属加工、陶瓷烧制、食品烘焙等领域得到广泛应用。增效燃气通过优化天然气成分配比或添加特殊助剂,显著提升燃烧效率和热值稳定性,但其性能指标直接影响生产安全和能源利用效率。因此,建立科学完善的检测体系是保障增效燃气品质的核心环节。
增效燃气核心检测项目解析
1. 基础成分分析
通过气相色谱仪(GC)检测甲烷(CH₄)、乙烷(C₂H₆)等主要烃类含量,确保天然气原料纯度≥95%。同步检测硫化物(H₂S)、二氧化碳(CO₂)等杂质浓度,要求H₂S≤20mg/m³,避免腐蚀设备和污染环境。
2. 热值测定与稳定性验证
采用热量计测定高位热值(HHV)和低位热值(LHV),标准要求达到35-42MJ/m³区间。通过连续采样分析热值波动率,确保生产批次间差异≤3%,保障工业炉窑的燃烧稳定性。
3. 爆炸极限与安全指标检测
依据GB/T 11062标准测定燃气的爆炸上限(UEL)和下限(LEL),重点关注甲烷的LEL(5%)和UEL(15%)范围。同时检测氧气混入量,要求氧含量≤1%,防范回火风险。
4. 增效添加剂定量分析
对添加的富氧剂、催化燃烧剂等特殊成分进行质谱(MS)检测,验证其分布均匀性。例如二甲醚(DME)添加比例需控制在0.5-3%,过量会导致燃烧残留物增加。
5. 燃烧性能综合评估 通过燃烧试验台测定火焰传播速度、燃尽率和NOx排放量,要求燃烧效率≥98%,NOx排放≤150mg/m³。同步检测燃烧后烟气中的CO含量(≤50ppm),确保符合环保标准。
检测流程与技术创新
现代检测体系采用"实验室分析+在线监测"双轨模式。原料入厂阶段进行全组分分析,生产过程配置红外光谱在线检测仪实时监控热值变化,每2小时自动采集样本进行气相色谱复检。新型激光气体分析技术(TDLAS)的应用,使爆炸极限检测响应时间缩短至5秒内,显著提升安全预警能力。
检测数据驱动的应用价值
完整的检测数据不仅用于质量验收,更能指导生产工艺优化。通过关联热值与添加剂配比的数据模型,可动态调整混合比例,使燃气热值标准差从1.8MJ/m³降至0.5MJ/m³。同时,长期检测数据积累为制定企业标准、应对环保核查提供有力支撑。
在"双碳"战略背景下,增效燃气的精准检测已成为行业高质量发展的技术基石。通过建立覆盖原料、生产、应用的全程检测体系,企业可有效提升能源利用效率15-20%,同时降低安全事故风险,实现经济效益与环境效益的双重提升。
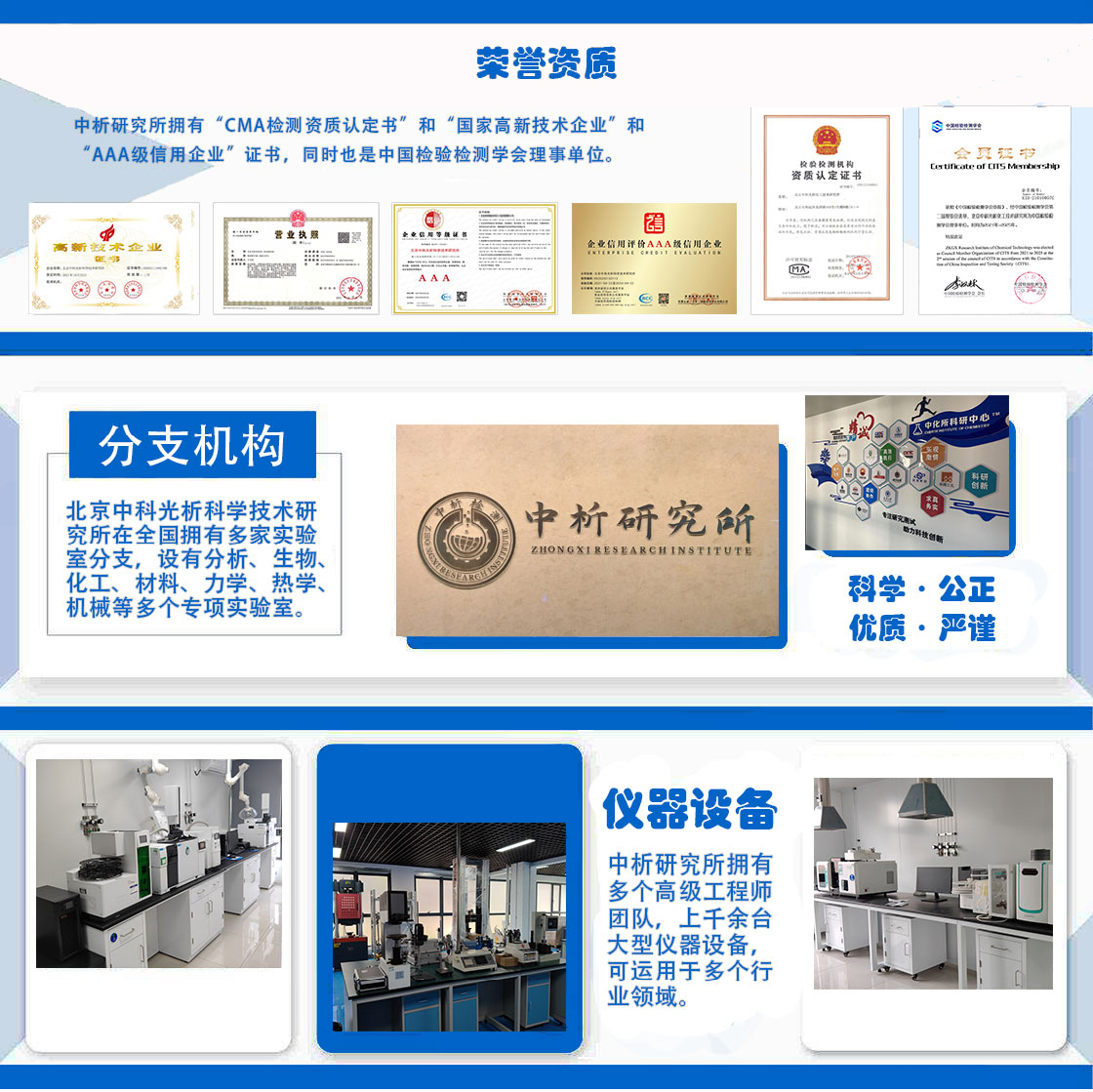
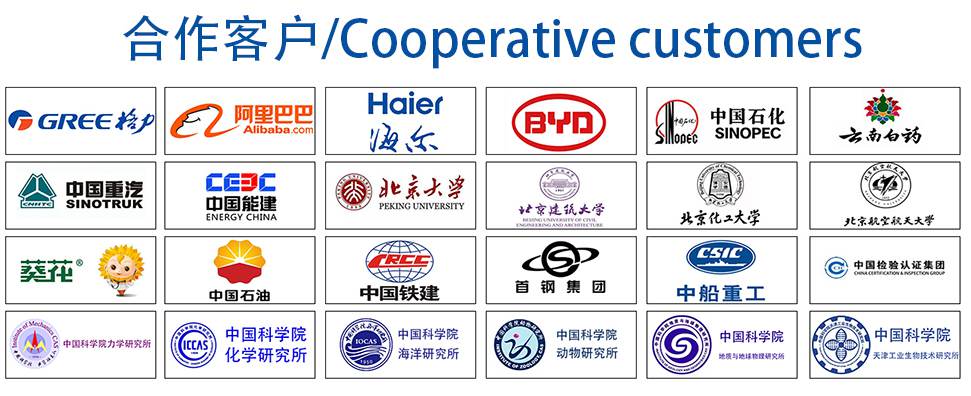