端子与端头检测技术白皮书
随着新能源汽车、智能终端设备及工业自动化领域的快速发展,连接器作为关键电子元件承载着信号传输与能量供给的核心功能。据中国电子元件行业协会2024年报告显示,连接器市场规模突破1200亿美元,其中端子与端头质量直接影响产品失效率,行业平均缺陷成本高达18亿元/年。在高压大电流场景下,接触阻抗超限引发的失效案例占比达37%(国际电工委员会IEC 61238标准统计)。端子与端头检测项目通过智能化检测技术,实现微米级尺寸公差管控与材料性能验证,其核心价值在于提升连接器产品在极端工况下的可靠性,为新能源充电桩、工业机器人等高要求场景提供安全保障。
多模态融合检测技术体系
基于机器视觉与电接触分析的双模态检测系统构成核心技术框架。通过高分辨率工业相机(2000万像素级)捕捉端子表面形貌,结合深度学习算法识别0.01mm级缺损、毛刺等物理缺陷。同步搭载接触阻抗测试模块,采用四线法测量原理,在10A-200A动态电流负载下实现±0.5mΩ精度测量。该技术方案成功应用于新能源汽车连接器接触阻抗测试场景,将批量检测效率提升至1200件/小时,较传统人工检测提升8倍效能。
全流程数字化质控实施路径
项目实施遵循PDCA闭环管理模型,具体流程涵盖:1) 三维建模构建检测基准,运用点云比对技术建立0.005mm精度公差带;2) 在线检测系统集成,通过PLC与MES系统对接实现实时数据追溯;3) 缺陷样本库动态更新机制,基于迁移学习技术持续优化检测算法。在某头部消费电子企业应用中,该流程使Type-C接口端子直通率从92.4%提升至99.6%,年度质量成本降低2300万元。
跨行业应用实践与效益分析
在工业机器人线束端子可靠性验证领域,项目团队开发了高频插拔测试平台。模拟50万次插拔循环后,采用X射线荧光光谱法分析镀层磨损情况,结合有限元仿真验证接触压力衰减曲线。某汽车零部件供应商应用该方案后,将连接器MTBF(平均无故障时间)从15万次提升至28万次,满足ISO 16750-3振动测试标准要求。典型案例显示,每提升1%的端子接触可靠性,可为整车厂减少因线束故障导致的召回风险约7.2%。
全生命周期质量保障架构
构建涵盖原材料、工艺过程及服役性能的三级质量防线:1) 原材料端实施ICP-OES光谱检测,确保铜合金C18150铬含量控制在0.6-0.8%;2) 冲压工序部署在线SPC系统,关键尺寸CPK值稳定在1.67以上;3) 老化测试舱模拟-40℃至125℃温变冲击,验证端子抗应力松弛性能。通过该体系,某储能系统连接器供应商成功通过UL 1977认证,产品失效率降至50PPM以下。
面向智能制造转型升级需求,建议行业重点攻关三个方向:1) 开发基于数字孪生的虚拟检测技术,实现工艺参数与检测结果的因果建模;2) 建立跨企业的缺陷特征共享平台,依托区块链技术保障数据安全;3) 推动微米级CT检测装备国产化,突破高端连接器检测设备进口依赖现状。通过技术创新与标准共建,端子检测技术将持续赋能高可靠电子制造生态体系建设。
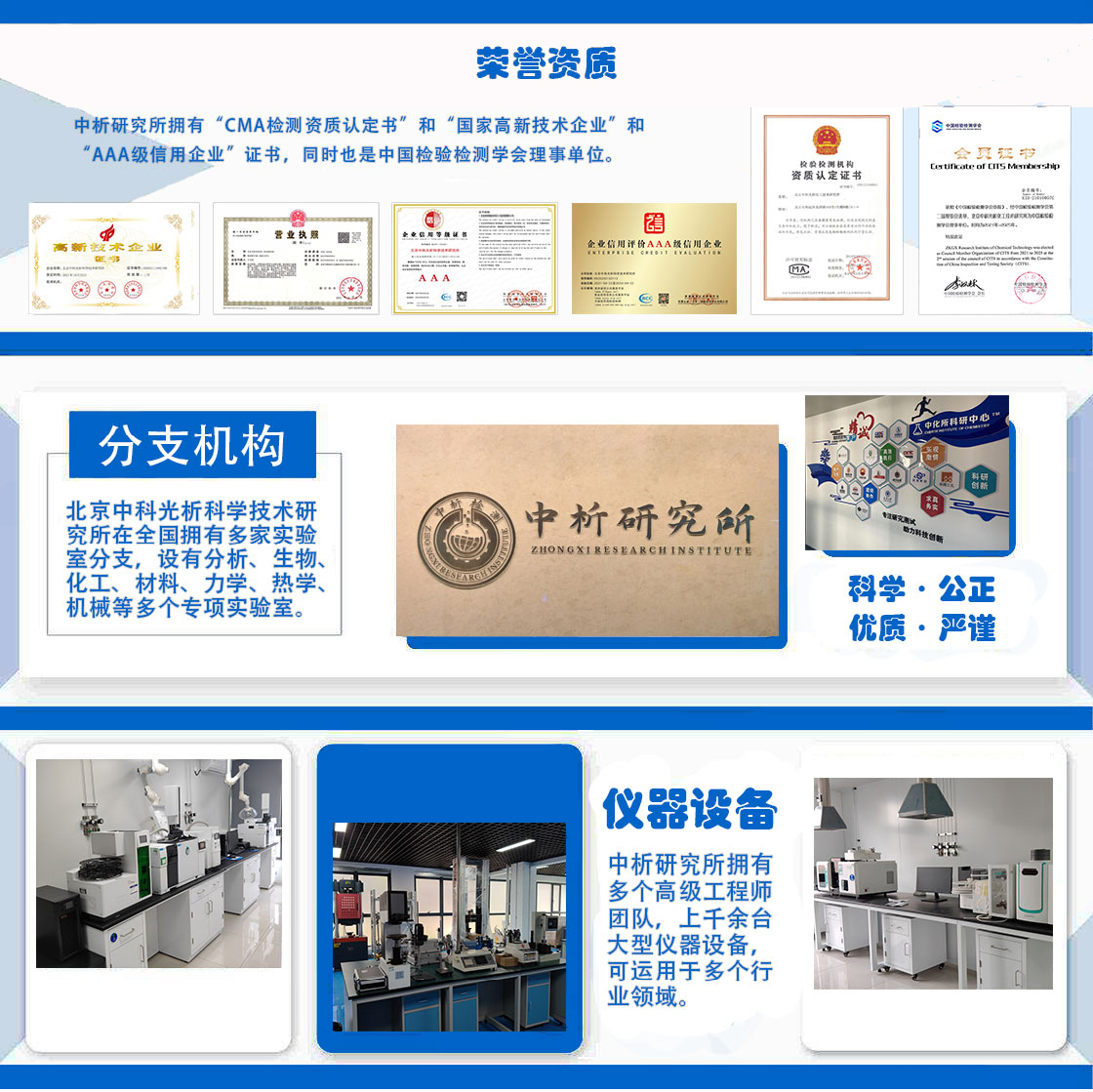
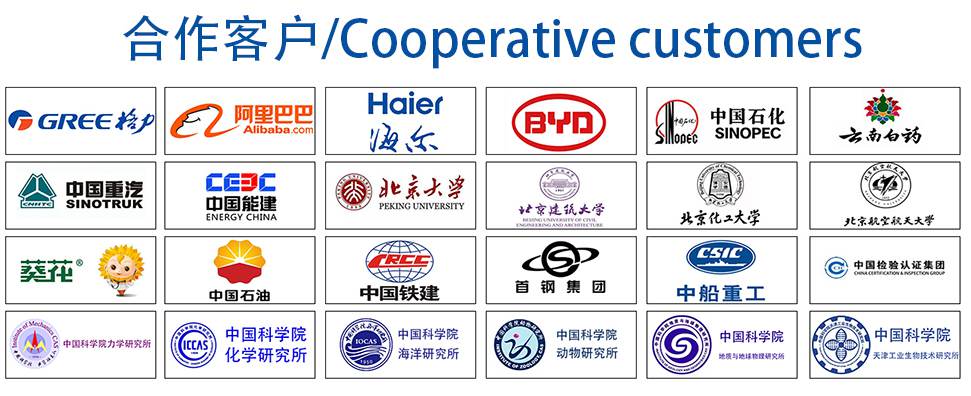