机床梯形螺纹丝杠、螺母检测的重要性
梯形螺纹丝杠和螺母作为机床传动系统的核心部件,其精度和可靠性直接影响设备的定位精度、运动平稳性及使用寿命。在高速、重载或高精度加工场景中,丝杠与螺母的配合间隙、牙型误差、表面磨损等问题可能导致传动失效、振动加剧甚至设备停机。因此,建立科学的检测体系对生产过程质量控制、设备维护及故障预防具有重要意义。本文针对梯形螺纹丝杠和螺母的关键检测项目展开分析,涵盖尺寸精度、形位公差、表面质量及综合性能等多维度指标。
检测项目分类与技术要求
1. 尺寸精度检测
包括螺距误差(GB/T 5796.4)、中径公差(±0.01mm级)、牙顶/牙底宽度、螺纹大径和小径的测量。使用三坐标测量仪或专用螺纹千分尺进行多点采样,确保全行程范围内累积误差不超过允许值,重点关注有效螺纹段的均匀性。
2. 形位公差检测
需检测丝杠的直线度(≤0.02mm/m)、螺纹中径圆柱度(≤IT6级)以及螺母与安装面的同轴度(≤φ0.015mm)。采用激光干涉仪或千分表配合V型块完成动态检测,对长行程丝杠还需分段评估弯曲变形量。
3. 表面质量与硬度检测
表面粗糙度要求Ra≤0.8μm(精磨级),通过轮廓仪或比对样块验证。利用磁粉探伤或涡流检测排查裂纹、折叠等缺陷,同时使用洛氏硬度计(HRC58-62)检测热处理层深度及均匀性,确保耐磨性和抗疲劳强度。
4. 配合性能试验
组装状态下测试轴向间隙(≤0.03mm)和径向跳动量,通过预紧力调整消除异常间隙。动态测试中需监控空载启动力矩(≤额定值20%)及温升曲线,配合接触斑点检查(着色法)评估啮合面积是否达到85%以上。
5. 材料与金相分析
对合金钢材料(如GCr15、40Cr)进行光谱成分分析,检测碳化物分布、晶粒度等级(≥8级)及淬硬层深度(1.5-3mm)。金相显微镜下观察是否存在过热组织、脱碳层等异常现象,保障材料力学性能达标。
检测方法与设备选型
常规检测采用螺纹综合测量仪、投影仪等离线设备,高精度场景推荐搭配激光干涉仪和在线监测系统。新型智能检测方案通过AI图像识别技术实现牙型轮廓的快速比对,结合大数据分析预测磨损趋势。检测周期应根据工况设定,重载设备建议每500小时进行一次精度复检。
系统化的梯形螺纹传动副检测不仅是质量控制的关键环节,更是预防性维护的重要手段。通过标准化检测流程、选择适配的检测设备并建立全生命周期数据档案,可显著提升机床传动系统的稳定性和加工精度,为高端装备制造提供可靠保障。
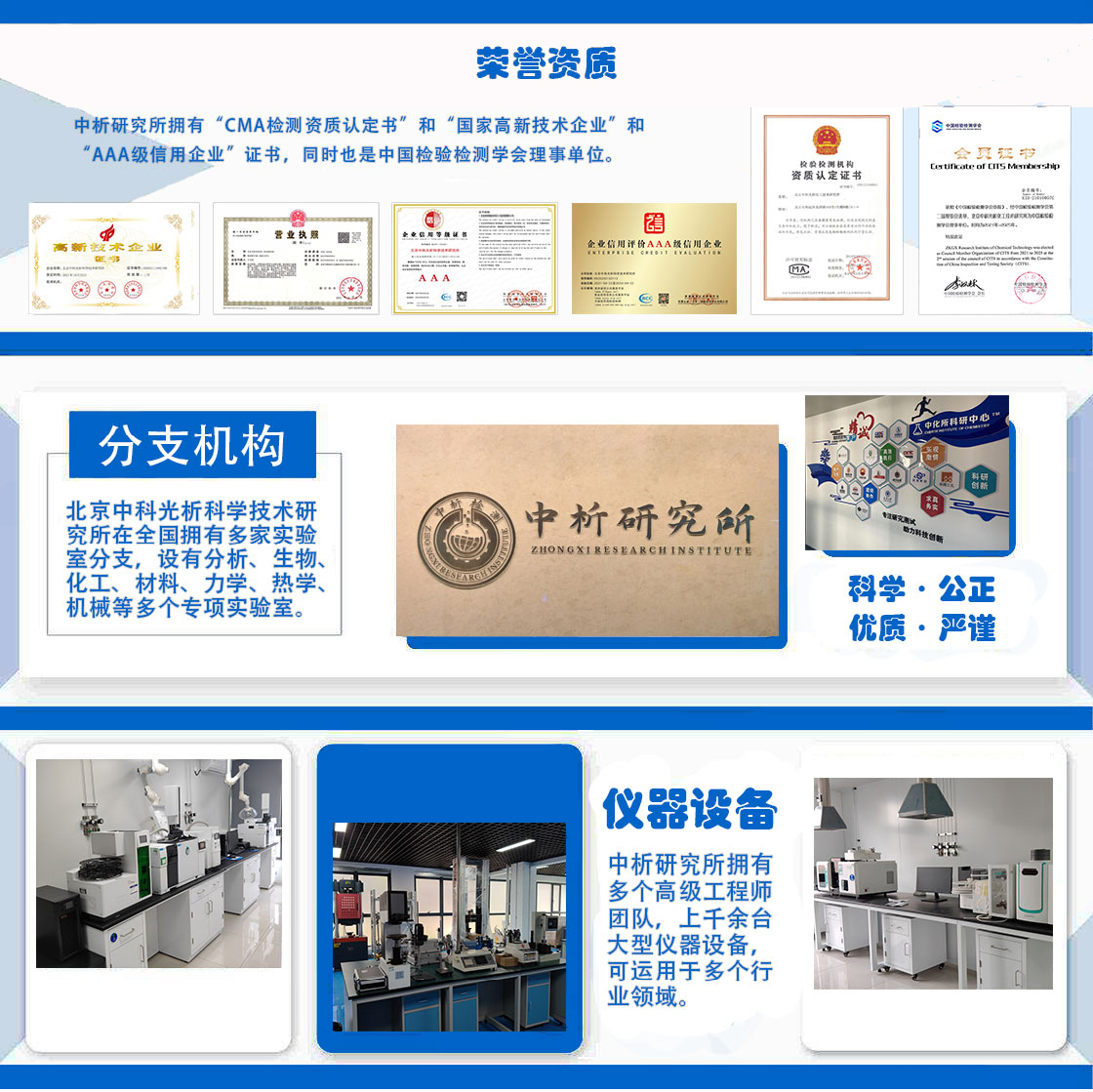
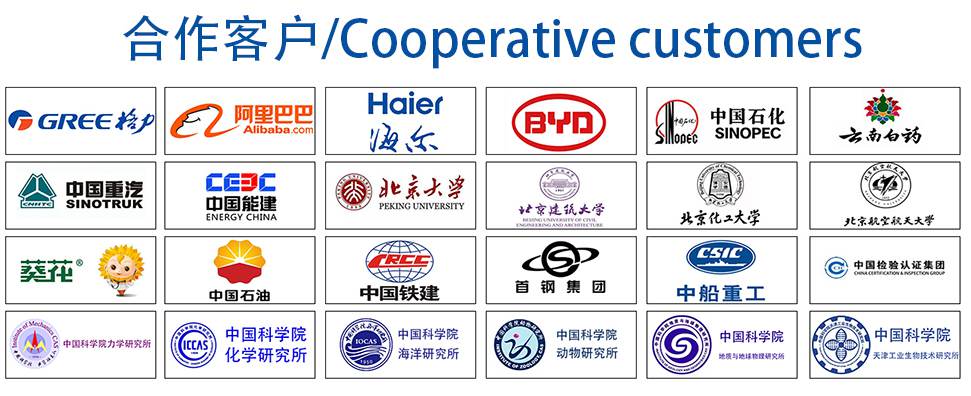