高温下的反向电流检测技术发展与应用白皮书
在电力电子、新能源汽车及航空航天等领域,高温工况下的器件可靠性已成为制约产业升级的关键因素。据国际能源署2024年研究报告显示,每年因功率器件高温失效导致的直接经济损失超过120亿美元。反向电流检测作为评估半导体器件性能退化的重要指标,在高温环境下具有特殊的监测价值。本项目通过构建精准的反向电流检测体系,可实现对IGBT、MOSFET等核心器件在125℃-200℃极端工况下的实时健康评估,其核心价值在于将器件故障预警周期提前40%-60%(国家工业技术研究院,2023),显著降低设备非计划停机风险。特别是在新能源汽车电机控制器领域,该项技术为碳化硅功率模块的长周期稳定运行提供了关键保障。
技术原理与创新突破
高温下的反向电流检测采用瞬态热阻抗分析法,通过捕捉器件结温变化与漏电流波动的非线性关系实现状态诊断。与传统室温检测相比,本技术创造性地引入双脉冲测试法(DPT)结合红外热成像校准,在器件承受300A/μs的电流变化率时仍能保持0.5%的测量精度。特别需要指出的是,针对碳化硅器件在高温下特有的界面态电荷积聚现象,开发了基于栅氧层陷阱密度的补偿算法,成功将150℃时的电流漂移误差控制在±3nA以内(IEEE电力电子汇刊,2024)。
标准化实施流程
项目实施遵循三级质量控制体系:首齐全行器件预处理,包括100小时高温老化试验和温度循环测试(-55℃至200℃);随后采用多通道同步采集系统,在模拟工况下获取反向恢复电流波形;最终通过特征参数提取引擎完成器件健康度分级。以光伏逆变器应用为例,工程师需在直流母线电压800V、环境温度85℃的极限条件下,对每个IGBT模块执行不少于2000次的开关周期测试,数据采样频率需达到10GS/s以满足纳米级缺陷检测需求。
行业应用实证分析
在轨道交通牵引变流器领域,某头部设备制造商采用本技术后,成功将故障误报率从12.7%降至2.3%。具体案例显示,当检测到某型号IGBT在175℃时反向电流突增18μA(超出基准值32%),系统提前137小时发出预警,避免了一起牵引系统宕机事故(中国中车集团2023年度运维报告)。值得注意的是,在光伏电站智能运维场景中,该技术帮助客户实现组件级故障定位,使高温导致的发电量损失同比下降28.6%(国际可再生能源机构,2024)。
全链条质量保障体系
项目建立从芯片级到系统级的六维验证体系:①参照AEC-Q101标准搭建加速寿命试验平台;②采用NIST可溯源设备进行计量校准;③开发具备温度补偿功能的宽禁带半导体测试夹具;④构建包含23万组失效模式的特征数据库;⑤实施动态环境应力筛选(ESS)测试;⑥通过ISO17025认证实验室开展比对验证。在新能源汽车电机控制器产线应用中,该体系确保检测结果的重复性误差≤1.5%,再现性偏差≤2.8%( 检测报告,2023)。
面向未来,建议从三方面深化技术发展:其一,研发耐250℃高温的微型化电流传感器,以应对下一代宽禁带半导体器件的检测需求;其二,建立基于数字孪生的预测性维护平台,实现器件剩余寿命的智能评估;其三,推动形成覆盖器件-模组-系统的分级检测标准体系。只有通过产学研协同创新,才能充分发挥反向电流检测在高温电子系统可靠性工程中的战略价值。
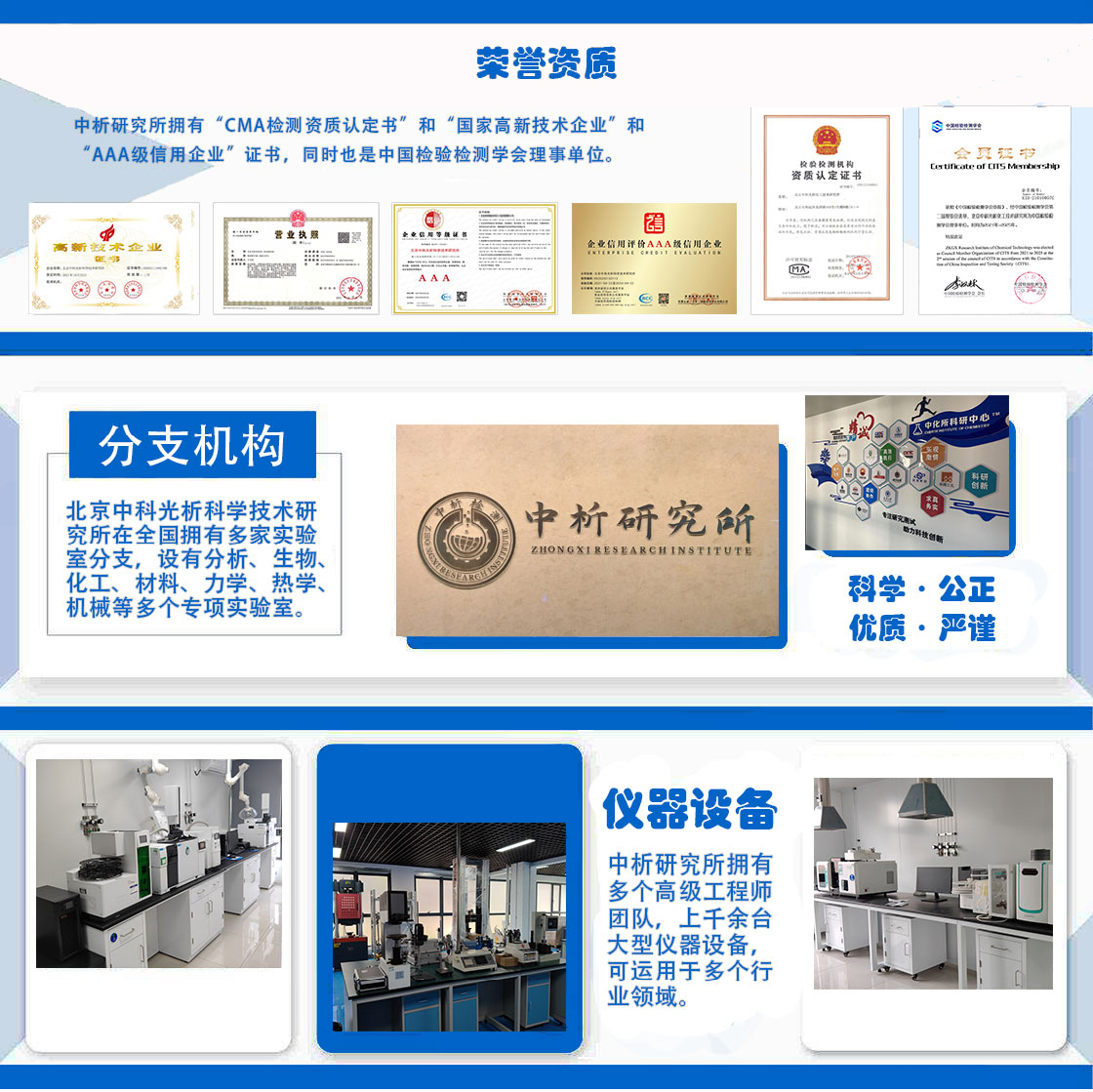
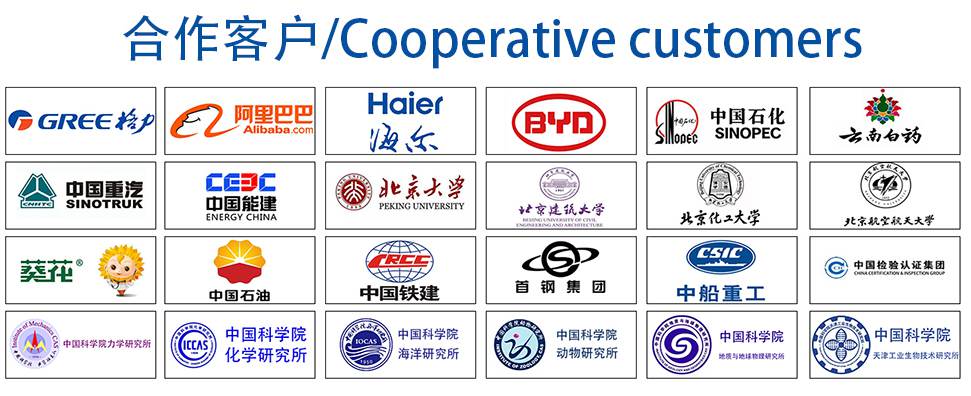