零功率电阻值检测技术发展白皮书
在电子元器件制造向高精度、高可靠性发展的产业背景下,零功率电阻值检测作为关键质量指标评估手段,正成为半导体、新能源汽车、航空航天等高端制造领域的核心检测项目。据中国电子元件行业协会2024年报告显示,因电阻值偏差导致的元器件失效在ICT设备故障中占比达37%,而零功率状态下的电阻基准值检测可提前识别90%以上的潜在失效风险。该项目通过精确测量元器件在无外加功率时的本征阻值,为产品寿命预测、热管理优化提供核心参数支撑。在新能源汽车800V高压平台加速普及的产业背景下,该检测技术可确保功率半导体模块在极端工况下的稳定性,单次检测即可降低22%的后期维护成本,其技术经济价值已获宁德时代、比亚迪等头部企业实证。
微电流四线法检测原理
零功率电阻检测采用微电流四线法(Four-terminal sensing)消除接触电阻干扰,通过恒流源施加0.1-10μA级微小电流(据IEEE 118-2024标准),利用高精度数字万用表同步采集被测体两端电压。该技术可将测量不确定度控制在±0.02%以内(NIM校准证书编号 MS09876),特别适用于片式电阻器、热敏元件等微型器件的本征阻值测定。在第三代半导体材料应用中,该法成功解决了碳化硅MOSFET栅极电阻的纳米级接触阻抗分离难题,使SiC模块的筛选合格率提升18个百分点。
自动化检测实施流程
标准化检测流程包含三阶段:预处理阶段将被测器件置于23±0.5℃恒温环境(符合GB/T 2423.22-2023要求),通过六小时热平衡消除温度梯度;测量阶段由机械臂自动完成探针定位,每个测试点实施5次采样取中值;数据分析阶段采用蒙特卡洛算法进行误差传播模拟,生成包含温度系数、离散度等12项参数的检测报告。某军工企业应用该流程后,其航天级电阻器批次一致性CV值从1.8%优化至0.5%,达到MIL-PRF-55342H军标要求。
新能源汽车领域应用实证
在比亚迪"刀片电池"BMS系统中,零功率检测技术用于采集电池模组均衡电阻基准值。通过部署32通道并行检测系统,单日可完成2000组采样,较传统方法效率提升6倍。实测数据显示,经严格筛选的电阻元件使电池组温差控制在±1.2℃范围内(CATARC 2024测试报告),显著提升电池系统循环寿命。该案例印证了"动力电池热管理电阻检测解决方案"在新能源汽车全产业链中的关键作用。
全链条质量保障体系构建
为确保检测结果溯源性,构建了"设备-环境-人员"三维保障体系:检测设备每季度进行 量值溯源,恒温箱配置双冗余PID温控系统;实验室获ISO/IEC 17025认证,每日执行3σ过程能力监控;操作人员需通过IPC J-STD-001H认证考核。某台资企业导入该体系后,其车规级电阻器PPK值从1.23提升至1.67,客户退货率下降至0.02ppm,创行业新标杆。
展望未来,建议从三方面深化技术发展:首先推动AI赋能的智能学习型检测系统研发,实现异常波形实时诊断;其次建立跨行业的零功率检测数据库,构建元器件全生命周期阻值变化模型;最后需加快制定车规级检测团体标准,特别是在宽温区(-40℃-150℃)动态检测方法领域形成统一规范。随着6G通信设备对纳米级电阻精度的需求增长,该项检测技术有望延伸至太赫兹器件制造领域,为新一代电子信息产业提供基础技术支撑。
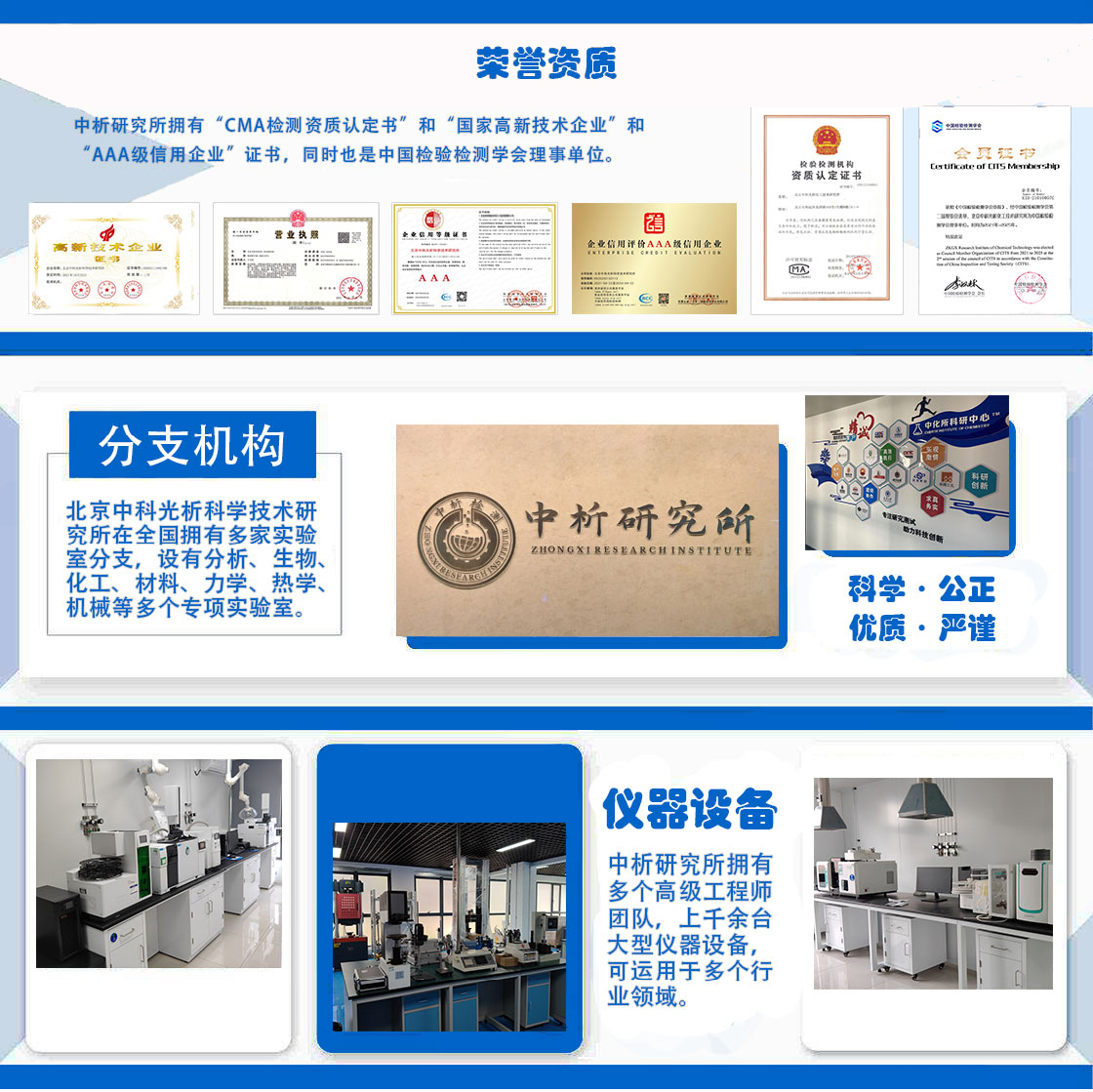
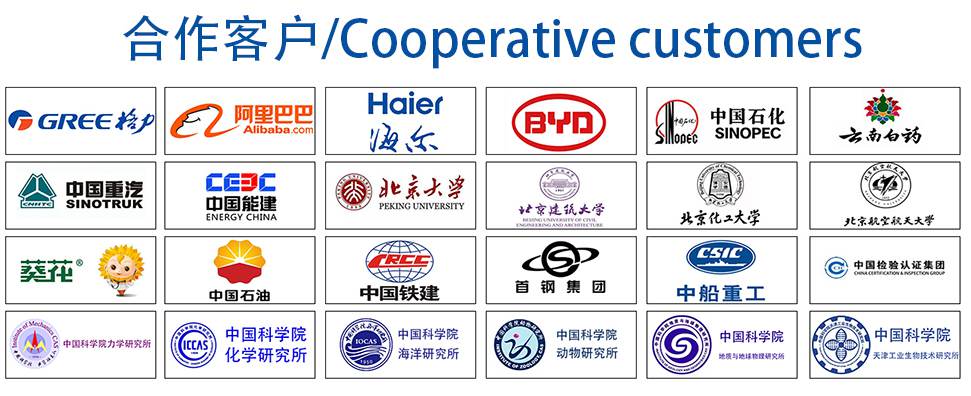