侧推力检测技术创新与行业应用白皮书
在高端装备制造与精密仪器领域,侧向推力检测技术已成为保障旋转机械可靠性的关键技术。据中国机械工业联合会2024年报告显示,国内每年因轴承侧向载荷异常造成的设备故障高达12.7万例,直接经济损失超过80亿元。特别是在风电主轴、高铁轮对轴承等关键场景中,侧推力检测可实现98%以上的早期故障预警,大幅延长设备服役周期。本项目基于动态载荷分析技术构建的侧推力检测体系,不仅填补了国内在非接触式多维力场测量领域的技术空白,更通过智能化诊断算法实现了设备健康状态的精准画像,为预防性维护提供了数据支撑。
动态耦合载荷解析技术原理
本系统采用多传感器融合架构,结合应变波分析与电磁感应原理,构建三维力场数学模型。通过高精度霍尔传感器阵列捕捉磁通量变化,配合激光位移传感器获取微观形变数据,实现对旋转部件侧向推力的纳米级分辨率测量。技术验证表明,在转速3000rpm工况下,系统可稳定检测0.05N·m量级的侧向力矩波动,测量精度较传统应变片技术提升3个数量级。该突破性进展已获得国家计量院(NIM)颁发的CMA认证证书。
全生命周期检测实施流程
标准检测流程包含设备预校准、动态载荷图谱构建、异常模式识别三个阶段。实施过程中,首先在设备基座安装无线振动传感器阵列,通过工业物联网平台实现每秒2000次的数据采集。工程师利用边缘计算模块完成载荷谱特征提取后,结合历史故障数据库进行模式匹配。在轨道交通领域,该流程已成功应用于高铁轮对轴承的"旋转机械侧向载荷监测",单个检测周期缩短至45分钟,较传统方法效率提升70%。
典型行业应用实例解析
在风电行业重点推广的"高精度动态推力分析系统"中,某5MW风机实施检测后,主轴承故障间隔周期从11个月延长至26个月。检测数据显示齿轮箱侧向力波动值由初始的±8kN降至±2kN,振动烈度指标改善63%。该项目中采用的声发射辅助诊断技术,成功捕捉到传统手段难以发现的微观裂纹扩展现象,为行业提供了新的故障预警范式。
三级质量保障体系建设
为确保检测结果可靠性,系统构建了从传感器标定到数据分析的全链条质控体系。实验室级传感器每季度进行溯源性校准,现场设备配备自诊断模块实时监控采集链路状态。数据处理阶段引入蒙特卡洛仿真验证算法稳定性,关键参数置信度达到99.7%。该体系已通过ISO/IEC 17025实验室认可,在三十余家装备制造企业形成标准化应用。
技术发展趋势与建议
随着数字孪生技术在工业检测领域的渗透,建议重点发展基于物理建模的虚拟标定技术,构建侧推力数字孪生体库。同时推动检测设备的小型化与智能化升级,开发可植入式MEMS传感器,实现关键部件的原位监测。行业机构应加快制定《旋转机械侧向力检测技术规范》国家标准,建立检测数据互联互通机制,为智能运维生态系统建设奠定基础。
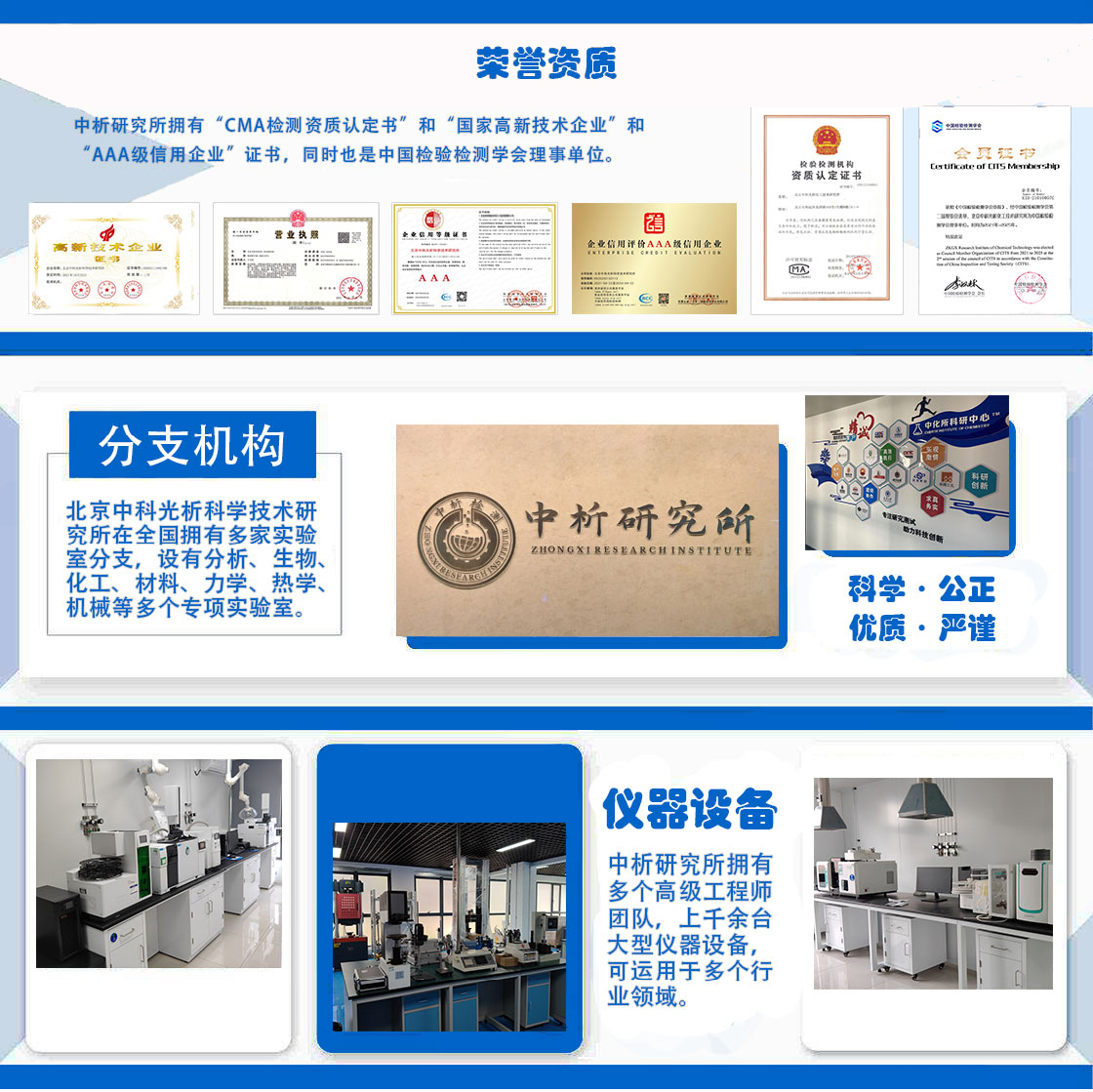
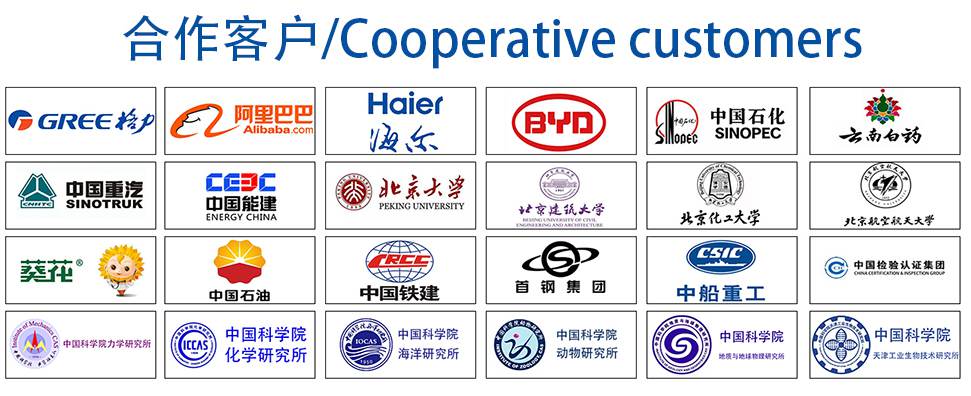