冲撞检测:核心检测项目与技术解析
引言
一、核心检测项目分类
1. 自动驾驶领域
2. 机器人及自动化领域
3. 工业制造领域
4. 其他领域
- 体育科学:运动员碰撞监测(如头盔传感器评估冲击力)。
- 虚拟现实:触觉反馈碰撞模拟,提升沉浸感。
二、关键技术方法
-
- 光学传感器:摄像头、红外用于物体识别。
- 雷达/LiDAR:精确测距与3D建模。
- 惯性传感器:加速度计、陀螺仪捕捉动态变化。
-
- 机器学习模型:CNN、Transformer处理图像与序列数据。
- 物理引擎仿真:如Unity、Gazebo预演碰撞场景。
- 实时计算框架:ROS(机器人操作系统)、边缘计算设备。
-
- 结合不同传感器优势(如摄像头高分辨率+雷达抗干扰),通过卡尔曼滤波或深度学习融合数据,提升鲁棒性。
三、应用场景与价值
- 汽车AEB系统:减少超70%的追尾事故(据IIHS统计)。
- 协作机器人(Cobot):工厂内人机协同效率提升30%。
- 智能仓储:AGV避障系统降低货损率90%。
四、挑战与未来趋势
- 技术瓶颈:复杂场景下的多目标跟踪、低光照/恶劣天气检测精度。
- 未来方向:
- AI驱动的预测模型:提前3-5秒预判碰撞风险。
- 5G/V2X协同:车与路侧单元实时通信,扩展检测范围。
- 生物仿生传感器:模拟生物感知机制(如昆虫复眼结构)。
上一篇:低压调速电气传动系统(环境)检测下一篇:限定短路试验检测
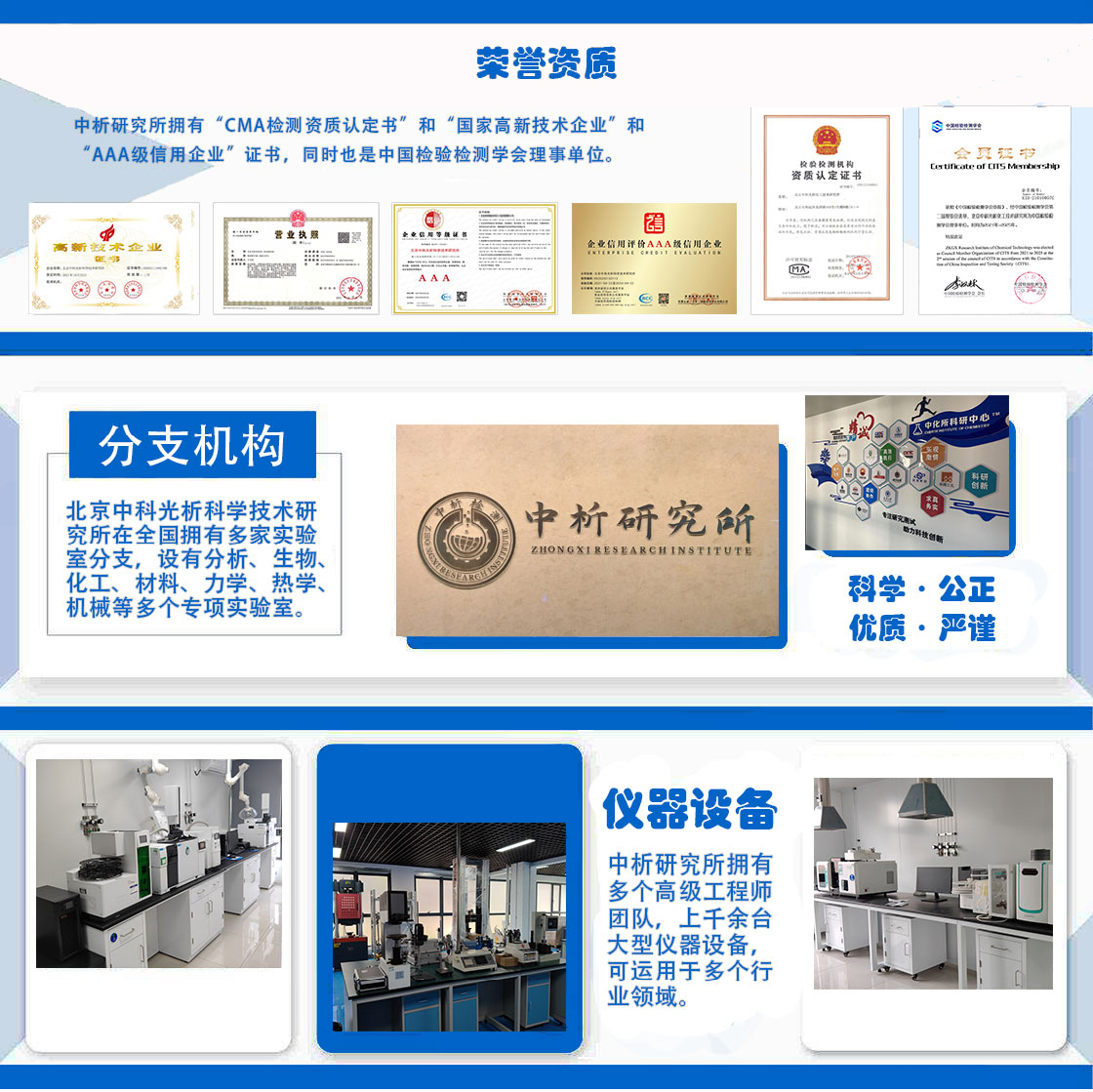
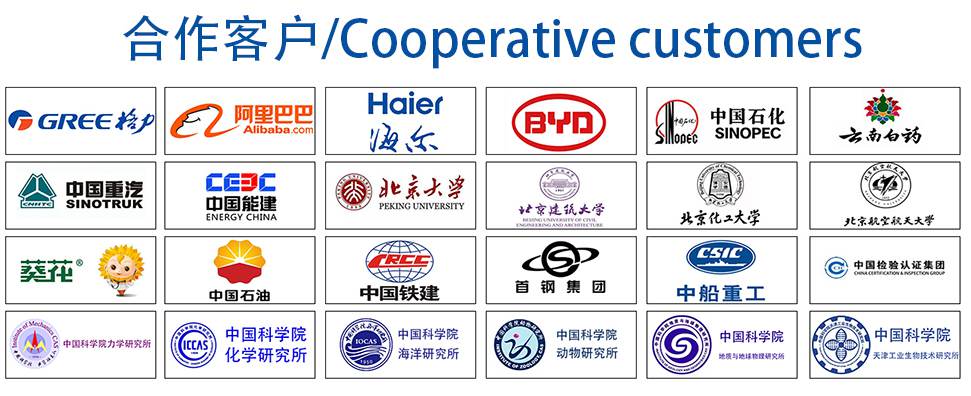
材料实验室
热门检测
276
233
208
217
215
221
230
223
234
233
220
219
222
219
214
210
227
212
224
218
推荐检测
联系电话
400-635-0567