万向节滚针轴承检测的重要性
万向节滚针轴承是汽车传动系统的核心部件之一,广泛应用于驱动轴、转向系统及差速器中,承担着传递扭矩和适应角度变化的重要功能。其性能直接影响车辆的动力传输效率、行驶平稳性及使用寿命。然而,由于工作环境复杂(如高速旋转、高负载、频繁冲击等),滚针轴承容易出现磨损、疲劳、腐蚀等问题。因此,通过科学的检测手段对万向节滚针轴承进行系统化的质量评估,是保障其可靠性和安全性的关键环节。
万向节滚针轴承检测的主要项目
1. 外观缺陷检测
通过目视检查或显微镜观察轴承表面是否存在划痕、锈蚀、裂纹、变形等缺陷。重点检查滚针排列是否均匀、保持架是否完整,以及密封件的贴合度。若发现表面损伤,可能因安装不当或材料疲劳引发失效风险。
2. 尺寸精度检测
使用千分尺、投影仪或三坐标测量仪,对轴承内径、外径、宽度、滚针直径及圆度进行精密测量。参数需符合ISO 492或GB/T 307.1标准,公差范围通常要求±0.005mm以内。尺寸超差会导致配合松动或卡滞,影响传动精度。
3. 材料性能测试
通过硬度计(如洛氏硬度HRC)检测轴承的基体硬度,要求达到58-62 HRC以确保耐磨性。同时,采用金相分析仪观察材料内部组织是否均匀,是否存在夹杂物或脱碳层。对于高频淬火处理的部件,需验证硬化层深度(一般≥0.8mm)。
4. 动态性能试验
在模拟工况下通过耐久性试验台测试轴承的旋转扭矩、温升及振动值。标准测试条件通常为额定载荷下连续运行500小时以上,温升不应超过40℃,振动幅度需低于0.15mm/s。异常噪音或温度突变可能预示润滑失效或滚针偏磨。
5. 润滑系统评估
检查轴承内部的油脂填充量及分布均匀性,采用红外光谱仪分析润滑油是否氧化变质。润滑脂的滴点应高于工作温度20℃以上,基础油黏度需满足NLGI 2级标准。劣化油脂会加速磨损,缩短轴承寿命。
6. 表面处理与防腐能力
利用盐雾试验箱验证轴承的耐腐蚀性能(如48小时中性盐雾试验后无红锈)。对于磷化或镀层处理的表面,需通过划格法测试附着力,并检测涂层厚度(通常要求5-15μm)。防腐性能不足会导致轴承在潮湿环境中快速失效。
7. 清洁度检测
通过颗粒计数仪测定轴承内部残留的金属碎屑、粉尘等污染物含量,每平方厘米面积内粒径>50μm的颗粒数应少于20个。杂质残留会加剧摩擦,甚至引发卡死故障。
检测流程与标准化管理
完善的检测流程应遵循“初检→性能测试→复检”的闭环模式,结合SPC(统计过程控制)方法进行数据监控。企业需建立符合IATF 16949或VDA 6.3标准的检测体系,配备自动检测设备(如智能影像测量仪)提升效率。检测报告需涵盖所有关键参数,并实现全程可追溯,为质量改进提供数据支撑。
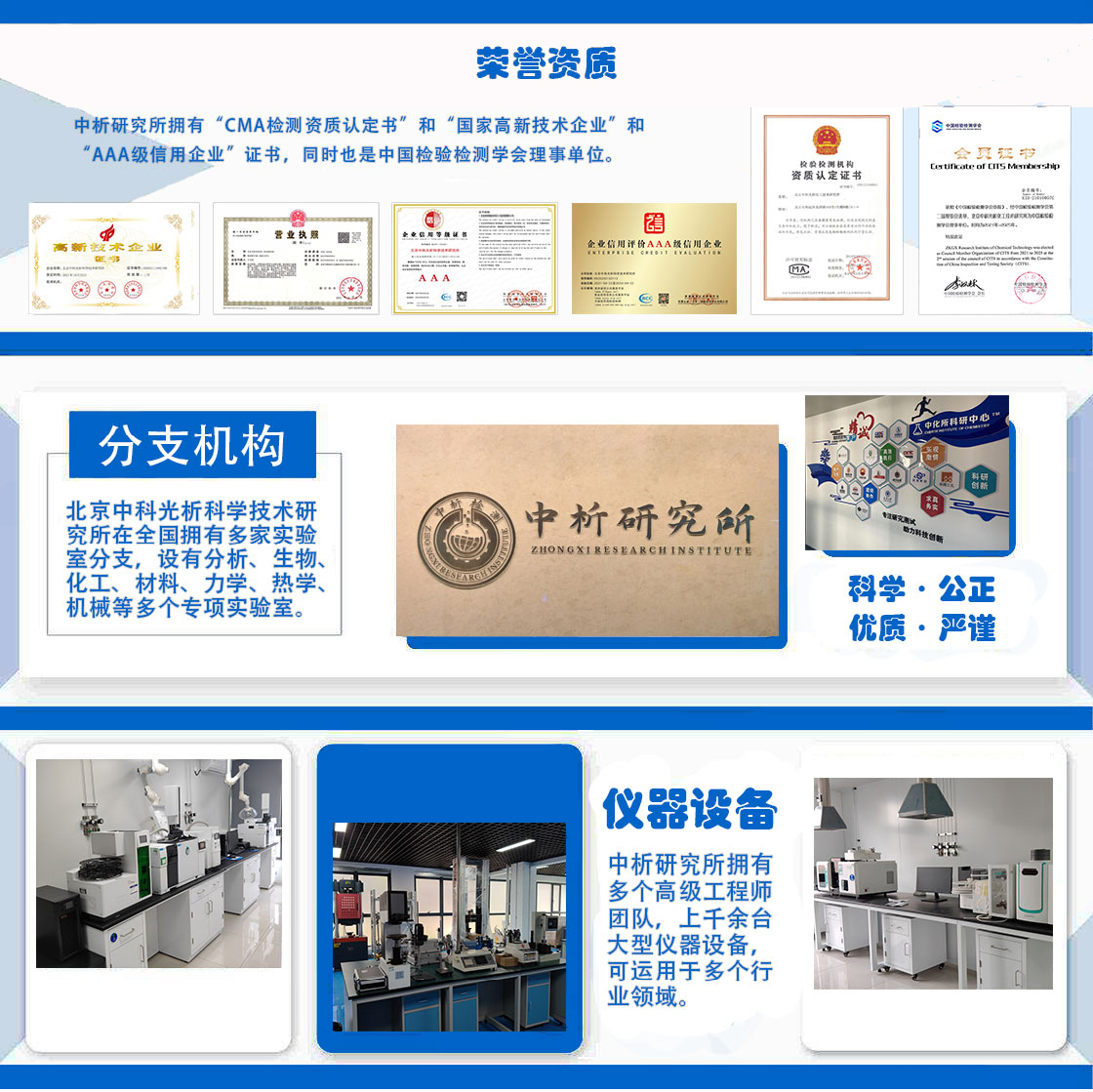
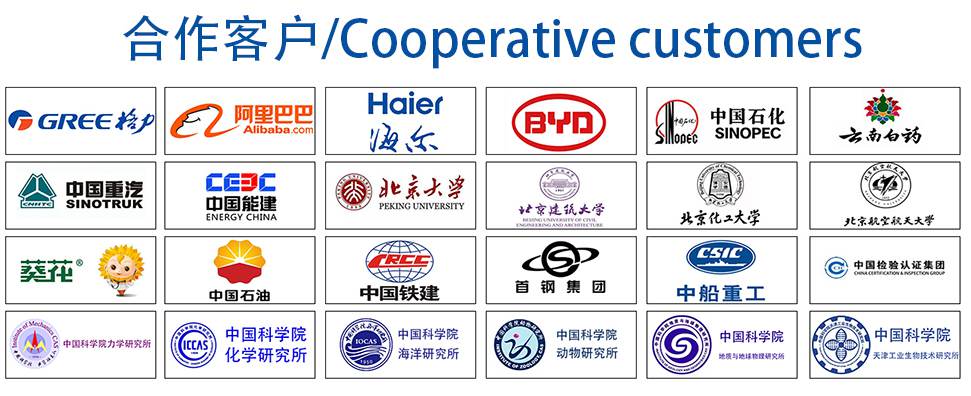