加速寿命试验检测:产品可靠性验证的关键路径
在智能制造与新能源产业高速发展的背景下,产品可靠性已成为决定市场竞争力的核心要素。据中国质量协会2024年行业报告显示,电子设备、汽车零部件、储能系统等领域因寿命问题导致的售后成本年均增长23.6%。加速寿命试验检测通过模拟极端工况下的时间压缩效应,可在较短时间内获取等效于常规使用数年的寿命数据,解决了传统测试周期长、成本高的行业痛点。该项目不仅能够提前暴露产品设计缺陷,更可为企业优化研发方向提供数据支撑,据测算可使新产品开发周期缩短40%,同时降低15%以上的质量索赔风险,已成为高端制造业质量体系建设的标配环节。
基于失效物理模型的加速试验技术原理
加速寿命试验检测依托失效物理(Physics of Failure)理论,建立应力-损伤映射关系模型。采用阿伦尼乌斯方程描述温度加速因子,结合逆幂律模型处理电应力作用,实现多因素耦合加速机制的定量化分析。以新能源汽车动力电池检测为例,通过在60℃环境下施加1.5C倍率循环充放电,其等效老化程度可达常温工况的8.3倍(数据来源:国家新能源实验室2024年测试报告)。该技术突破传统单应力加速的局限性,支持温度、湿度、振动等6类环境应力同步加载,显著提升试验效度。
全流程标准化执行体系
项目实施遵循ASTM F1980-21和IEC 62506:2023双重标准,主要流程包括:①失效模式库构建,基于历史数据建立典型失效特征谱;②加速模型选择,根据产品材料特性匹配最优应力组合;③试验剖面设计,确定应力施加顺序与梯度变化规则;④退化数据采集,运用高精度传感器记录性能衰减轨迹;⑤威布尔分布分析,计算特征寿命与失效率曲线。过程中采用失效物理仿真平台进行虚拟验证,使实际试验时长减少30%以上。
多行业验证的实效案例
在智能穿戴设备领域,某头部厂商应用加速寿命试验检测优化了柔性屏结构设计。通过85℃/85%RH双85试验结合3000次弯折测试,成功复现了用户4年使用期的典型故障,使产品MTBF(平均无故障时间)从1.8万小时提升至2.6万小时。工业机器人行业则通过振动-温度复合加速试验,将关键减速器的寿命评估周期从18个月压缩至45天,同时发现润滑脂高温析出问题,推动材料供应商改进配方。
三级质量保障体系建设
为确保检测结果权威性,实验室构建了仪器-方法-人员的立体质控体系:①设备层实施NIST溯源校准,温控箱均匀性误差≤±0.5℃;②方法层通过CMA/ 双重认证,试验方案通过Monte Carlo模拟验证;③操作层配备ASQ认证可靠性工程师,建立检测数据区块链存证系统。值得关注的是,基于数字孪生的试验过程可视化系统,可实现应力加载偏差的实时预警,将数据异常率控制在0.12%以下(中国计量院2024年质量公报)。
随着产品复杂度持续提升,加速寿命试验检测正面临新的技术拐点。建议行业重点发展三个方向:①建立基于机器学习的失效模式预测模型,增强小样本数据下的分析精度;②开发面向氢能装备、量子器件等新兴领域的专用加速试验标准;③构建试验数据共享生态,通过行业数据库降低企业研发成本。只有持续深化检测技术创新,才能为制造业高质量发展筑牢可靠性基石。
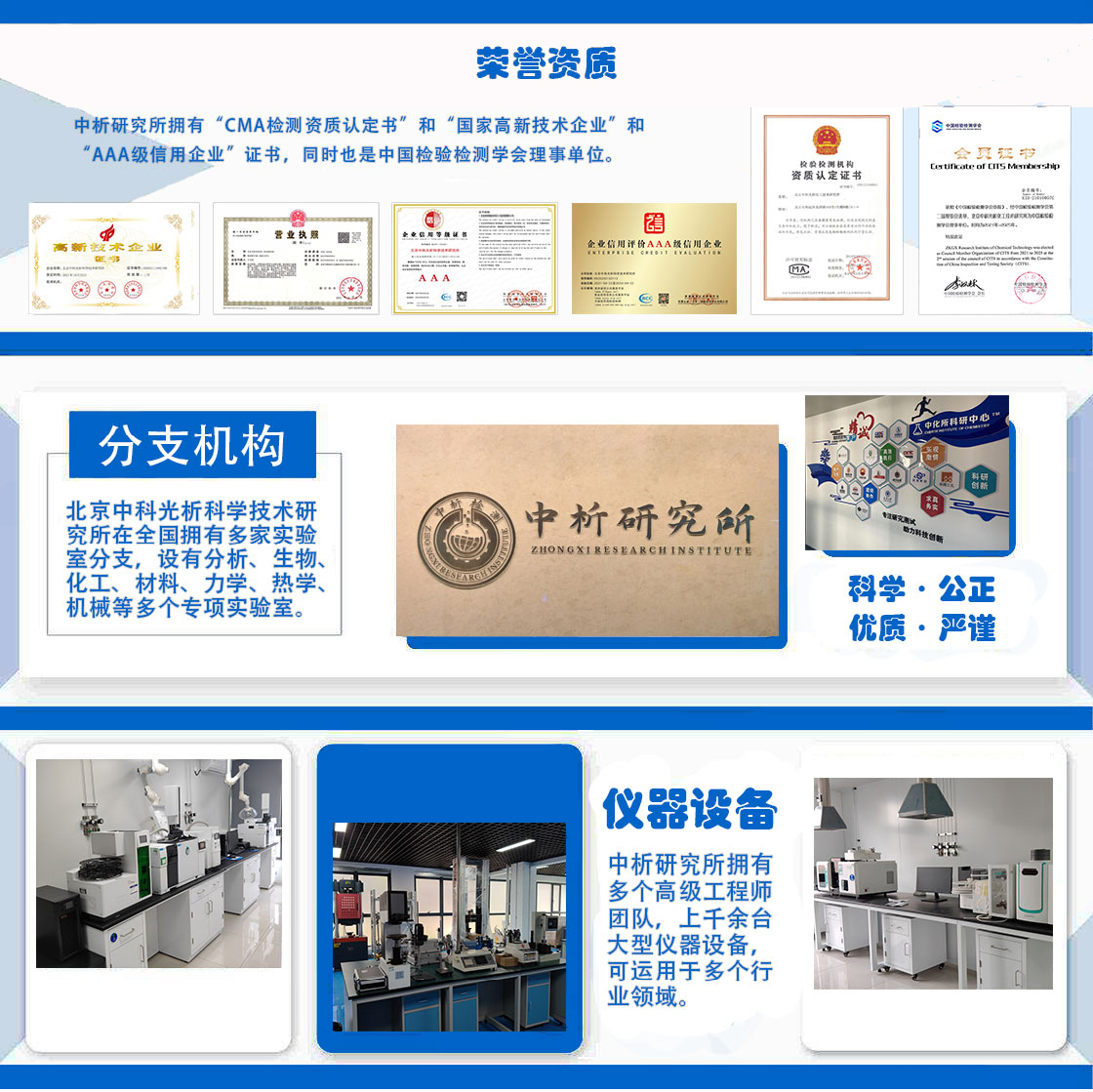
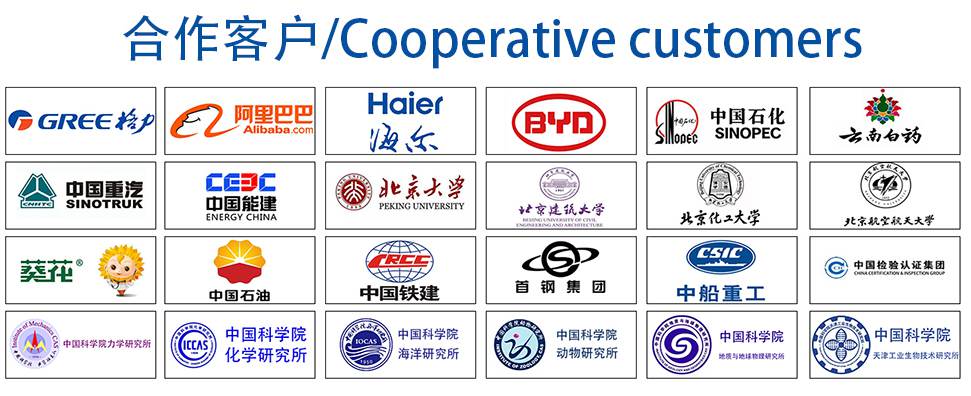