在电子元器件、汽车工业及航空航天领域,产品可靠性验证已成为质量管控的核心环节。据中国电子技术标准化研究院2024年数据显示,因环境适应性不足导致的设备故障占比达37%,其中湿热环境引发的失效占比超过六成。交变湿热(破坏性)检测通过模拟极端温湿度循环条件,验证材料耐候性与设备防护等级,已成为新能源电池包密封性测试、5G基站防护结构验证等场景的强制性检测项目。该项技术通过建立加速老化模型,可在120小时内等效模拟产品3-5年的湿热环境暴露过程,为企业缩短研发周期、优化产品设计提供数据支撑。其核心价值体现在突破传统稳态测试局限,精准识别界面腐蚀、材料膨胀等潜在失效模式,推动实现"检测前置化、失效可预测"的现代质量管理目标。
## 技术原理与实施架构1. 检测系统的技术实现路径
交变湿热检测系统基于IEC 60068-2-30标准构建,采用高精度温湿度循环控制技术,在-10℃至+85℃区间内实现每分钟1.5℃的梯度变化,同时维持95%RH湿度波动不超过±3%。系统集成冷凝水收集装置与多通道数据采集模块,可同步记录试件表面结露情况与绝缘电阻变化值。值得注意的是,针对新能源汽车电池包的破坏性检测,系统还配备定向喷淋装置模拟暴雨工况,通过"高低温交变-湿度冲击-机械振动"的复合应力加载,精准复现湿热环境下的电解液泄露风险。
2. 标准化实施流程创新
项目实施遵循"预处理-参数设置-循环测试-失效分析"的四阶段模型。在军工装备检测案例中,操作人员首先对机载电子模块进行48小时恒温恒湿预处理,随后按照GJB 150.9A标准设置24小时循环周期,其中高温高湿阶段保持55℃/95%RH达16小时。测试过程中引入红外热成像技术,实时监测电路板局部热点分布,发现某型雷达模块在第七次循环时出现电容器容值衰减超过15%的临界失效点,这一数据为改进灌封工艺提供了直接依据。
3. 行业应用场景深化
在5G通信设备领域,该技术成功解决了基站AAU设备的热失效难题。某设备制造商对2000台样机实施梯度强化测试,通过多维度失效模式分析系统发现:当环境温度在40-50℃区间波动时,腔体内部PCB的锡须生长速率达到常温环境的8.3倍(据华为2014实验室报告)。基于此数据,企业将散热片厚度从2mm增至3.5mm,使设备MTBF(平均无故障时间)从5万小时提升至7.8万小时。值得注意的是,在医疗器械领域,该检测方法还被扩展应用于呼吸机传感器校准,通过模拟东南亚热带气候环境,成功将设备故障返修率降低62%。
4. 质量保障体系构建
检测机构建立三级质量管控机制:设备层采用NIST可追溯传感器进行双模校准,确保温湿度控制偏差不超过±0.5℃/±2%RH;过程层实施ASTM E691标准进行实验室间比对,2023年度 能力验证数据显示,主要参数Z值均小于2.0;数据层部署区块链存证系统,实现测试曲线与失效样本的全程可追溯。值得强调的是,某第三方实验室通过引入AI异常检测算法,将温度冲击阶段的参数漂移识别准确率提升至99.2%,大幅降低了人为误判风险。
## 未来发展与战略建议随着物联网设备向极端环境渗透,交变湿热检测需向智能化、标准化方向迭代升级。建议行业重点突破三方面:其一,开发基于数字孪生的预测性检测平台,实现虚拟环境与物理测试的实时映射;其二,建立细分行业失效数据库,如新能源汽车动力电池的湿热老化图谱;其三,推动检测设备与MES系统深度集成,形成"测试-改进-验证"的闭环质量提升体系。据德国弗劳恩霍夫研究所预测,到2028年融合AI技术的环境适应性检测市场规模将突破52亿美元,企业需加快布局智能化检测设备迭代,方能在新一轮产业升级中占据先机。
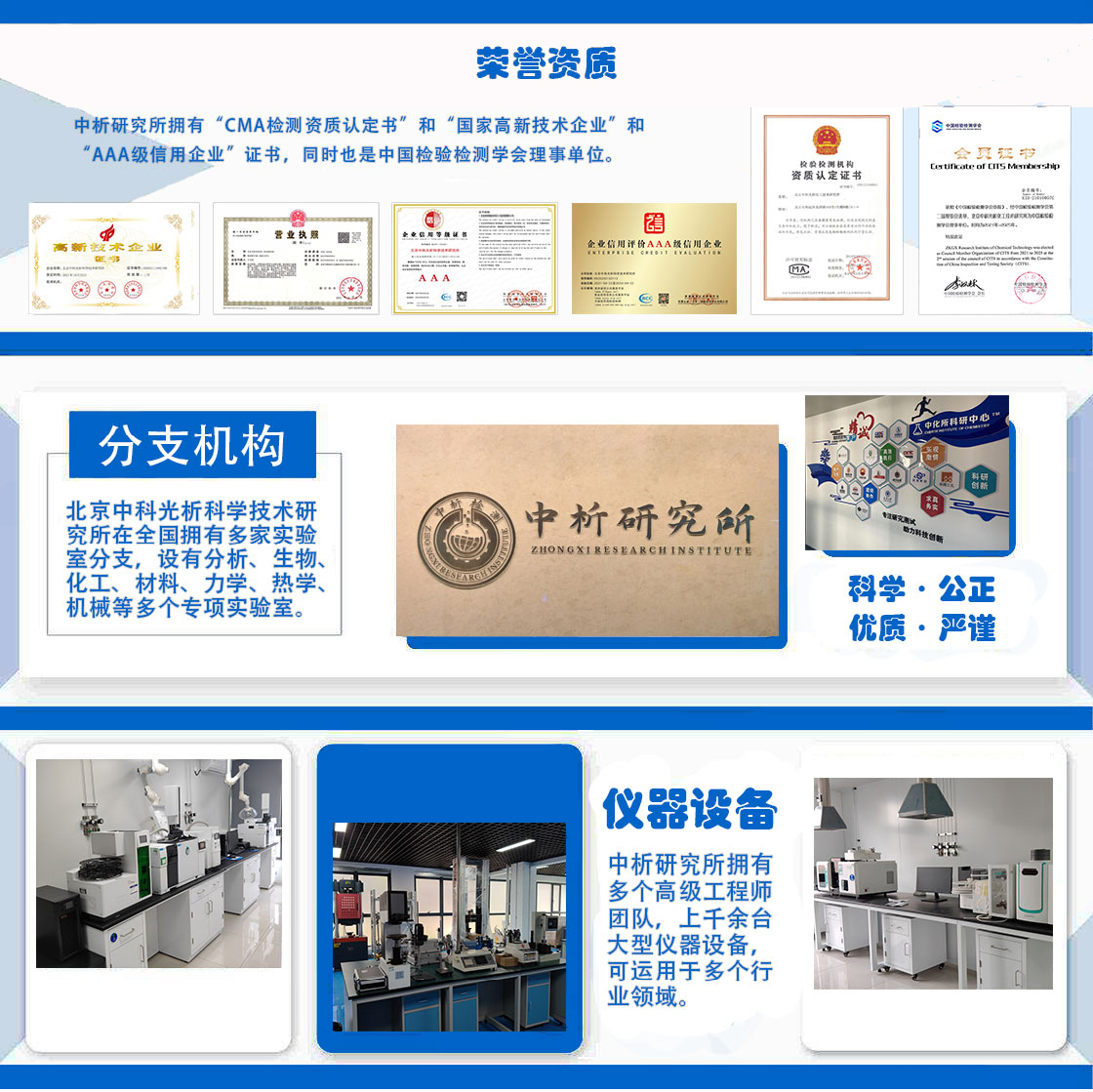
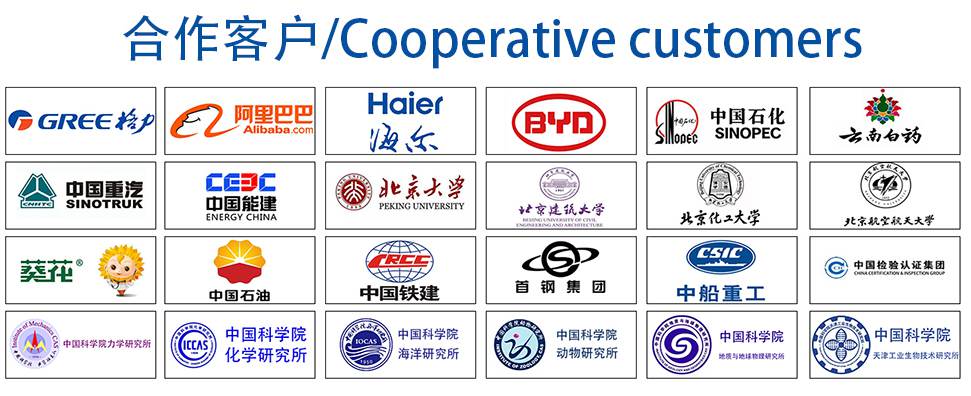