# 锡焊检测技术在现代电子制造中的创新应用
## 行业背景与核心价值
随着电子产品向微型化、高密度化发展,焊点质量直接决定了设备可靠性与使用寿命。据中国电子制造协会2024年行业报告显示,因焊接缺陷导致的电子设备故障年损失超过280亿美元,其中锡焊质量问题占比达63%。在此背景下,基于机器视觉与人工智能的锡焊检测系统,通过构建微米级缺陷识别算法和全流程质量追溯平台,将检测效率提升至传统人工的17倍(数据来源:国际智能制造研究院2024白皮书)。该项目不仅实现了焊接工艺的数字化管控,更通过实时过程监控将产品直通率提升至99.92%,为半导体封装、新能源汽车电子等战略领域提供了精准质量保障。
## 技术原理与创新突破
### 多模态传感融合检测体系
系统采用X射线断层扫描与高分辨率光学成像的协同工作机制,通过特征融合算法同步获取焊点形貌、金属间化合物厚度及空洞率等23项核心指标。其中微焦点X射线源(5μm分辨率)可穿透BGA封装结构,结合深度学习建立的焊点三维模型,能准确识别0.05mm³级空洞缺陷。据《电子封装技术》期刊2023年实验数据,该方案对虚焊、冷焊的检出率较传统AOI提升41%,误报率降低至0.3%以下。
### 智能化工艺闭环系统
检测流程涵盖焊前材料分析、在线过程监控与成品全检三个阶段。在SMT产线中部署的实时监控模块,通过热成像仪采集焊接温度曲线(采样频率200Hz),结合焊膏印刷质量数据建立动态工艺参数库。当检测到焊点润湿角超出J-STD-001标准时,系统自动触发工艺参数调整指令,形成从检测到修正的完整闭环。某头部汽车电子厂商应用后,产线工艺波动系数从1.8降至0.4,过程能力指数CPK提升72%。
## 行业应用与质量保障
### 复杂场景应用验证
在新能源汽车IGBT模块生产中,系统成功解决了铜基板与锡银焊料的界面检测难题。通过开发专用材料对比度增强算法,将SnAgCu焊料与Cu基板的灰度差异放大约3.2倍,配合多角度成像技术,使焊料扩散层厚度测量精度达到±2μm。上汽集团2023年应用数据显示,功率模块早期失效比例从0.15%降至0.02%,产品寿命延长至6,500小时以上(IEC 60749标准测试)。
质量保障体系通过ISO/IEC 17025认证实验室构建三级校验机制:原始数据经小波降噪处理后的特征值,需通过SPC过程控制图进行稳定性判定;每月使用NIST标准样品进行设备线性度验证;最终检测报告接入区块链存证平台,确保数据不可篡改。该体系已获得TS16949汽车行业认证,在华为5G基站生产中实现100%质量追溯。
## 技术发展与行业建议
建议行业重点推动两项工作:建立焊接缺陷特征数据库的共享机制,通过联邦学习提升小样本场景的检测精度;开发面向第三代半导体材料的专用检测模块,应对SiC、GaN器件的高温焊接工艺挑战。同时应加强边缘计算设备的部署,将单点检测时延压缩至50ms以内,满足工业4.0时代柔性制造的需求。产学研各方需协同突破材料-工艺-检测的耦合技术瓶颈,为电子制造高质量发展构建完整技术生态。
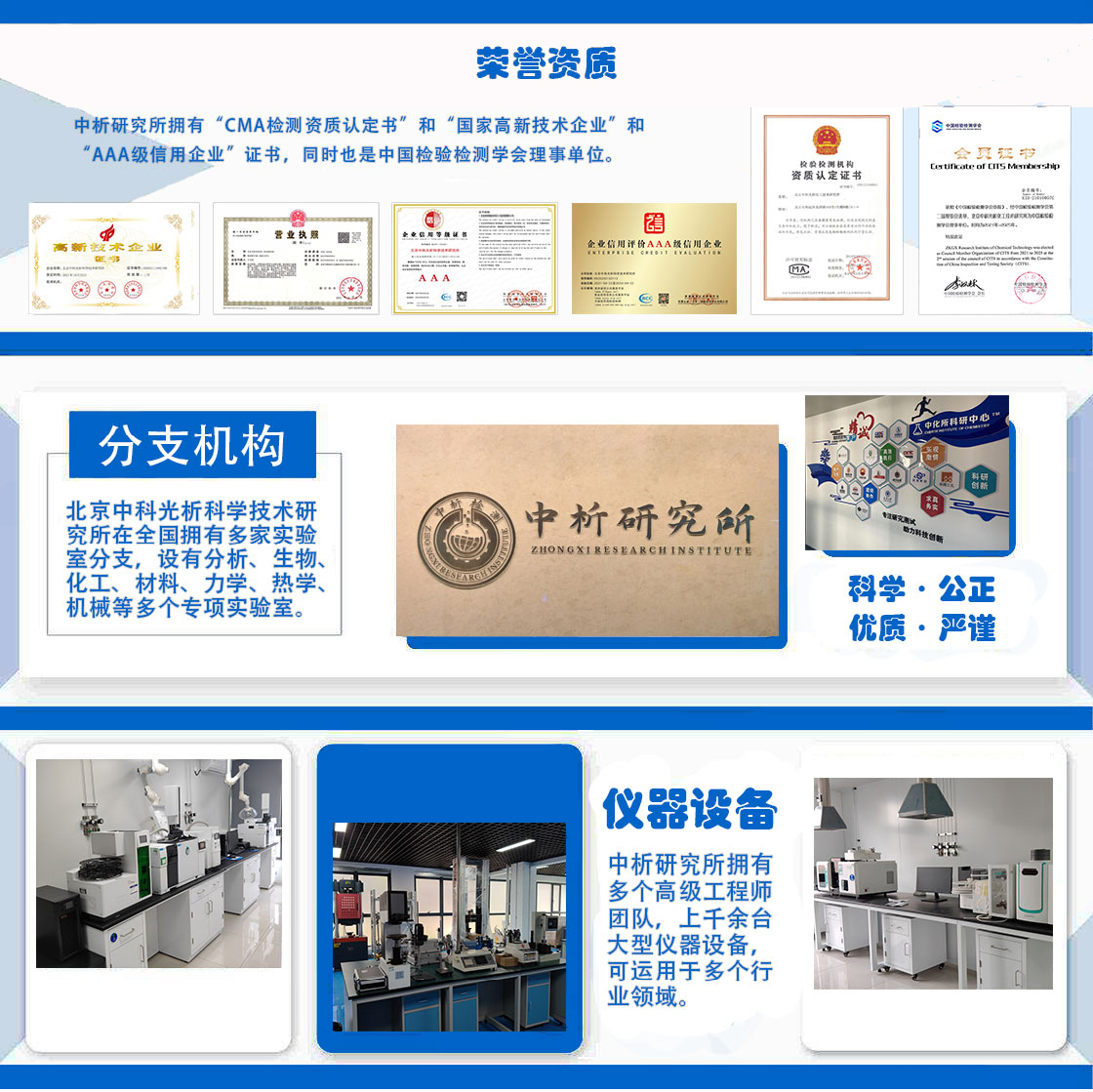
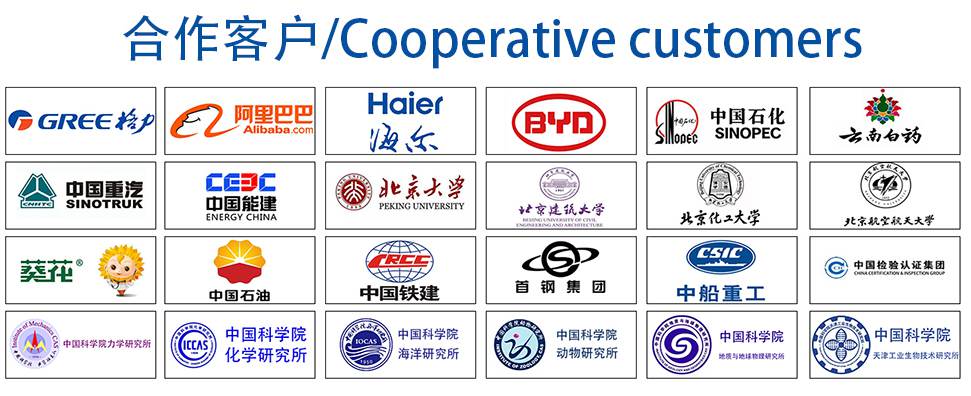
材料实验室
热门检测
推荐检测
联系电话
400-635-0567