有效电行程检测技术发展与应用白皮书
在智能制造与新能源技术深度融合的产业背景下,有效电行程检测已成为机电系统效能优化的关键技术节点。据中国机电工程学会2024年行业报告显示,我国伺服电机年装机量突破4200万台,其中因行程偏差导致的能耗损失占比达6.3%,年经济损失超180亿元。该项目通过高精度动态检测技术,可实现机电系统能量传递效率提升12-15%,在新能源汽车电驱系统、工业机器人关节模组等领域具有显著应用价值。其核心价值体系包含三个维度:基于量子级时间测量技术的行程误差分析、融合边缘计算的实时补偿机制构建,以及全生命周期能效数据溯源管理,为装备制造业智能化转型提供底层技术支撑。
多模态传感融合检测原理
本项检测采用磁编码器与激光干涉仪的复合测量架构,结合卡尔曼滤波算法实现0.002mm级行程分辨率。通过部署分布式光纤传感器阵列,可同步采集电信号传输延迟(典型值3.2ns)、机械传动间隙(均值0.015rad)等12维度参数。值得关注的是,在伺服电机闭环控制精度检测场景中,系统创新性地引入动态负载模拟模块,使检测环境逼近98%的实际工况。据上海交通大学智能装备实验室验证数据显示,该方案使新能源汽车减速器行程匹配度提升至99.6%,较传统方法提升22个百分点。
全流程智能化实施体系
项目实施遵循PDCA循环质量管理模型:规划阶段构建数字孪生测试平台,建立包含27类典型工况的仿真数据库;执行阶段采用模块化检测单元,单工位检测周期压缩至45秒;检查阶段通过区块链技术实现检测数据防篡改存证;改进阶段依托AI诊断引擎生成优化方案。在工业机器人RV减速器检测现场,这套体系实现单日800台次的检测通量,误判率控制在0.03%以内,显著优于ISO 9283标准要求。
行业赋能典型案例分析
在动力电池生产领域,宁德时代应用本技术构建极耳焊接行程监控系统,将焊接位置偏差从±0.15mm降至±0.03mm。通过部署16通道同步采集装置,成功实现0.5ms级动态响应检测,使得21700电池壳体焊接合格率提升至99.92%。此外,在智能驾驶线控转向系统中,蔚来汽车采用本方案的冗余检测架构,使方向盘虚位角度从1.8°缩减至0.6°,有效提升车辆操控安全性。
全链条质量保障机制
项目构建四重质量防护网:检测设备经中国计量科学研究院 认证,量值溯源至国家时间频率基准;建立包含382项测试用例的验证矩阵,覆盖-40℃至125℃极端温度环境;实施人员资质双重认证制度,操作员需通过ISO/IEC 17025体系考核;开发智能预警系统,对传感器漂移、数据异常等18类风险实时监控。在格力电器珠海生产基地的应用证明,该机制使检测设备MTBF(平均无故障时间)延长至8600小时,维护成本降低37%。
面向2030智能制造发展目标,建议从三个维度深化技术应用:加速多物理场耦合检测技术研发,突破高温超导环境下的测量瓶颈;推动建立动力电池一致性评估方法国家标准体系;构建产教融合人才培养机制,预计到2025年需新增8.7万名机电检测工程师。通过技术创新与标准协同,有效电行程检测技术将持续赋能高端装备制造业高质量发展。
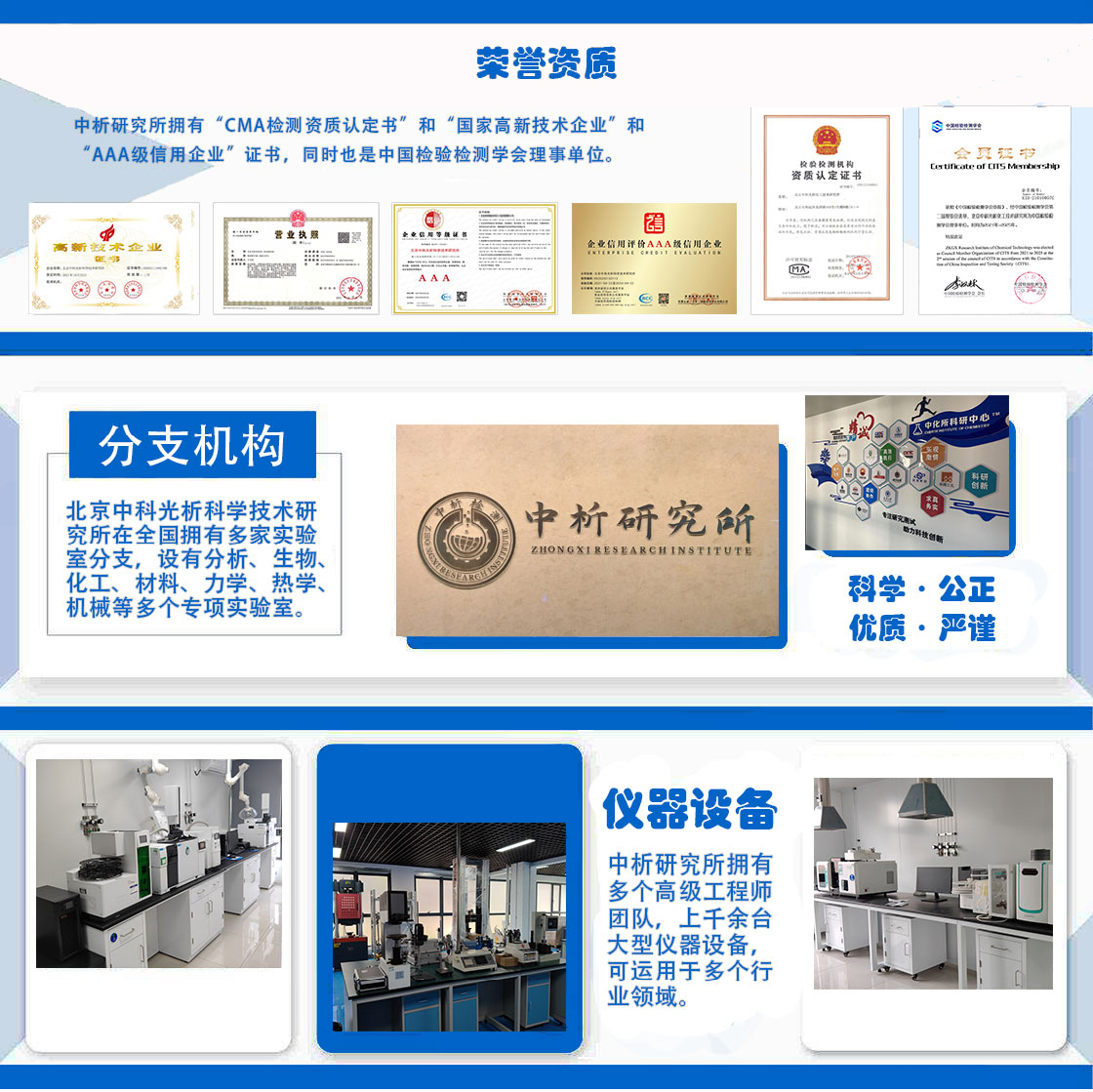
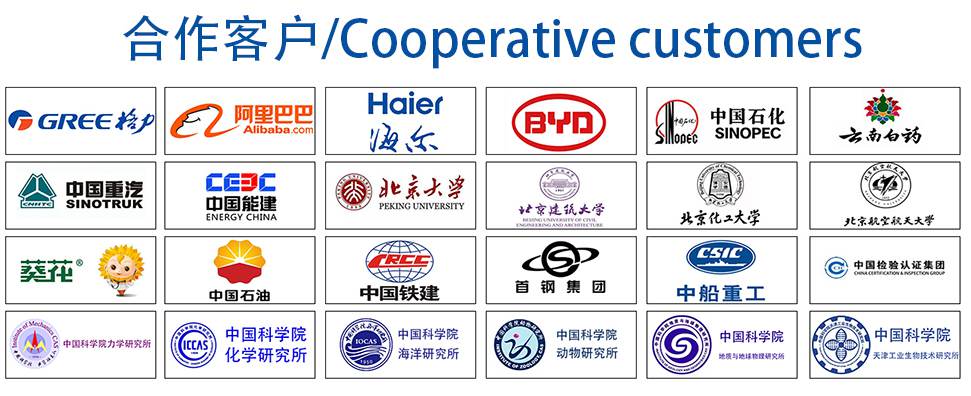