石油机械配件检测:守护能源装备安全的生命线
在石油勘探开发与炼化生产的全产业链中,机械配件犹如精密仪器的细胞单元,其性能质量直接决定着钻采设备、输油管道、炼化装置的运行安全与使用寿命。随着深海油田、页岩气等复杂工况开采活动的增加,石油机械配件检测已从传统的外观检查发展为涵盖材料性能、动态响应、环境耐受等30余项指标的立体化质量监控体系。行业数据显示,通过全流程检测可将设备故障率降低62%,每年为石油行业避免超过50亿美元的经济损失。
核心检测项目体系
材料性能验证
采用光谱分析仪、金相显微镜等设备对阀体、钻铤、管接头的金属成分进行定量分析,确保材料符合API 6A/17D标准。通过万能试验机开展拉伸、压缩、弯曲试验,检测屈服强度(≥758MPa)、断面收缩率(≥50%)等关键力学指标。运用夏比冲击试验机在-46℃低温环境下评估材料的脆性转变特性。
几何精度检测
使用三坐标测量仪对螺杆泵定子内螺旋曲面进行0.001mm级精度扫描,比对API 11B规定的公差带。采用激光干涉仪检测井口装置平面度,确保法兰密封面平面度≤0.05mm。通过螺纹综合测量机验证油套管接头的锥度、螺距、牙型角等参数,满足API 5CT标准要求。
表面完整性评估
应用工业内窥镜对涡轮钻具流道内部进行360°缺陷扫描,利用磁粉探伤检测曲轴表面0.1mm级细微裂纹。通过白光干涉仪测量柱塞泵缸套表面粗糙度(Ra≤0.4μm),采用涂层测厚仪验证硬质合金镀层厚度(50-200μm)。
动态性能测试
在液压脉冲试验台上对防喷器闸板进行20000次开合循环测试,模拟井下35MPa压力冲击。使用六自由度振动台对海底采油树进行5-200Hz扫频试验,检测共振频率点。通过高速摄像机记录螺杆钻具轴承在1500rpm工况下的动态偏摆量(≤0.08mm)。
环境适应性验证
在H2S分压0.1MPa的腐蚀试验箱中持续暴露720小时,评估节流阀的硫化物应力开裂敏感性。采用盐雾试验机模拟海洋平台环境,检测316L不锈钢件的点蚀深度(≤0.02mm)。通过高温高压釜在175℃、70MPa条件下测试封隔器胶筒的密封保持性能。
智能化检测技术革新
当前行业正加速推进数字射线检测(DR)、相控阵超声检测(PAUT)等齐全技术应用。基于深度学习的视觉检测系统可自动识别92%以上的表面缺陷,检测效率提升400%。通过数字孪生技术构建配件全生命周期数据库,实现质量问题的正向追溯与逆向归因。这些技术创新使得检测漏检率从1.2%降至0.05%,为石油装备安全提供了革命性保障。
在能源安全战略升级的背景下,石油机械配件检测已突破传统质量控制的范畴,发展成为融合材料科学、精密测量、人工智能的交叉学科。只有构建起覆盖设计验证、生产监控、服役评估的全链条检测体系,才能确保每件机械配件都能在极端工况下稳定服役,为能源供应筑牢安全防线。
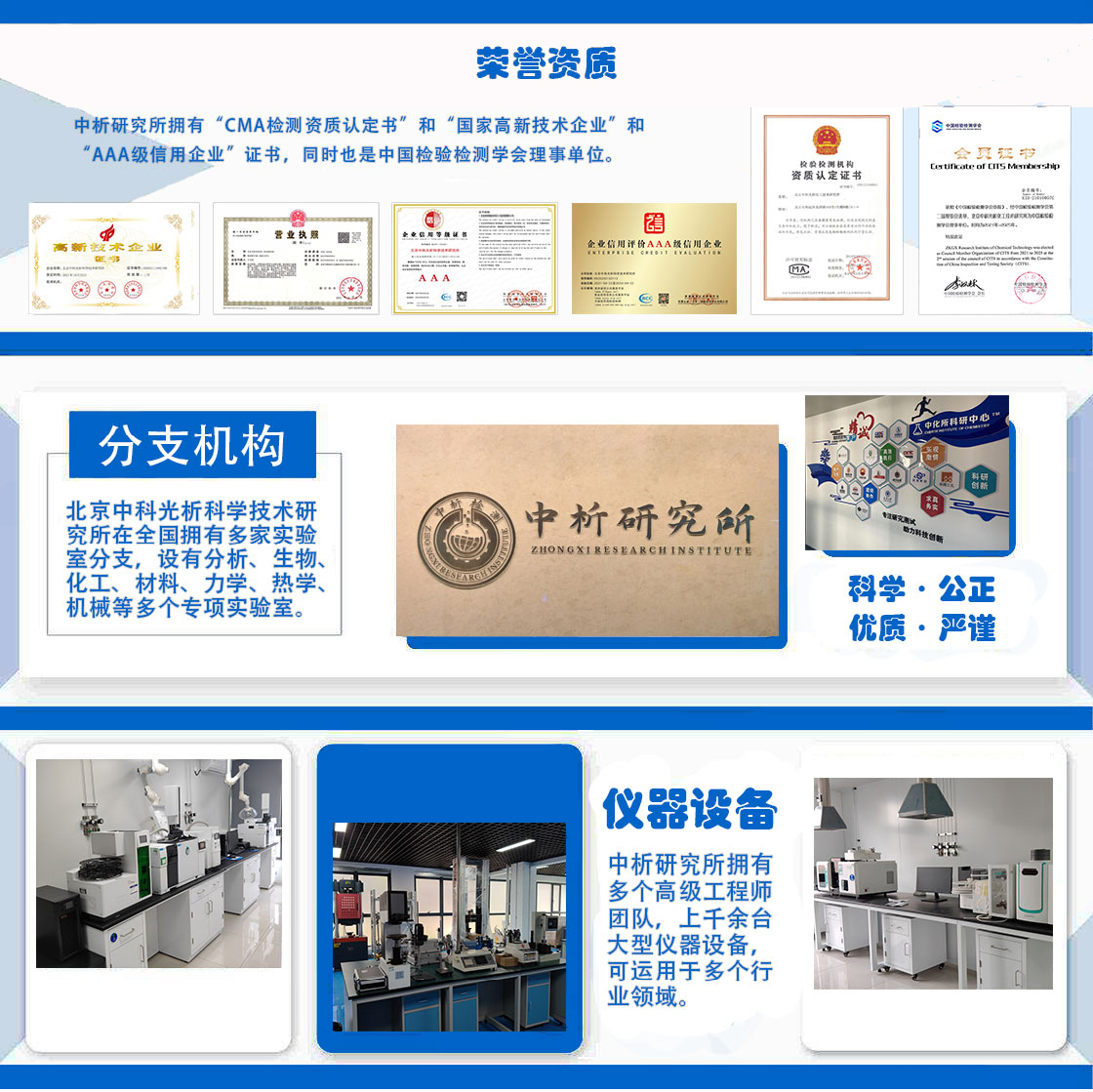
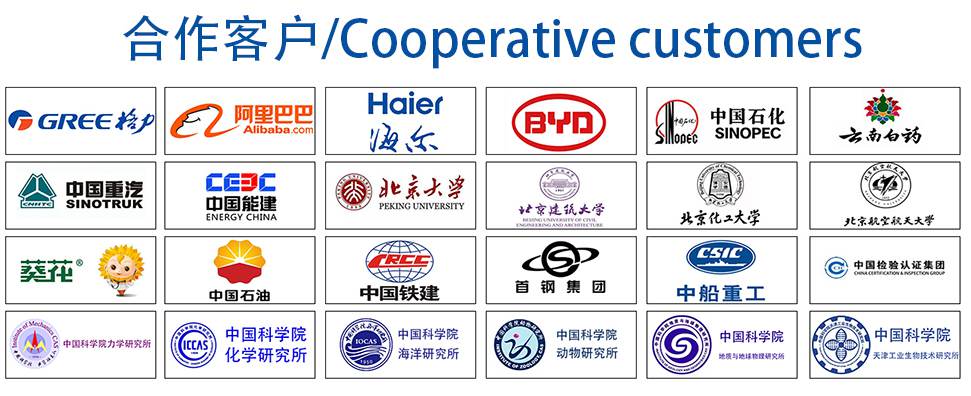