工业产品检测的核心价值与流程概述
工业产品检测是保障制造业高质量发展的重要环节,贯穿于产品研发、生产、流通的全生命周期。作为质量控制的核心手段,它通过系统化的测试与分析,确保产品符合国家标准、行业规范及客户需求。在化竞争背景下,工业检测不仅能够规避因产品缺陷引发的安全事故,更能帮助企业建立市场信任度,提升国际竞争力。现代检测体系已从传统的人工抽样检查发展为多维度、智能化的评估模式,涵盖物理性能、化学特性、环境适应性等20余个关键指标,形成了一套科学严谨的质量验证闭环。
核心检测项目分类解析
1. 材料性能检测
包括金属材料的拉伸强度、硬度测试,非金属材料的耐腐蚀性、热变形温度检测。通过万能试验机、光谱分析仪等设备验证原材料是否符合设计要求,确保产品基础性能达标。
2. 尺寸精度验证
采用三坐标测量仪、激光扫描仪等精密设备进行公差检测,重点控制关键部位的配合精度。对机械零部件而言,0.01mm级的误差可能导致整机装配失效。
3. 表面质量评估
涵盖涂层厚度、粗糙度、色差等指标的检测,使用X射线荧光测厚仪、表面轮廓仪等专业设备。特别是汽车、家电等外观件产品,表面质量直接影响用户体验和市场接受度。
4. 功能可靠性测试
模拟实际使用场景进行耐久性试验,包括电子产品的老化测试、机械设备的疲劳试验。例如新能源汽车电池需通过2000次充放电循环检测,确保使用寿命达到行业标准。
5. 环境适应性检测
在气候箱中进行的温湿度循环测试、盐雾试验、振动冲击测试等,验证产品在极端环境下的性能稳定性。军工、航空航天产品往往需要满足-55℃至125℃的宽温域工作需求。
智能化检测技术革新
随着工业4.0的发展,机器视觉检测系统已实现对微小缺陷的毫秒级识别,AI算法可自动分析检测数据并生成质量改进方案。某汽车零部件企业引入智能检测线后,产品不良率从0.8%降至0.15%,年节约质量成本超1200万元。
检测认证体系构建
完善的检测体系需要取得CMA、 等实验室认证资质,同时对接ISO9001、IEC等国际标准。第三方检测机构出具的ASTM、EN检测报告,已成为产品进入欧美市场的必备通行证。
工业产品检测正在从被动质量控制转向主动质量设计,通过检测大数据反哺产品研发,推动制造业向高端化、智能化方向转型升级。未来,虚拟仿真检测与实体检测的深度融合,将进一步提升工业品质量管控效率。
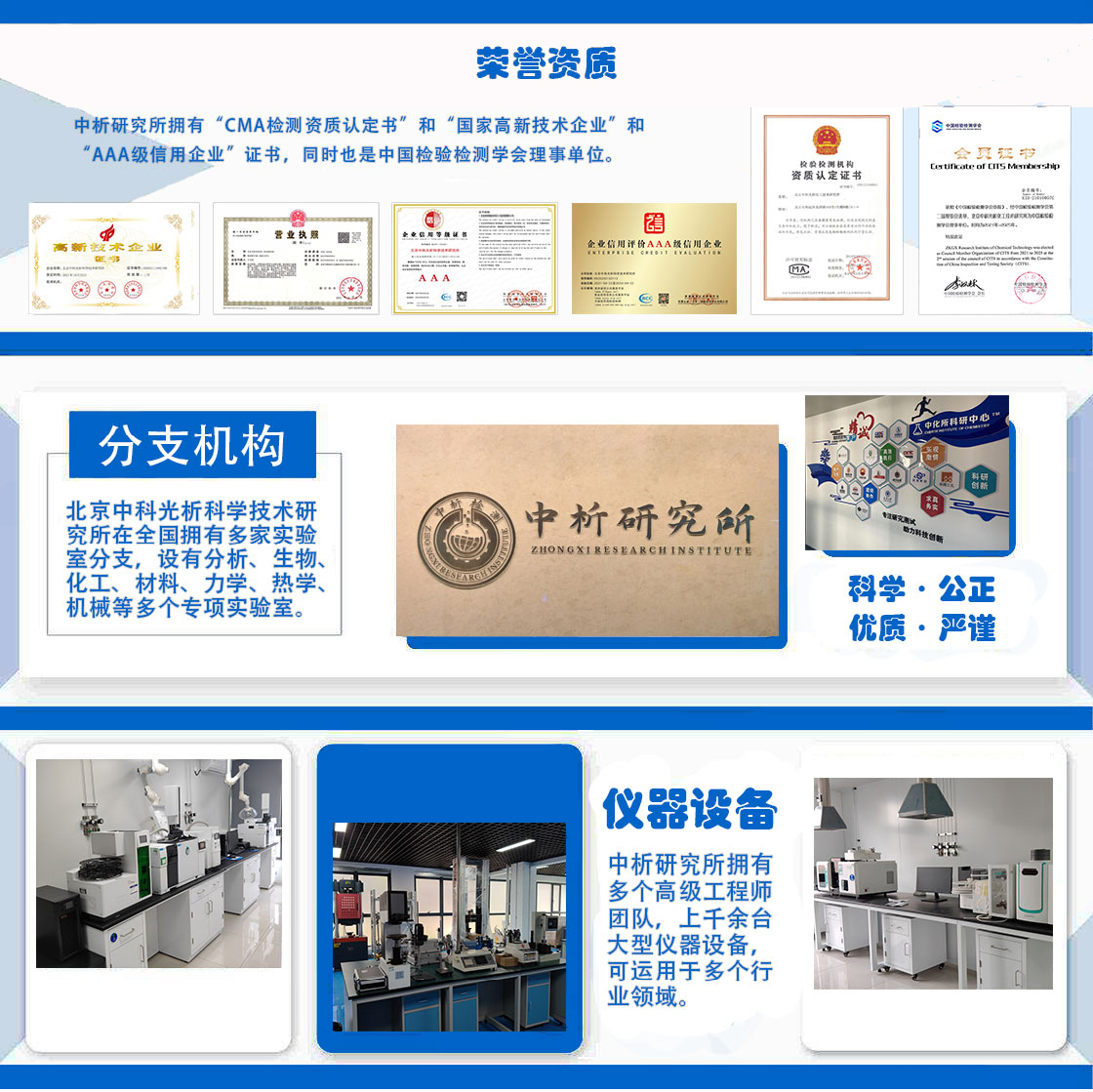
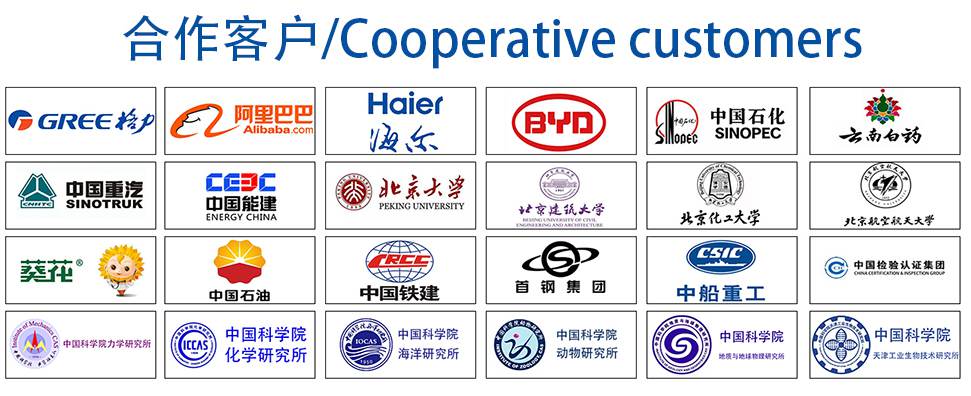