热熔胶订设备检测的重要性
热熔胶订设备是印刷、包装、书籍装订等领域的关键生产设备,其性能直接影响产品粘合强度和生产效率。随着市场对产品外观和耐用性要求的提升,设备运行的稳定性、温度控制的精准性以及胶水涂布的均匀性成为核心关注点。通过系统性检测,可确保设备满足工艺标准,避免因设备故障导致的胶层开裂、粘接不牢等问题,同时降低能耗与生产成本。定期检测还能延长设备使用寿命,保障生产线的连续运转。
热熔胶订设备的核心检测项目
1. 设备参数校准检测
包括温度控制精度(胶槽、输胶管路)、压力传感器误差范围、传动系统同步性等。需通过专业仪器验证温控模块的±2℃误差是否符合标准,并检查气压/液压系统输出压力的稳定性。
2. 胶槽与输胶系统检测
重点评估胶槽加热均匀性(采用多点测温法)、输胶泵流量一致性(误差需≤3%)以及胶液残留量控制能力。需模拟不同工况检测输胶管路是否堵塞或渗漏。
3. 施胶机构性能测试
检测刮胶刀平整度、施胶轮转速匹配度及胶层厚度波动范围(通常要求≤0.05mm)。通过试生产验证胶线宽度是否符合设计要求,观察是否存在断胶、溢胶现象。
4. 安全防护与能耗分析
检查设备过热保护装置响应时间(应≤3秒)、紧急制动功能有效性,同时监测单位产量的电能与胶料消耗量,评估设备能效比是否达标。
5. 成品质量关联性检测
通过破坏性试验验证粘接强度(如180°剥离力测试),并利用恒温恒湿箱模拟环境变化后的胶层耐久性,确保产品通过行业标准(如QB/T 1961-2011)。
智能检测技术的应用趋势
现代热熔胶订设备逐步集成IoT传感器与AI算法,实现实时温度补偿、胶量预测调节等功能。检测过程中可通过数据采集系统分析设备运行曲线,预判机械磨损、加热元件老化等潜在故障,推动检测模式从被动维护向主动预防转变。
总结
热熔胶订设备的检测需覆盖机械性能、工艺参数、安全规范及成品质量多维度指标。通过标准化检测流程与智能化技术结合,企业可显著提升设备综合性能,在保证产品质量的同时实现降本增效的目标。
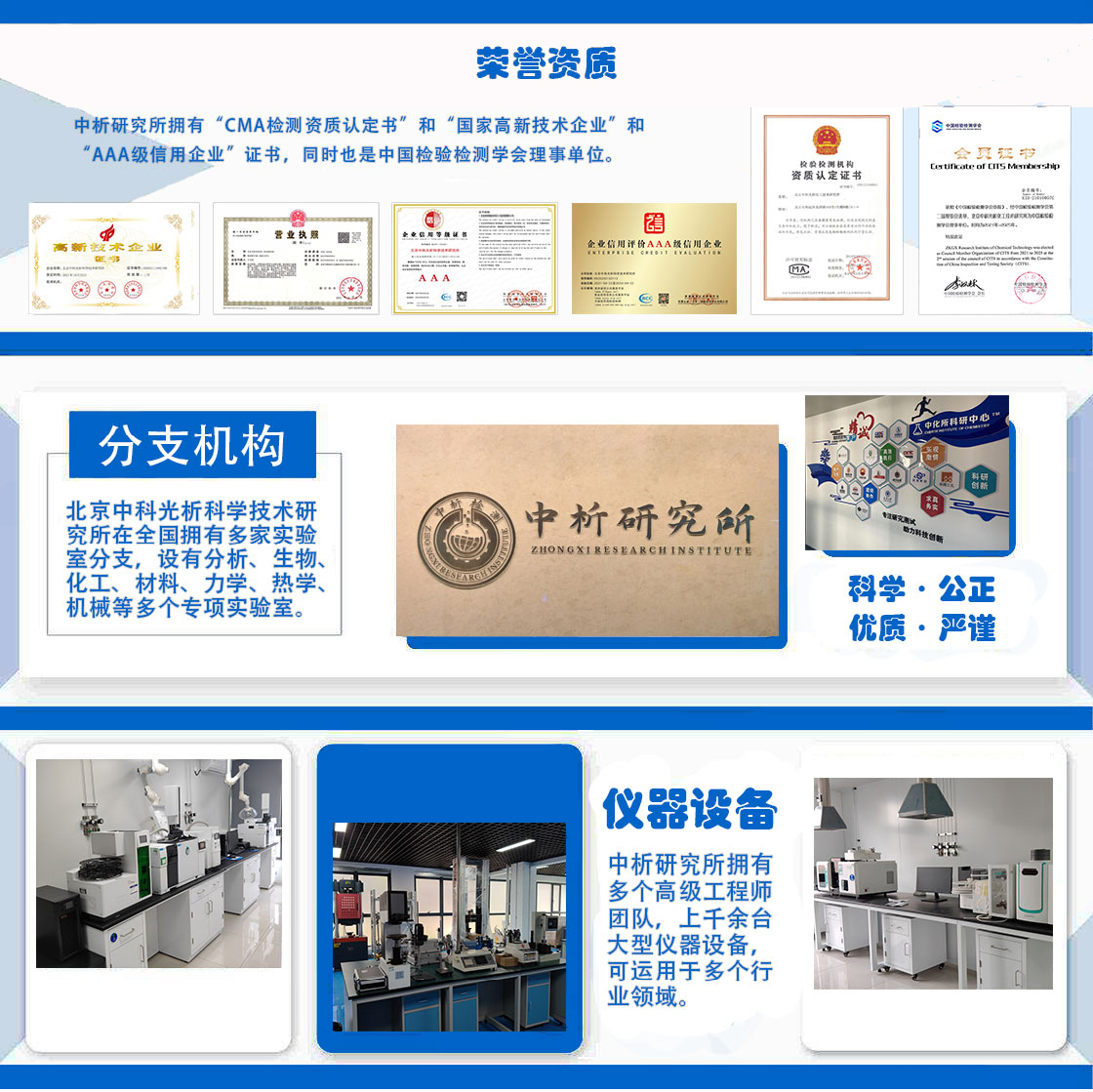
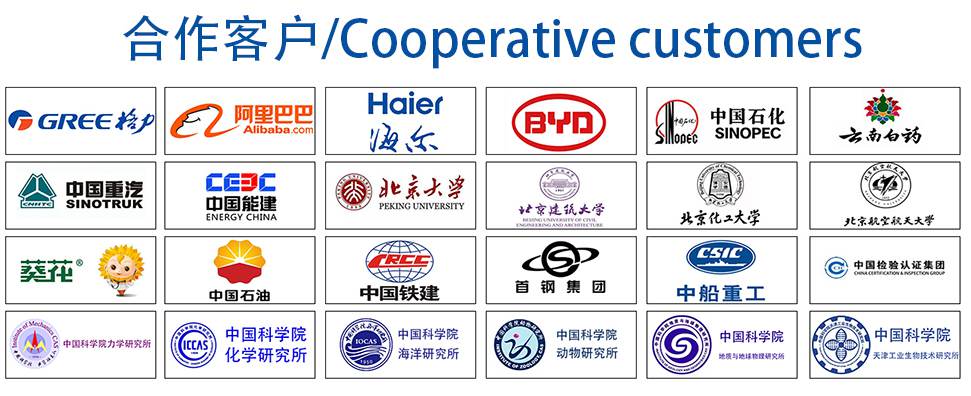