再制造内燃机检测项目的核心内容与技术要求
再制造内燃机作为循环经济与绿色制造的重要实践方向,通过修复、升级或替换旧机部件实现资源高效利用,其性能与可靠性须达到甚至超过新机标准。在这一过程中,检测环节是保障再制造产品质量的核心手段,涉及机械性能、材料特性、排放合规性等多维度指标。科学的检测体系不仅能够验证再制造工艺的有效性,还能为企业降低返修成本、提升市场信任度提供技术支撑。
1. 基础尺寸与几何精度检测
再制造内燃机的核心部件(如缸体、曲轴、凸轮轴等)需通过三坐标测量仪、激光扫描仪等设备进行几何参数验证,确保关键尺寸公差(如缸径圆度、曲轴轴颈跳动量)符合原厂技术规范。对于存在磨损或变形的部件,需评估是否满足再制造修复余量要求,避免因尺寸超差导致装配失效。
2. 材料性能与表面状态分析
采用显微硬度计、金相显微镜对部件表面及基体进行检测,重点监控关键运动副(如活塞环槽、气门座圈)的硬化层深度和显微组织状态。同时通过磁粉探伤、超声波探伤等技术排查裂纹、气孔等缺陷,对于复合修复工艺(如激光熔覆、电弧喷涂)需额外检测结合界面致密性。
3. 装配质量与动态平衡测试
整机装配过程中需执行扭矩校验、间隙测量等工序控制,并使用动平衡机验证曲轴组件的平衡精度(残余不平衡量≤15g·mm)。涡轮增压器转子等高速旋转部件需单独进行超速试验,确保在120%额定转速下无异常振动或变形。
4. 台架性能与排放合规性验证
在标准试验台架上进行冷热启动、负荷特性曲线、耐久性等测试,功率输出偏差应控制在±3%以内。排放检测需满足国六/欧Ⅵ标准,特别关注NOx(氮氧化物)与PM(颗粒物)的实时浓度。对于电控系统单元,还需通过OBD诊断接口验证传感器数据准确性与故障码响应逻辑。
5. 密封性与耐久性专项检测
采用氦质谱检漏仪对燃油系统、冷却系统进行密封性测试,泄露率需低于10-5 Pa·m3/s。模拟实际工况进行500小时强化试验,监测机油消耗率(≤0.1%燃油消耗量)与气缸压缩压力衰减幅度(周期降幅<5%)。
检测标准的迭代与智能化升级
随着再制造工艺的进步,检测体系正逐步融合AI视觉识别、工业CT断层扫描等新技术。通过建立数字化检测数据库,企业可实现历史数据的趋势分析与工艺优化,推动再制造内燃机检测从单一合格判定向全生命周期质量管控转型。
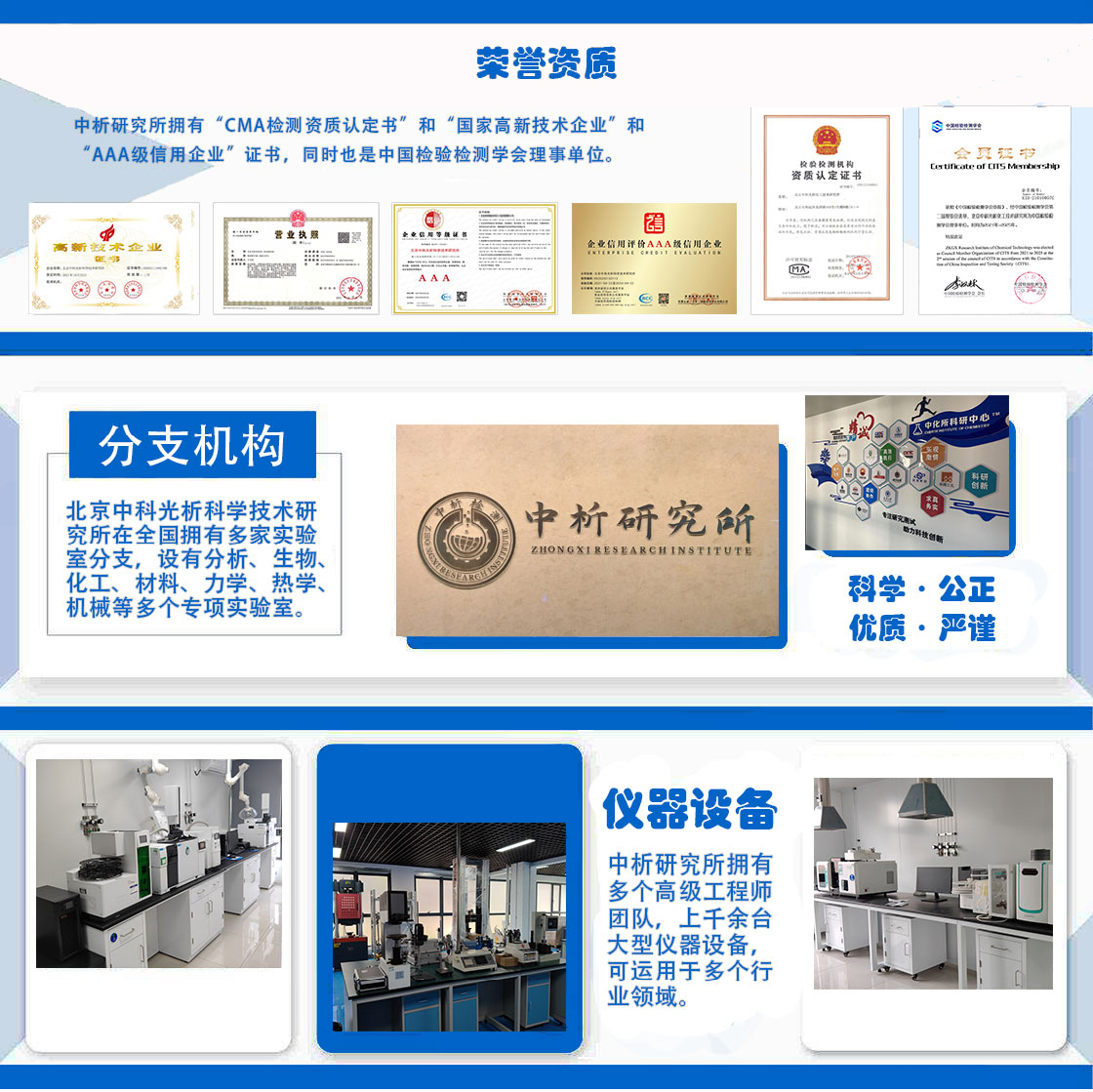
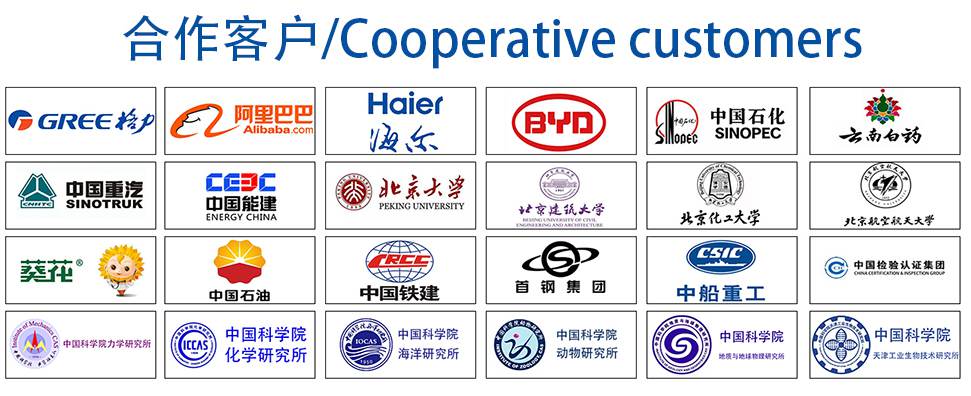