单柱塞式分配泵总成检测技术解析
单柱塞式分配泵作为液压系统的核心组件,广泛应用于工程机械、农业设备和工业生产线中,其性能直接影响设备的动力传递效率和运行稳定性。该泵通过柱塞的往复运动实现高压油液的精准分配,对密封性、压力响应和流量精度要求极高。为确保其长期可靠运行,需建立科学的检测体系,涵盖制造验收、装机前调试及周期性维护全流程。以下从结构特性出发,系统阐述单柱塞式分配泵总成的关键检测项目及技术要求。
密封性能检测
通过加压试验台模拟额定工作压力的1.5倍工况,持续保压15分钟,采用压降法判定主密封圈、柱塞副及阀座接合面的渗漏情况。要求静态泄漏量不超过0.05ml/min,动态工况下压力波动幅度需控制在±2%范围内。同步运用荧光示踪剂检测微观渗漏通道。
流量分配均匀性测试
在标准试验油温(50±2℃)条件下,使用多通道高精度流量计同步采集各出油口的瞬时流量。当柱塞行程频率达到额定转速时,各支路流量偏差应小于3%。重点分析分配器凸轮型线磨损导致的周期性波动,要求流量不均匀度系数δ≤0.8。
压力脉动特性评估
利用动态压力传感器记录泵出口压力波形,通过FFT频谱分析识别由柱塞换向冲击引起的压力波动。要求基频脉动峰值不超过平均压力的8%,高频谐波分量衰减率需达到-20dB/oct以上。异常脉动可能预示配流盘磨损或预紧弹簧失效。
机械部件配合精度检测
采用三坐标测量仪核查柱塞副配合间隙(标准值5-8μm),柱塞圆柱度误差须≤1.5μm。使用扭力测试仪验证斜盘调节机构的操作力矩,全程调节应平稳无卡滞,力矩波动值≤0.3Nm。同时检测轴承游隙是否在0.02-0.04mm设计范围内。
材料耐久性验证
通过金相分析评估关键部件(柱塞、缸体)的硬化层深度(≥0.3mm)及显微硬度(HRC58-62)。进行200小时交变负荷耐久试验后,检测摩擦副表面粗糙度Ra值变化量应小于0.1μm,且无可见剥落或划痕。
智能诊断技术应用
集成振动加速度传感器与声发射检测装置,建立泵体振动特征数据库。通过BP神经网络算法识别早期故障模式,如斜盘轴承点蚀引发的5-8kHz特征频率,实现磨损状态的定量评估与剩余寿命预测。
通过上述多维度的检测体系,可精准定位单柱塞式分配泵总成的性能缺陷,为优化设计参数、改进装配工艺提供数据支撑,同时指导用户制定预防性维护策略,有效降低设备故障率。随着在线监测技术的发展,检测流程正逐步向智能化、实时化方向演进。
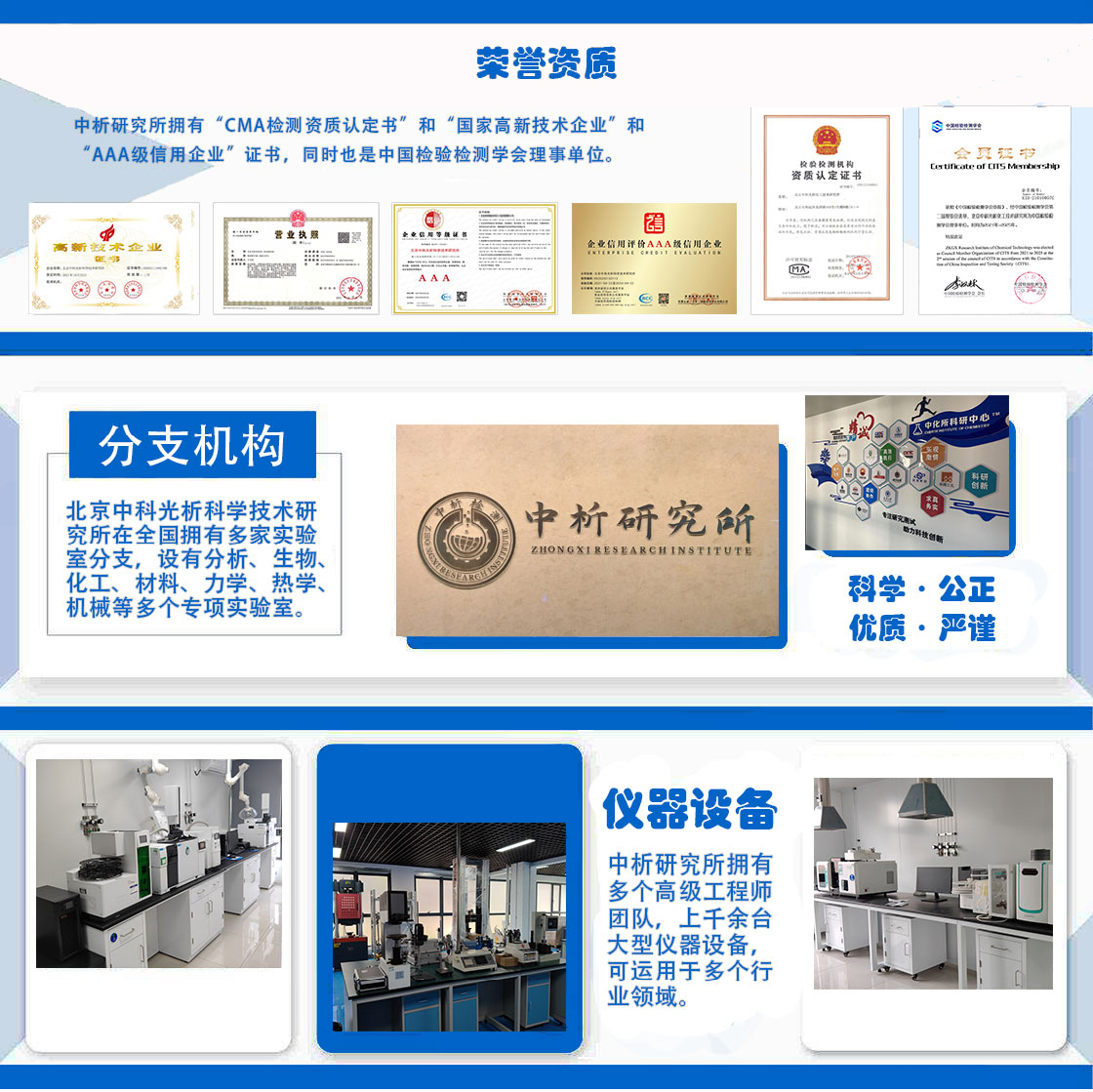
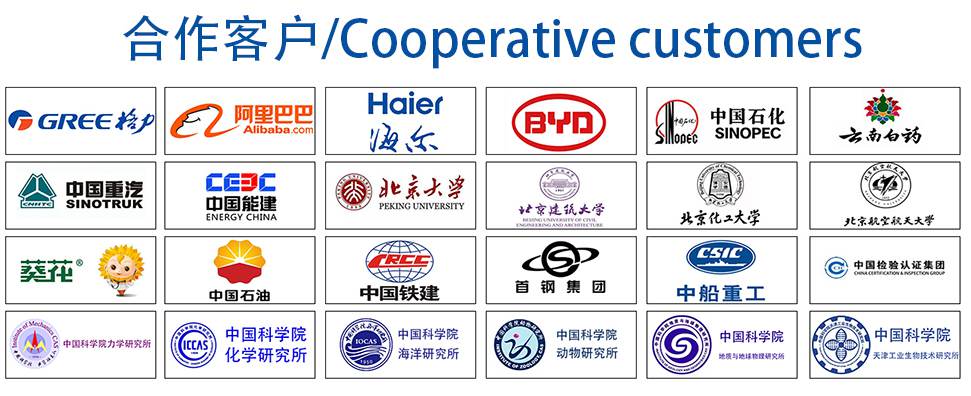