喷漆机器人检测的关键意义与技术挑战
在汽车制造、家电生产及工业设备加工领域,喷漆机器人凭借高效率、高精度和环保优势逐渐取代传统人工喷涂。随着自动化程度不断提升,如何确保喷漆质量的稳定性和工艺参数的合规性成为行业关注焦点。喷漆机器人检测贯穿于设备调试、过程监控与成品验收全周期,涉及机械性能、喷涂效果、环境参数等多维度评估,直接影响产品外观质量、防腐性能及生产成本控制。其核心目标是通过系统性检测验证机器人轨迹精度、涂料覆盖均匀度及涂层性能,避免因参数偏差导致的返工、废品率上升等问题。
核心检测项目分类与实施方法
1. 机械运动系统检测
通过激光跟踪仪或动态捕捉系统验证机器人重复定位精度,要求六轴关节运动误差≤±0.1mm。同步检测末端执行器的线性速度稳定性(波动率<5%)和加速度响应特性,确保复杂曲面喷涂时轨迹无抖动。采用力矩传感器监测各关节负载变化,识别传动系统异常磨损。
2. 喷涂质量参数检测
使用超声波测厚仪(分辨率0.1μm)检测干/湿膜厚度,结合红外光谱分析仪验证涂层固化程度。部署多角度色差仪(ΔE≤0.5)进行色彩一致性检测,采用网格法(ASTM D3359标准)测试涂层附着力。对于金属漆等特殊涂料,需增加粒径分析仪监测雾化颗粒分布状态。
3. 环境控制系统检测
在喷房关键位点布置温湿度传感器组(精度±1%RH/±0.5℃),确保温度控制在20-25℃、湿度40-60%RH。通过风速仪验证层流风速稳定性(0.2-0.5m/s),使用粉尘粒子计数器监控空气洁净度(ISO 14644 Class 5标准)。
4. 智能化监测系统验证
对机器视觉系统进行MTF调制传递函数测试,确保CCD相机的空间分辨率≥5μm/pixel。测试缺陷识别算法在气泡、流挂、橘皮等典型异常中的检出率(要求≥98%),验证PLC控制系统对于喷涂压力(0.3-0.6MPa)、雾化气压(0.4-0.8MPa)等参数的闭环控制精度。
检测技术创新与行业发展趋势
当前喷漆机器人检测正朝着多模态融合方向发展,集成高光谱成像(120波段以上)、太赫兹波检测等新技术,可同步获取涂层厚度、成分及内部缺陷数据。基于数字孪生的虚拟检测系统实现工艺参数预测优化,5G+边缘计算架构使实时质量追溯成为可能。未来行业将更注重建立覆盖设计-生产-服务的全生命周期检测体系,推动喷漆机器人向智能化、自适应化方向演进。
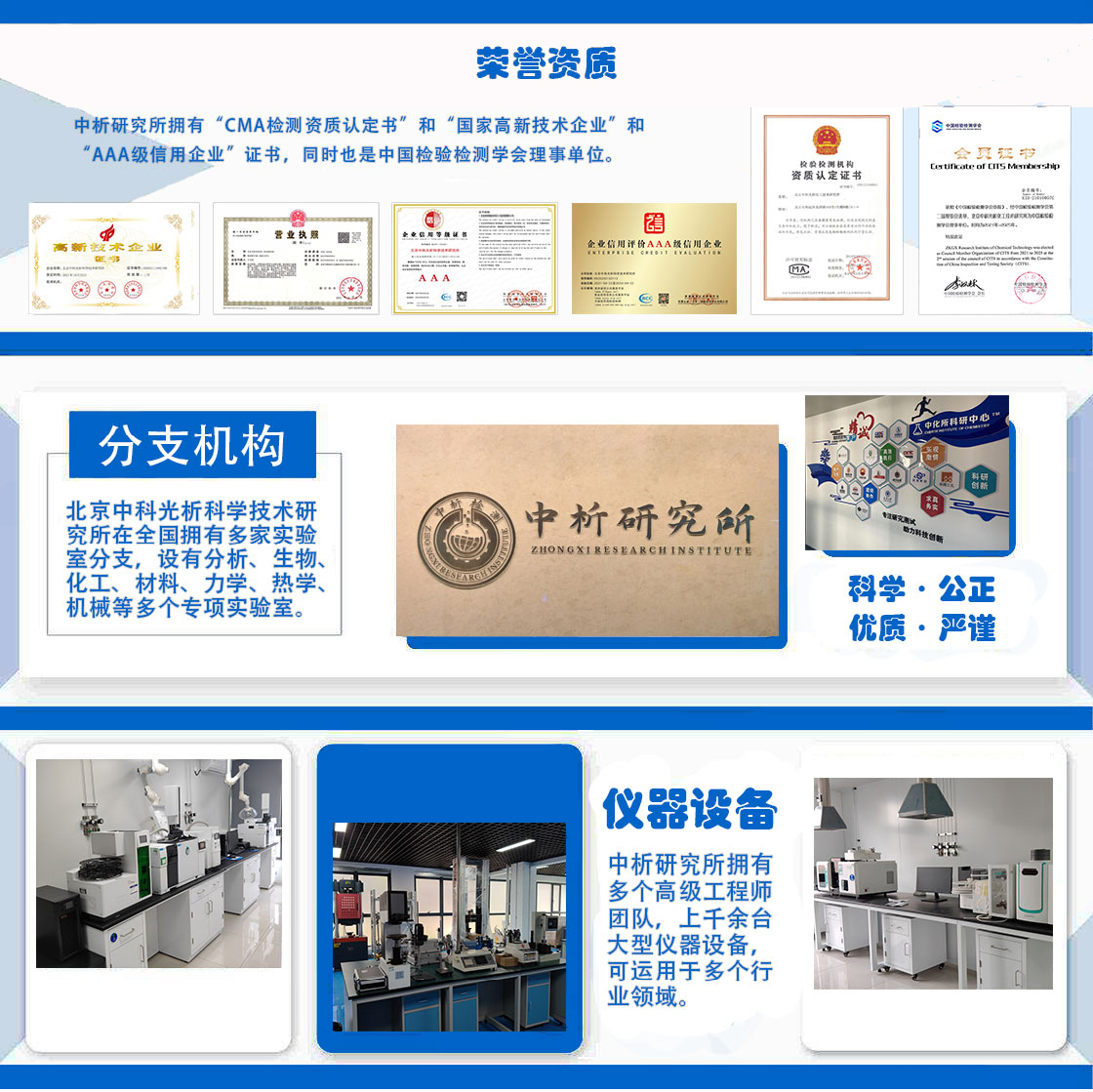
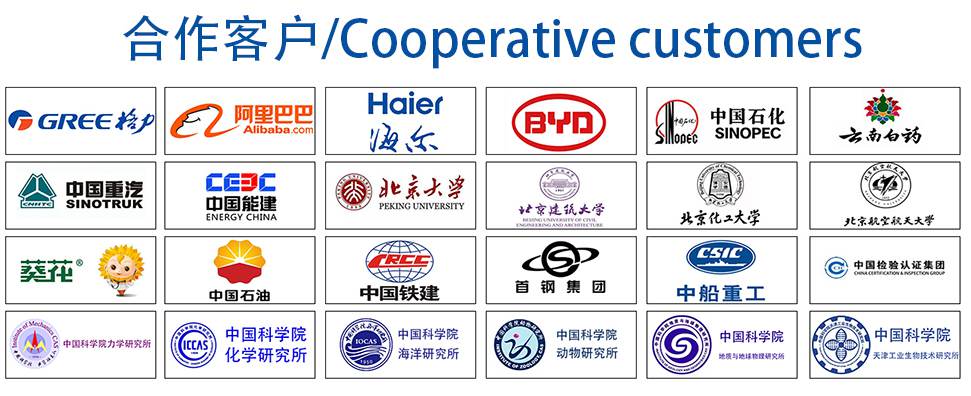