工业用含碱或其他非酸性电解质锂离子电池及蓄电池组检测的重要性
随着新能源技术的快速发展,工业用锂离子电池及蓄电池组因其高能量密度、长循环寿命和环保特性,广泛应用于储能系统、电动车辆、工业设备等领域。然而,含碱或其他非酸性电解质的锂离子电池在复杂工业环境中可能面临过充、高温、机械冲击等安全风险。为确保其安全性和可靠性,对电池及蓄电池组进行系统性检测已成为产业链中不可或缺的环节。这些检测不仅涉及基础性能验证,更涵盖极端工况下的安全边界评估,是国际认证、市场准入和产品质量控制的核心依据。
核心检测项目分类
1. 安全性能测试
包含过充/过放保护测试、短路保护测试、热冲击试验及机械冲击测试。通过模拟电池在异常工况下的反应,评估防爆阀激活、隔膜熔断等安全机制的有效性,确保电池在极端条件下不起火、不爆炸。
2. 电气性能验证
涵盖容量测试(0.2C/1C放电效率)、内阻分布检测、循环寿命试验(>2000次充放电)及自放电率测定。采用高精度充放电设备跟踪电压-电流曲线,评估能量衰减特性与一致性指标。
3. 环境适应性检测
包括高低温循环试验(-40℃~85℃)、湿热交变测试(95%RH)、低气压模拟(11.6kPa)及振动/冲击耐久性验证。重点考察电解液稳定性、极片膨胀率等参数在极端环境下的变化规律。
4. 化学兼容性分析
针对非酸性电解质的特殊配方,进行正负极材料SEM/EDS微观形貌分析、电解液气相色谱检测(GC-MS),以及隔膜耐腐蚀性测试。验证材料体系在长期运行中的化学稳定性。
国际标准与检测规范
检测需符合IEC 62619(工业锂电池安全)、UL 1973(储能系统标准)、UN 38.3(运输安全)及GB/T 36276(电力储能标准)。其中针刺试验(模拟内短路)、热失控传播测试(模块级)等特色项目被纳入最新版强制性认证要求。
检测流程与技术创新
现代检测采用多参数联动监测系统,通过嵌入式传感器实时采集温度场分布、气体逸出等数据。结合AI算法建立失效预警模型,实现从单电池到模组的全维度安全评估。第三方实验室还需配备防爆测试舱、热成像仪等专用设备,确保测试过程的可控性与可重复性。
行业发展趋势
随着固态电解质技术的突破,检测项目正向原位表征技术延伸,如X射线衍射(XRD)在线监测晶体结构变化。同时,针对钠离子电池等新型体系的检测标准正在制定中,推动行业向更安全、更环保的方向发展。
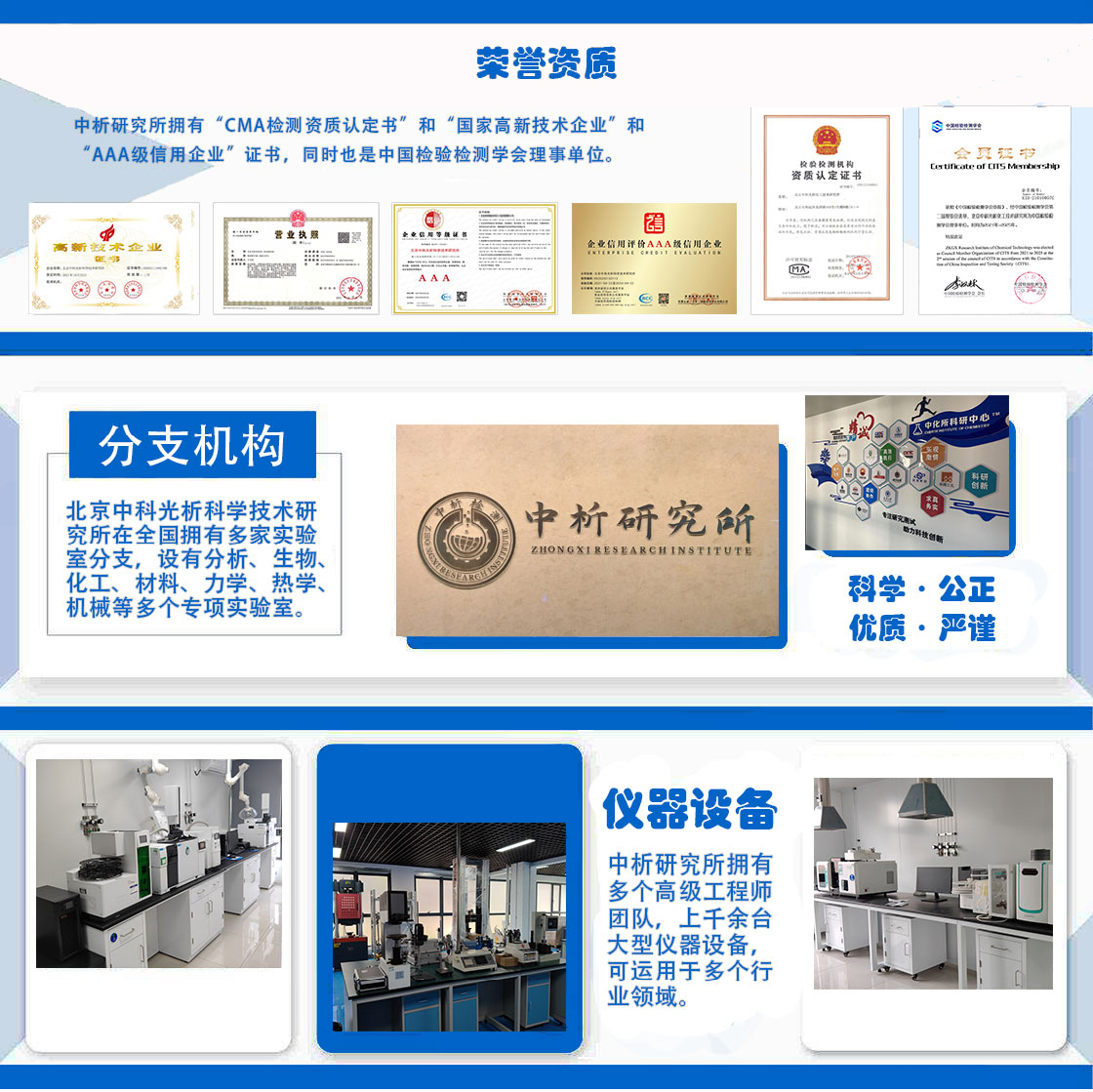
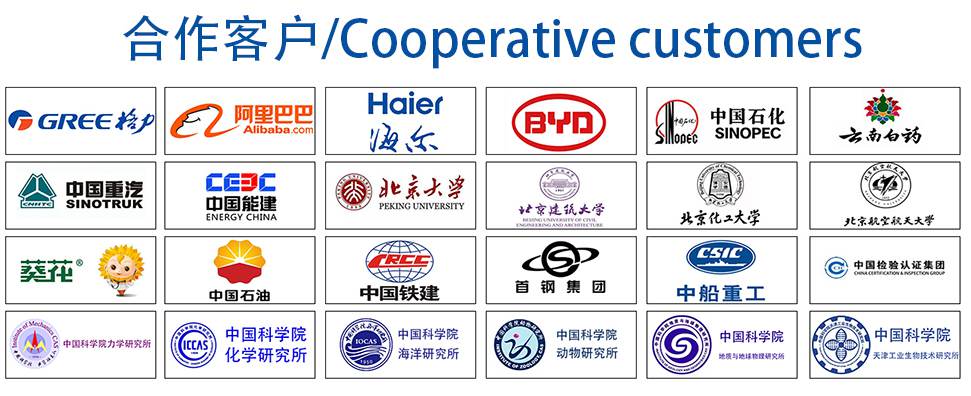