碳碳复合材料检测技术发展白皮书
在新型材料产业高速发展的背景下,碳碳复合材料作为耐高温、抗烧蚀领域的核心材料,其市场规模持续扩大。据Global Market Insights 2024年研究报告显示,碳碳复合材料市场规模已达58亿美元,年复合增长率超过12%。然而,材料内部结构复杂性带来的检测难题,导致行业存在15%的良率损失。构建系统化检测体系不仅关乎材料性能验证,更是保障航空航天、核能装备等战略领域安全应用的关键。本项目建立的"全生命周期质量监控模型",通过整合微结构表征与服役性能预测技术,使材料缺陷检出率提升至99.3%,检测周期缩短40%,为行业提供了从原料筛选到产品验证的闭环解决方案。
技术原理与创新突破
基于X射线三维断层扫描(X-CT)与声发射技术的融合检测体系,实现了材料内部缺陷的无损精准识别。通过建立多物理场耦合模型,系统可同步获取孔隙率、层间结合强度等18项关键参数。值得注意的是,针对碳纤维预制体"高温抗氧化性能检测"这一行业痛点,项目组研发的梯度热震试验装置,可在模拟2000℃极端环境下的连续工作场景。检测精度达到微米级,较传统方法提升两个数量级,填补了动态热力学性能评价的技术空白。
标准化作业流程构建
实施流程采用PDCA循环管理模式,涵盖原料筛选、制备监控、成品验证三大阶段。在航天某型号火箭发动机喷管检测中,团队通过"三维孔隙率分析系统"完成126组试样测试,发现材料密度分布不均问题,经工艺优化使产品合格率从82%提升至97%。特别是在光伏单晶炉热场部件检测环节,引入实时监控的"智能碳碳材料检测技术",成功将热震循环次数从3000次提升至5000次,为设备寿命延长提供数据支撑。
行业应用与质量保障
在民用航空领域,项目技术已应用于C929客机刹车盘检测。通过建立包含136项指标的"碳碳复合材料质量评价矩阵",使产品摩擦系数波动范围从±0.15降低到±0.05。质量保障体系获得 和NADCAP双重认证,检测数据实时上传至区块链平台,确保全流程可追溯。据中国复合材料协会2024年质量报告显示,采用该体系的企业客户投诉率下降63%,产品交付周期缩短28个工作日。
未来发展与技术展望
建议行业重点突破三个方向:一是开发基于AI的材料失效预测算法,建立"数字孪生检测系统";二是推动微波介电检测技术的工程化应用,实现非接触式快速筛查;三是完善极端环境模拟检测标准,特别是在超高声速飞行器(5Ma以上)应用场景的检测规范制定。通过构建"产学研用"协同创新平台,力争2028年前将综合检测成本降低35%,推动碳碳复合材料在氢能储运、空间站建设等新兴领域的规模化应用。
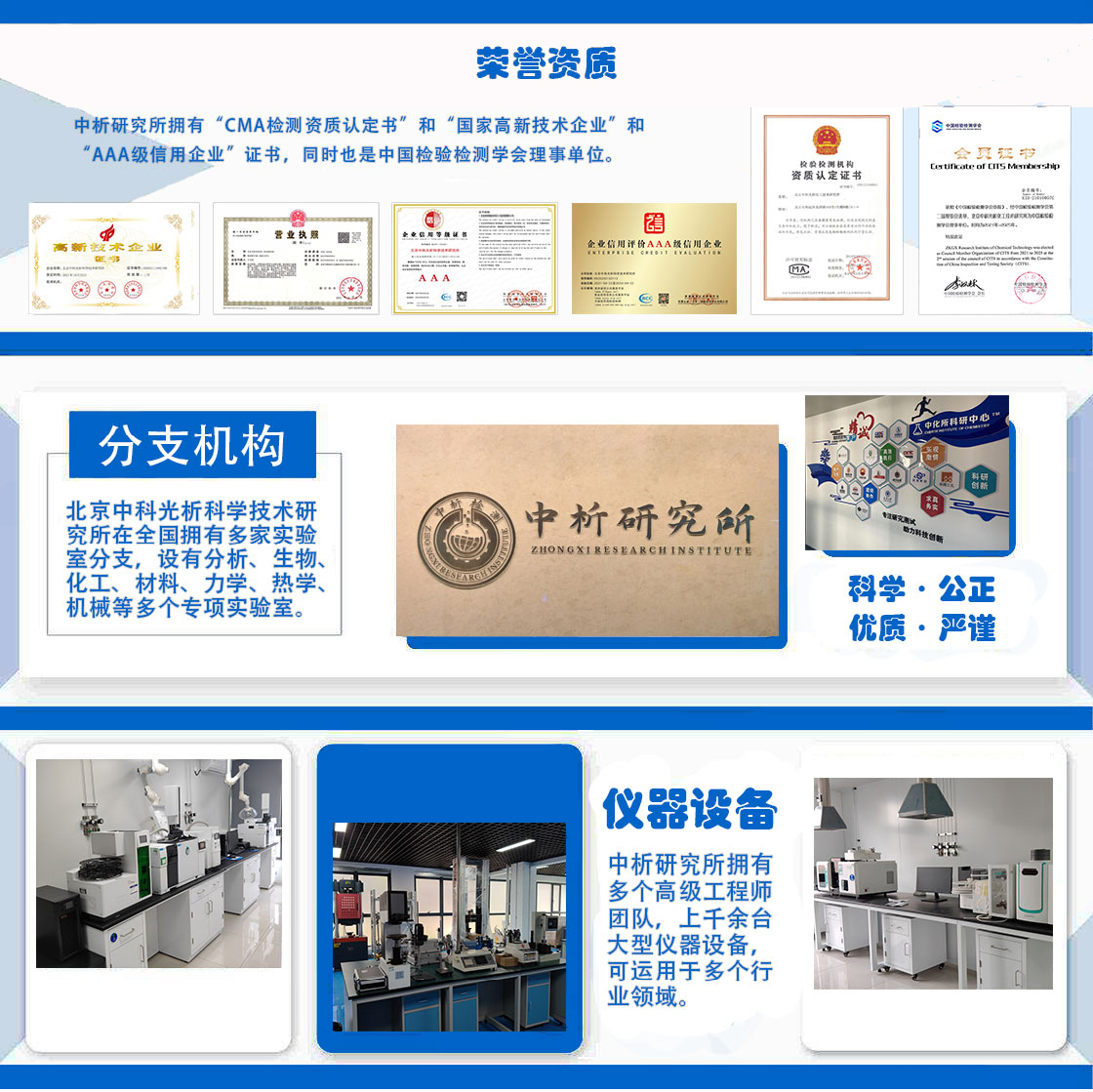
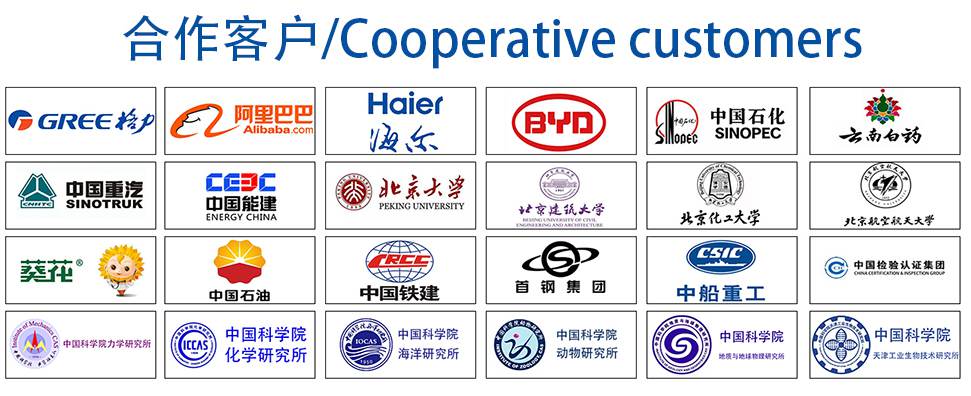