在水利水电、港口航道、交通工程等领域,混凝土结构长期承受水流、泥沙等介质的冲击磨损,其耐久性问题直接影响工程安全与服役寿命。据中国水利水电科学研究院2024年数据显示,我国年均因冲磨破坏导致的混凝土结构维修费用超120亿元,其中30%的损坏可通过科学检测实现早期预防。抗冲磨试验检测作为材料耐久性评估的核心手段,通过量化混凝土在动态荷载下的抗损能力,为工程设计优化、运维决策提供关键数据支撑。其核心价值体现在三方面:一是突破传统目视检查的局限性,实现结构性能量化评价;二是通过检测数据指导高性能混凝土研发,提升"水利工程抗冲磨检测标准"执行效果;三是建立全寿命周期健康档案,助力基础设施智慧化管理体系建设。
## 技术原理与创新突破1. 多维度检测技术体系构建
现行抗冲磨试验主要基于ASTM C1138水下钢球法和DL/T 5150旋转射流法两大体系。前者通过钢球介质模拟水流磨蚀环境,测定单位面积质量损失率;后者采用高压水砂射流模拟高速含沙水流,记录试件表面磨损深度。2023年新发布的JT/T 1492标准创新性引入三维激光扫描技术,将检测精度提升至0.01mm级,并能构建磨损表面数字化模型。值得关注的是,智能传感技术的应用实现了"混凝土抗冲磨性能优化方案"的动态修正,通过实时监测磨损速率变化,为材料配比调整提供即时反馈。
2. 标准化检测实施流程
完整的检测流程包含五个阶段:试样制备阶段需确保混凝土养护龄期达28天且湿度控制于60±5%;环境模拟阶段根据工程实际选择淡水或海水介质,含砂量控制在10-30kg/m³;力学加载阶段采用液压伺服系统,冲击速度保持在3-5m/s区间;数据采集阶段同步记录质量损失、表面形貌、声发射信号等12项参数;结果分析阶段通过Weibull分布模型评估材料失效概率。交通运输部2024年工程检测指南特别强调,对于跨海大桥桩基等特殊部位,需开展200小时持续冲刷模拟以获取长期性能数据。
3. 行业典型应用案例分析
在金沙江某水电站项目中,检测团队运用改进型旋转射流装置,发现二级配混凝土在含砾水流中的磨损速率达2.3mm/年,超出设计允许值40%。据此提出的"硅粉-钢纤维复合增强技术"使抗冲磨强度提升65%,经3年运行验证,泄洪洞底板厚度损失量减少至0.8mm/年。另一典型案例是港珠澳大桥人工岛护面块体检测,通过建立波浪-结构耦合模型,优化后的C60高性能混凝土使设计使用年限从50年延长至80年,该项目成果获2023年度中国土木工程詹天佑奖。
4. 全链条质量保障体系
检测质量管控涵盖设备、人员、环境三大维度:试验机每年需经国家计量院进行力值校准,误差控制在±1%以内;操作人员必须持有CMA认证检测师证书,并每季度参与比对试验;环境实验室须维持温度23±2℃、湿度50±10%的恒温恒湿条件。中国建筑科学研究院2024年测评报告显示,采用区块链技术的检测数据存证系统,使报告可追溯率达到100%,有效杜绝数据篡改风险。针对特殊工程需求,部分重点实验室已配置可模拟-20℃至40℃温变、盐雾浓度30g/m³的复合环境舱。
## 未来发展展望随着"交通强国"战略深入推进,抗冲磨检测技术将向智能化、标准化、精细化三方面发展。建议行业重点攻关三方向:一是开发基于机器视觉的在线监测系统,实现冲磨损伤的实时预警;二是建立全国性混凝土抗冲磨性能数据库,构建材料性能-环境参数-服役年限的预测模型;三是制定差异化的检测标准体系,针对海洋工程、高海拔地区等特殊环境制定专项检测规程。预计到2030年,智能检测装备渗透率将超过60%,检测成本降低35%,为推动基础设施高质量发展提供关键技术保障。
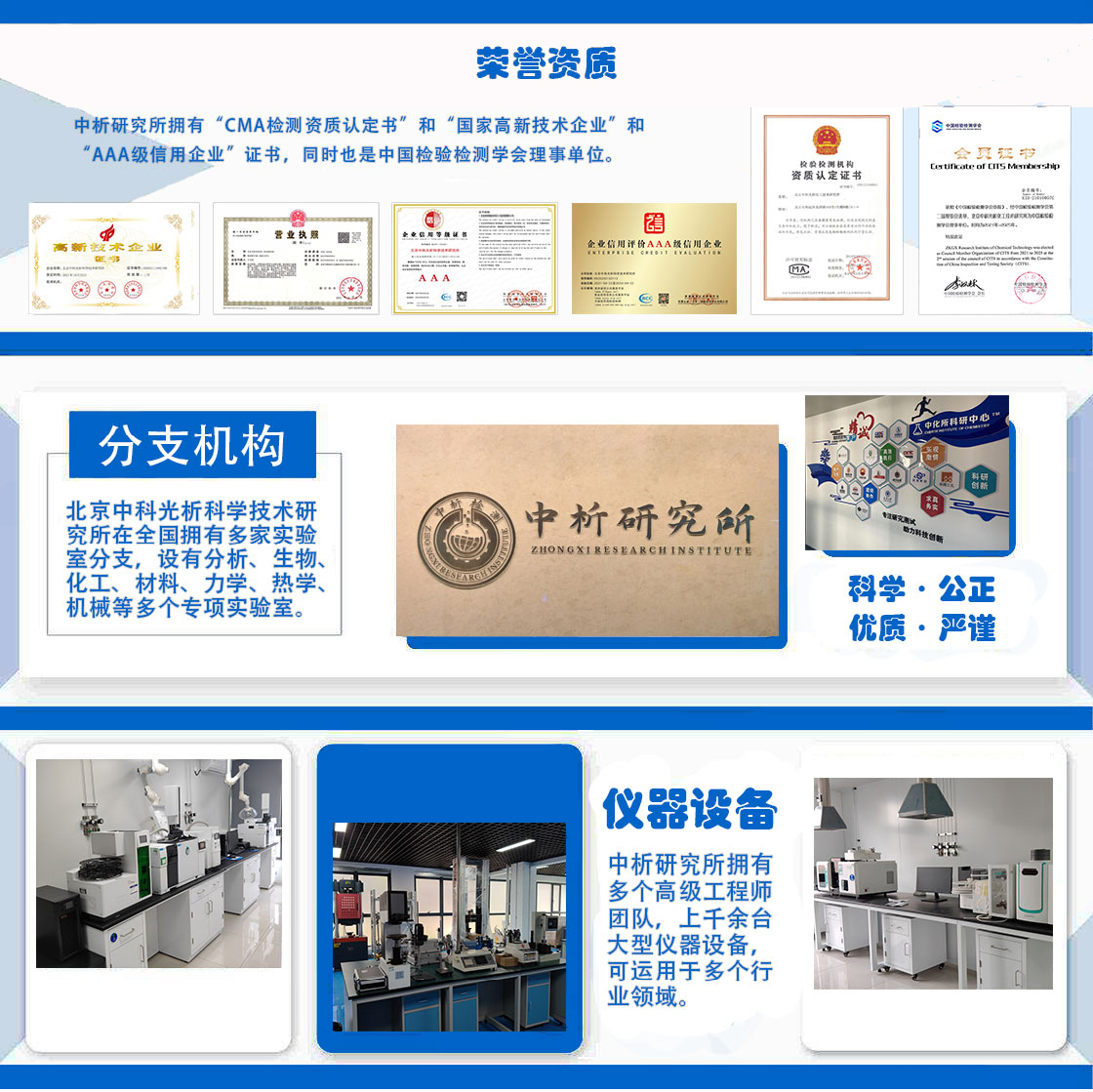
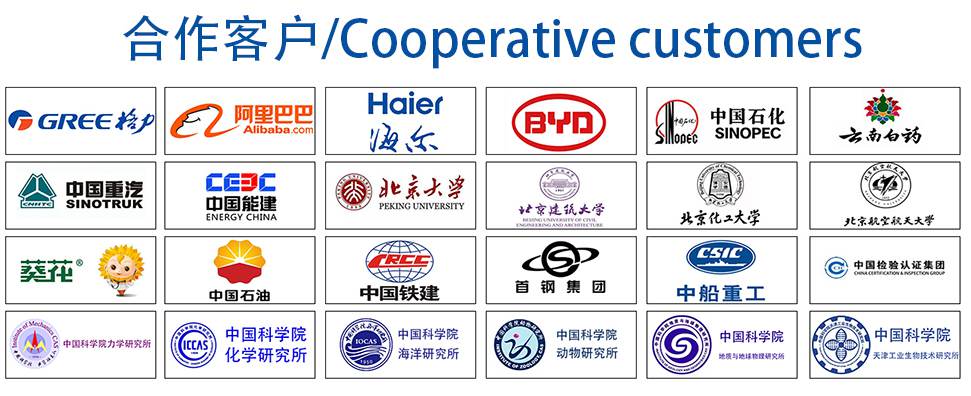