锚夹具硬度检测技术白皮书
在基础设施建设持续扩张的背景下,预应力锚夹具作为桥梁、隧洞及大型设备的核心连接部件,其力学性能直接关系工程结构安全。据中国机械科学研究总院2024年行业报告显示,我国每年因金属锚具失效引发的工程事故造成直接经济损失逾23亿元。锚夹具硬度检测项目通过量化评估材料抗变形能力,可有效预防应力集中导致的脆性断裂问题,其核心价值体现在质量预警周期缩短60%、部件使用寿命提升35%等方面。特别是在跨海大桥锚碇系统、盾构机推进装置等高压工况场景中,精准的硬度检测成为保障设备可靠运行的关键防线。
基于压痕法的硬度检测原理
现行检测体系采用洛氏硬度(HRC)与维氏硬度(HV)双标定体系,通过金刚石压头在设定载荷下形成压痕的深度/面积比推算材料强度。值得注意的是,为适应锚夹具特殊曲面结构,检测设备集成三维定位补偿算法,可将测量误差控制在±1.5HRC范围内(GB/T 230.1-2018标准)。针对大型锚板的现场检测需求,便携式超声波硬度计的应用突破传统实验室检测局限,实现0.2mm极薄硬化层的无损测量,该技术已在港珠澳大桥沉管隧道锚固系统维护中验证其有效性。
全流程质量管控实施路径
标准检测流程涵盖预处理、基准校正、多点检测三大阶段。预处理环节要求被检件表面粗糙度Ra≤0.8μm,消除氧化层与加工硬化影响;基准校正采用标准硬度块进行设备线性度校准,确保每批次检测数据可比性;多点检测策略依据JB/T 9377-2020规范,在锚具锥孔工作面实施网格化布点,单件采样点不少于9个。上海振华重工的质量报告显示,该流程使锚板硬度离散度从12%降至6%以内,显著提升产品一致性。
行业典型应用场景分析
在高铁轨道板预应力锚固系统领域,中铁四局引入自动化硬度检测线后,单个锚具检测耗时由45分钟缩短至8分钟,检测效率提升82%。更值得关注的是地下管廊施工场景,中交建集团项目组通过硬度梯度分析,成功预警某批次锚夹具表面硬化层厚度不足问题,避免价值1.2亿元的顶管机卡滞事故。这些实践印证了硬度检测在工程风险防控中的前置作用,尤其对预应力损失、氢脆倾向等隐蔽缺陷具有显著识别效果。
多维质量保障体系构建
检测机构需建立涵盖设备、人员、环境的立体质控网络:设备层面执行日校、周检、月审三级校验制度,配备激光干涉仪进行测深机构精度验证;人员资质严格遵循 -CL01:2018要求,检测工程师须持有金属材料热处理中级以上证书;环境控制方面,检测区温度波动需稳定在23±2℃,相对湿度≤65%。中检集团实验室比对数据显示,该体系下检测结果Z比分数稳定在0.8-1.2区间,达到国际互认水平。
面向新型基础设施建设需求,建议从三方面深化技术发展:一是开发基于机器视觉的硬度压痕智能判读系统,解决人工读数主观偏差问题;二是制定锚夹具硬度-疲劳寿命映射数据库,推动检测标准从单一指标向性能预测转型;三是构建"材料-工艺-检测"协同创新平台,特别是在高强钛合金锚具等新材料领域建立前瞻性检测方法。唯有持续创新,方能在保障工程安全的同时,助力我国高端装备制造业实现质量突围。
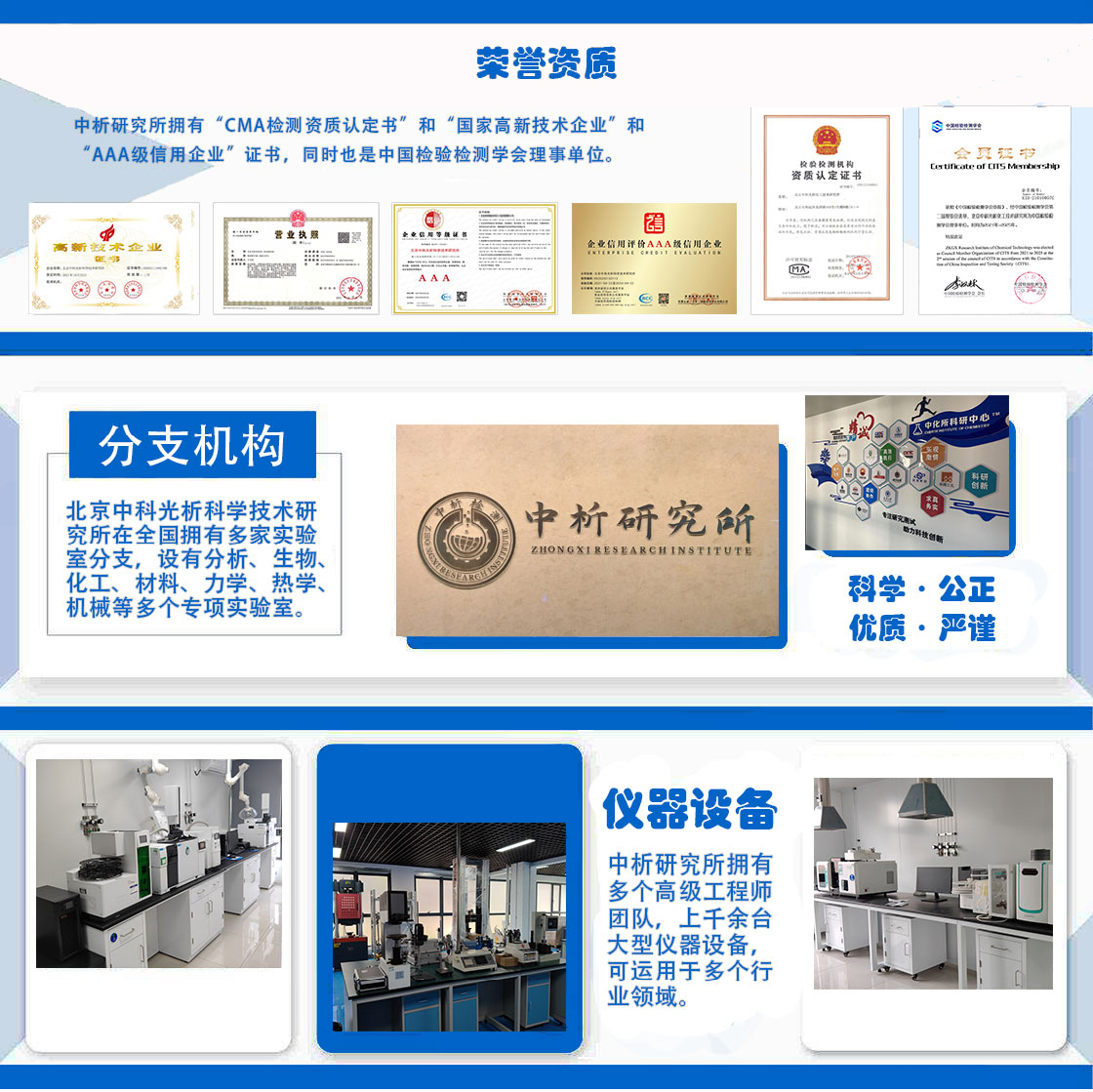
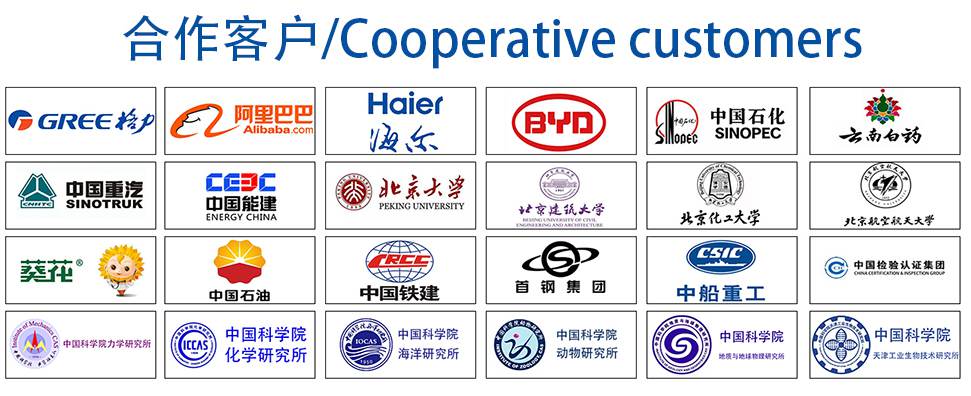