金属燃油箱检测的重要性与必要性
金属燃油箱作为车辆燃油系统的核心部件,其安全性和可靠性直接影响车辆运行安全与环境保护。由于长期暴露在高温、高压、腐蚀性介质及复杂工况下,燃油箱可能因材料疲劳、焊接缺陷或外部冲击导致泄漏、爆裂等风险。根据GB/T 18296-2017《汽车燃油箱安全性能要求和试验方法》等标准规定,金属燃油箱必须通过系统性检测来验证其结构强度、密封性及耐久性。通过科学规范的检测项目,可有效预防燃油泄漏引发的火灾隐患,同时确保产品符合国家强制性认证(如CCC认证)及国际标准要求。
关键检测项目及技术方法
1. 结构强度测试
通过液压爆破试验模拟燃油箱内部压力极限状态,检测箱体最大承压能力及变形情况。测试压力需达到标准规定的1.5倍工作压力并保持30分钟,要求无永久性变形或破裂。同时需进行落锤冲击试验,以验证燃油箱在遭受外部机械碰撞时的抗冲击性能。
2. 密封性检测
采用气压法或浸水法进行检测:将燃油箱充入50kPa压缩空气后浸入水中,观察2分钟内是否出现气泡;或通过压降法监测气密性,泄漏量需小于0.5L/h。此项目可精准发现焊缝、接缝处的微观渗漏缺陷。
3. 耐腐蚀性能测试
依据ISO 9227标准开展中性盐雾试验,连续喷洒5%氯化钠溶液720小时,评估箱体表面镀层或涂层的抗腐蚀能力。配套进行循环腐蚀试验(CCT),模拟湿热、盐雾、干燥等多环境交替作用,检测长期使用后的耐候性。
4. 焊接质量分析
采用X射线探伤检测焊缝内部气孔、夹渣等缺陷,配合金相显微镜观察焊缝微观组织形态。对关键焊缝进行拉伸试验,确保抗拉强度≥母材强度的90%。超声波测厚仪用于测量箱体壁厚均匀性,偏差需控制在±0.1mm内。
5. 环境适应性验证
通过高低温交变试验(-40℃~80℃)检测材料热胀冷缩特性,要求循环100次后无开裂或密封失效。振动测试模拟不同路况下的机械载荷,频率范围覆盖10-200Hz,持续8小时检测连接件松动风险。
检测设备与标准规范
主流检测设备包括万能材料试验机、三坐标测量仪、氦质谱检漏仪等,需定期进行计量校准。检测过程需严格参照GB/T 13239-2021《金属燃油箱技术条件》、ECE R34(欧盟车辆防火认证)等标准,同时结合企业内控质量体系(如IATF 16949)制定检测流程。
金属燃油箱的全面检测是保障车辆安全的重要防线。通过结构、材料、工艺等多维度测试,可系统性识别潜在缺陷,为产品设计优化和质量改进提供数据支撑。随着新能源汽车对轻量化金属油箱需求的增长,检测技术正朝着智能化(如AI缺陷识别)和高效化方向持续升级。
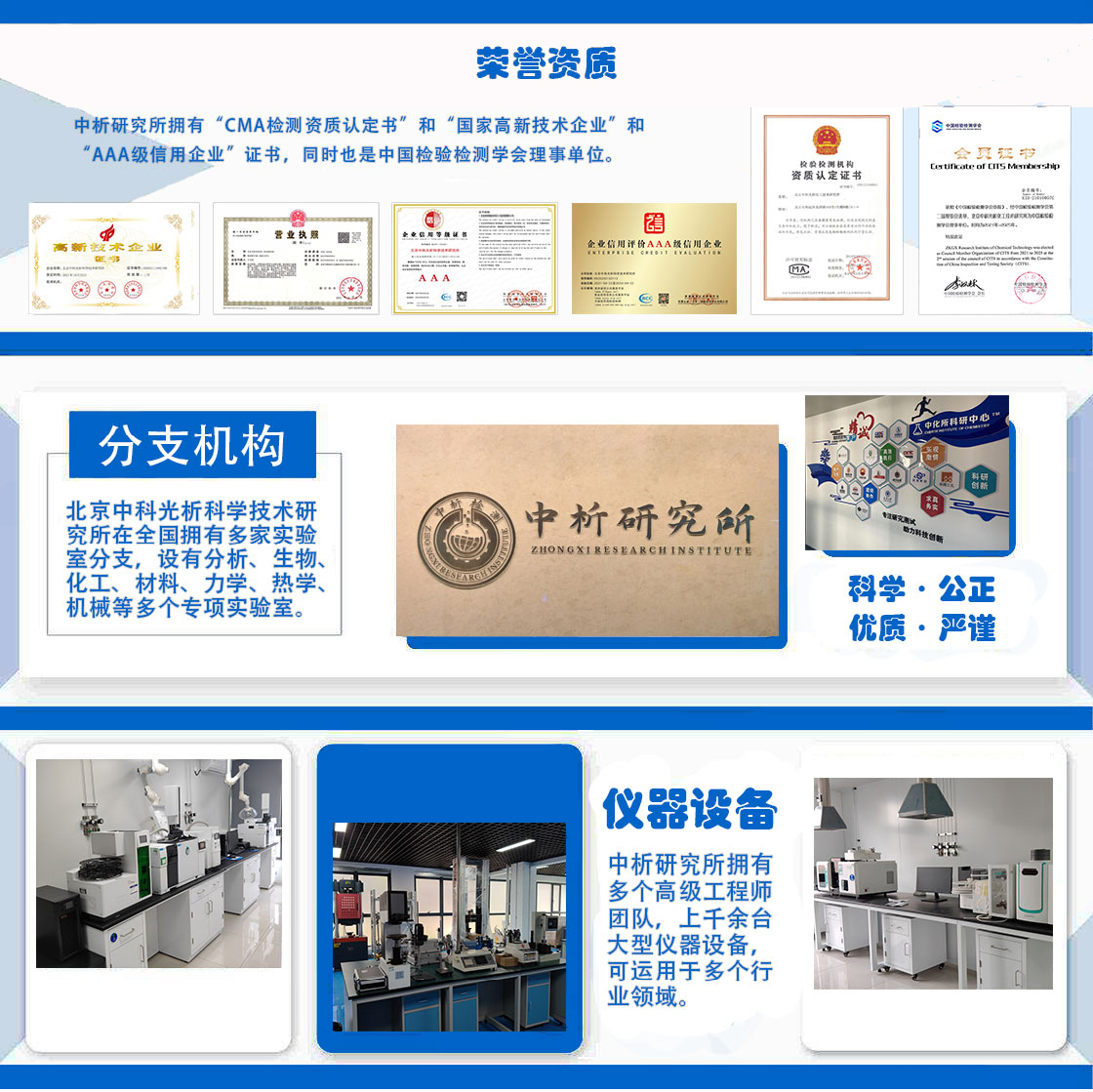
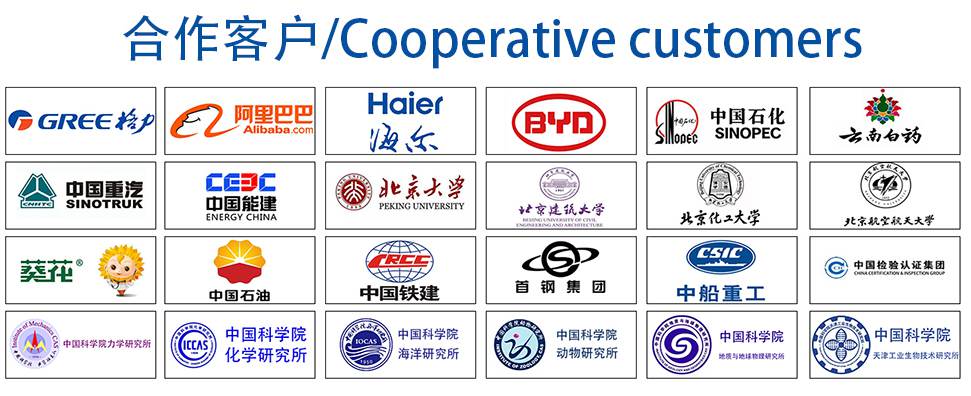