爆炸性环境用设备检测的重要性与技术要求
爆炸性环境是指空气中存在可燃气体、蒸气、粉尘或纤维等物质,与氧气混合后可能被引燃的危险场所,如石油化工、采矿、制药等行业的生产区域。在这些环境中使用的电气设备、机械装置及仪表工具,一旦发生火花、高温或电弧,可能引发灾难性爆炸事故。因此,针对爆炸性环境用设备的检测不仅是法律法规的强制要求,更是保障人员生命安全和生产稳定的核心措施。国际电工委员会(IEC)制定的IEC 60079系列标准、中国国家标准GB 3836等文件,均对这类设备的防爆性能、结构设计和检测流程提出了明确规范。
核心检测项目及技术要点
1. 防爆结构认证检测
设备需通过隔爆型(Ex d)、增安型(Ex e)、本质安全型(Ex i)等防爆型式的结构验证。检测机构通过压力测试、间隙测量和材料分析,确认设备外壳能有效隔绝内部爆炸或阻止外部可燃物进入。例如隔爆型设备需承受1.5倍设计压力的爆炸冲击而不变形。
2. 材料耐腐蚀与抗静电检测
设备外壳材质需进行盐雾试验、湿热试验,评估其在腐蚀性环境中的耐久性。同时检测表面电阻值,确保静电消散能力符合要求(通常表面电阻≤1×10⁹Ω),避免静电积聚引发放电风险。
3. 密封性能测试
采用氦质谱检漏法或水压试验,验证设备接合面、电缆引入装置的密封等级。隔爆型设备的间隙长度与接合面粗糙度需满足IP68防护标准,确保可燃介质无法渗入内部。
4. 温度组别判定
通过热成像仪监测设备运行时表面及内部元件的最高温度,对照T1-T6温度组别标准(T6为最高级别,限制温度≤85℃),确保设备在额定负载下不会成为点火源。
5. 电气参数安全验证
对电路进行火花点燃试验,模拟正常/故障状态下的电气特性。本质安全型设备需通过火花试验装置检测,证明其能量限制水平低于可燃物最小点燃能量(如甲烷为0.28mJ)。
6. 机械强度与抗震测试
依据GB 3836.1进行冲击试验(7J能量冲击)和跌落试验(1m高度自由跌落),验证设备在意外碰撞或运输过程中的结构完整性。同时需通过振动测试(频率10-150Hz,加速度20m/s²)模拟长期运行工况。
7. 防爆标志与文件审查
检查设备铭牌是否完整标注防爆标志(如Ex d IIB T4 Gb)、认证编号及使用限制条件,同时审核技术文件是否包含防爆合格证、安装说明和维护规程。
检测流程与持续管理
检测流程涵盖型式试验、出厂检验和定期复检三阶段。获证设备需每5年进行复检,重点核查结构改动和部件老化情况。企业应建立设备台账管理系统,结合ATEX指令和IECEx认证体系要求,实现全生命周期风险管控。
随着智能传感器和物联网技术的应用,新型在线监测系统可实时采集设备温度、密封参数等数据,结合AI算法预测潜在故障,推动爆炸性环境设备检测向智能化、预防性维护方向发展。
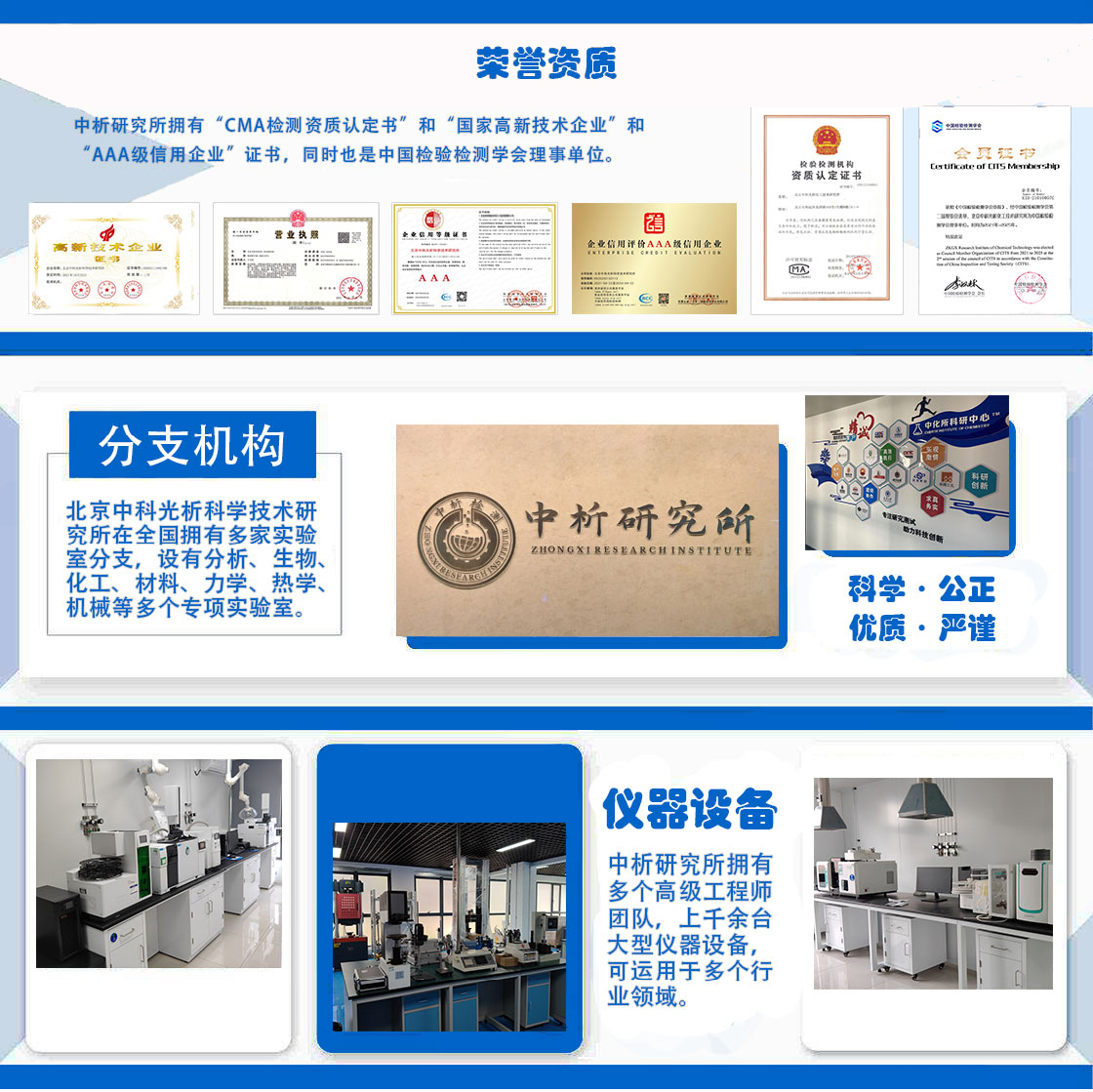
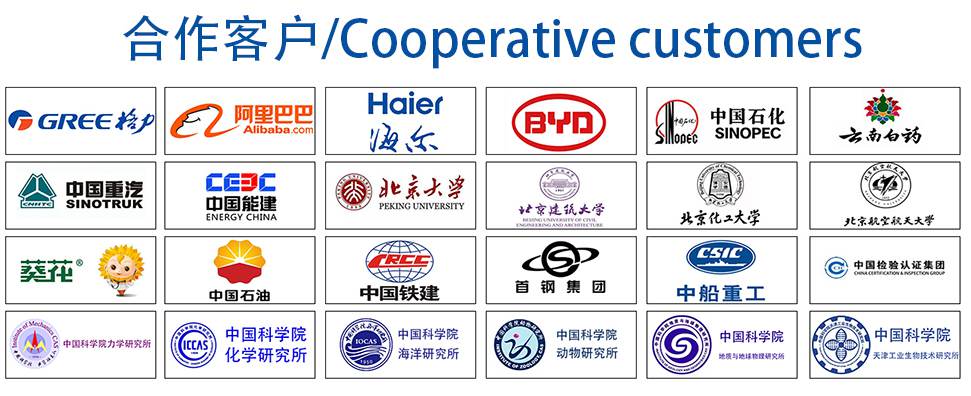