汽车制动气室橡胶隔膜检测的重要性
汽车制动气室橡胶隔膜是气压制动系统的核心部件之一,其性能直接影响制动响应速度、密封性和行车安全。作为制动气室的关键密封元件,橡胶隔膜需在高压、高频率伸缩及复杂工况下长期保持弹性与气密性。若出现老化、裂纹或变形等问题,可能导致制动失效甚至引发严重事故。因此,通过科学系统的检测项目对橡胶隔膜的物理性能、耐介质性、耐久性等进行全面评估,是保障车辆安全运行和符合行业标准(如GB/T 13061、ISO 7637等)的必要环节。
关键检测项目及方法
1. 物理性能检测
包括厚度、硬度、尺寸精度等基础参数的测量。使用游标卡尺、硬度计(邵氏A型)等工具,验证隔膜是否符合设计公差要求。例如,厚度不均匀可能导致局部应力集中,加速疲劳损坏。
2. 耐介质性能测试
模拟橡胶隔膜接触制动液、润滑油及腐蚀性介质的工况。将样品浸泡于标准试液(如DOT3/DOT4制动液)中72小时以上,检测其体积变化率、硬度变化及表面溶胀情况,确保材料抗渗透性和化学稳定性。
3. 耐老化与耐温性能
通过高温老化试验(如100℃×72h)和低温脆性试验(-40℃×24h),评估材料在极端温度下的性能衰减。同时进行臭氧老化测试(50pphm浓度,20%伸长率),观察是否产生龟裂,验证抗环境氧化能力。
4. 力学性能测试
采用拉力试验机检测拉伸强度、断裂伸长率及永久变形率,要求拉伸强度≥15MPa,断裂伸长率≥300%。动态疲劳测试需模拟实际工作频率(通常200-500次/分钟),进行至少50万次循环试验,记录裂纹扩展情况。
5. 密封性与爆破压力测试
在专用气密性检测台上,对隔膜施加1.2MPa工作压力并保压3分钟,检测泄漏量。爆破压力测试则逐步加压至3倍额定压力,确保隔膜无破裂或异常变形。
6. 微观结构分析
使用电子显微镜观察橡胶断面形貌,评估填料分散性及硫化均匀度。红外光谱(FTIR)分析可检测材料成分是否发生降解,辅助判断失效机理。
检测标准与质量控制
需严格执行QC/T 311、SAE J1407等行业标准,结合企业内控指标建立全生命周期质量档案。建议定期对供应商原材料进行溯源检测,并通过台架试验验证实际装车性能。采用非破坏性检测技术(如X射线成像)可提升检测效率,降低质量风险。
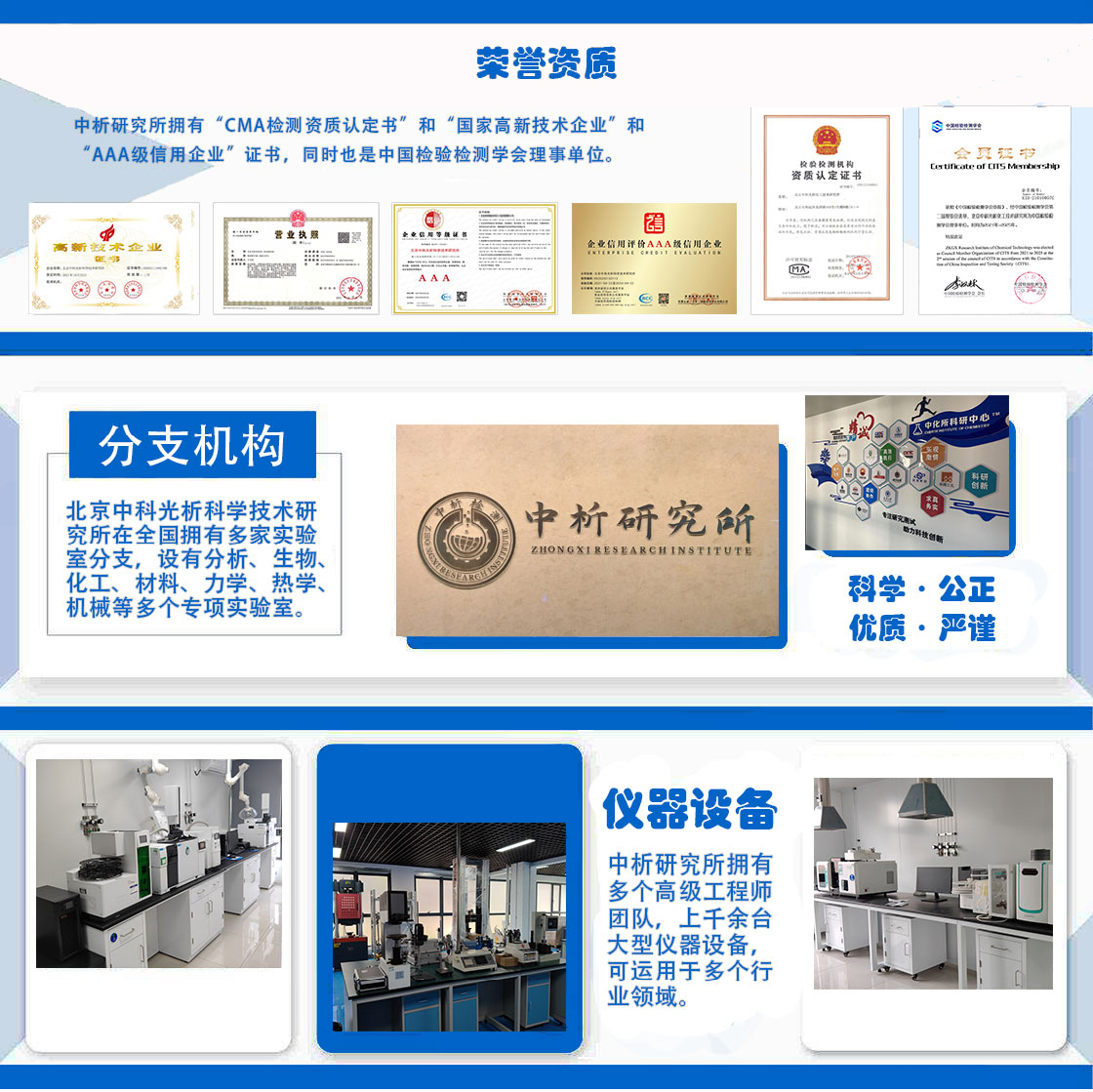
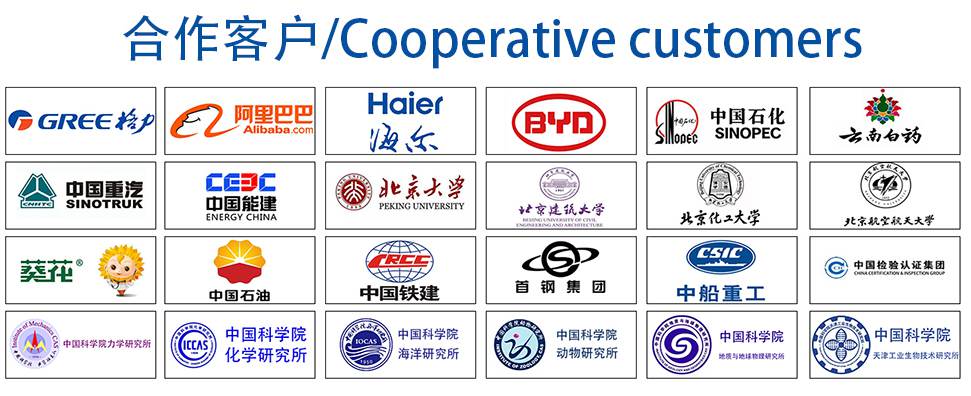