油管和套管内涂层检测的重要性
在石油和天然气开采行业中,油管和套管是确保井筒完整性和油气输送安全的核心设备。由于长期处于高温、高压及腐蚀性介质环境中,其内壁涂层的性能直接影响设备寿命和生产效率。内涂层的主要功能包括防腐蚀、减少流体摩擦阻力、防止结垢以及提升管材表面光洁度。然而,涂层在安装、使用过程中可能因机械损伤、化学侵蚀或工艺缺陷出现剥落、针孔或厚度不均等问题。因此,定期的内涂层检测是保障油气井安全运行、降低维护成本的关键环节。
涂层检测的主要项目
1. 涂层厚度检测
涂层厚度是评价防护性能的基础指标。通过超声波测厚仪或磁感应测厚仪,可非破坏性地测量涂层的平均厚度及均匀性。检测时需根据API RP 5L2或ISO 21809标准,确保涂层厚度符合设计规范(通常要求误差在±20%以内)。对于局部过薄或过厚区域需重点分析,避免形成腐蚀薄弱点。
2. 附着力测试
涂层与基体的结合强度直接影响其抗剥离能力。采用划格法(ASTM D3359)或拉开法(ISO 4624)进行附着力测试,通过专用刀具在涂层表面划出网格或用粘接剂拉拔,观察涂层剥落情况。合格涂层应达到1级(划格法)或≥5MPa(拉开法),否则需重新喷涂或修补。
3. 针孔与孔隙率检测
针孔是涂层连续性缺陷的重要体现,可通过高压电火花检测仪(依据NACE SP0188标准)或湿海绵法识别。检测时施加5-30kV电压或润湿表面,漏电信号或气泡产生位置即为缺陷点。孔隙率则通过氯化钠溶液浸泡试验(ASTM B117)评估涂层抗渗透能力。
4. 耐化学性与硬度测试
模拟井下环境开展耐酸、耐碱及耐盐雾测试(如ISO 9227),观察涂层在特定介质中浸泡后的形貌变化。硬度检测采用铅笔硬度法(ASTM D3363)或邵氏硬度计,确保涂层具备足够的机械强度以避免运输或作业中的磨损。
5. 热稳定性与外观检查
通过循环热冲击试验(如-30°C至150°C交替)验证涂层抗热应力性能,同时采用高清内窥镜或管道爬行器(PIG)对涂层表面进行全周向目视检查,排查鼓包、裂纹或颜色异常等问题。
检测技术的创新趋势
随着智能化技术的发展,电磁超声检测(EMAT)和相控阵超声波技术(PAUT)逐步应用于涂层缺陷的三维成像。此外,基于AI算法的自动缺陷识别系统可提升检测效率,而纳米涂层材料的使用则对检测设备的精度提出更高要求。未来,结合在线监测与大数据分析的涂层健康管理系统将成为行业重点发展方向。
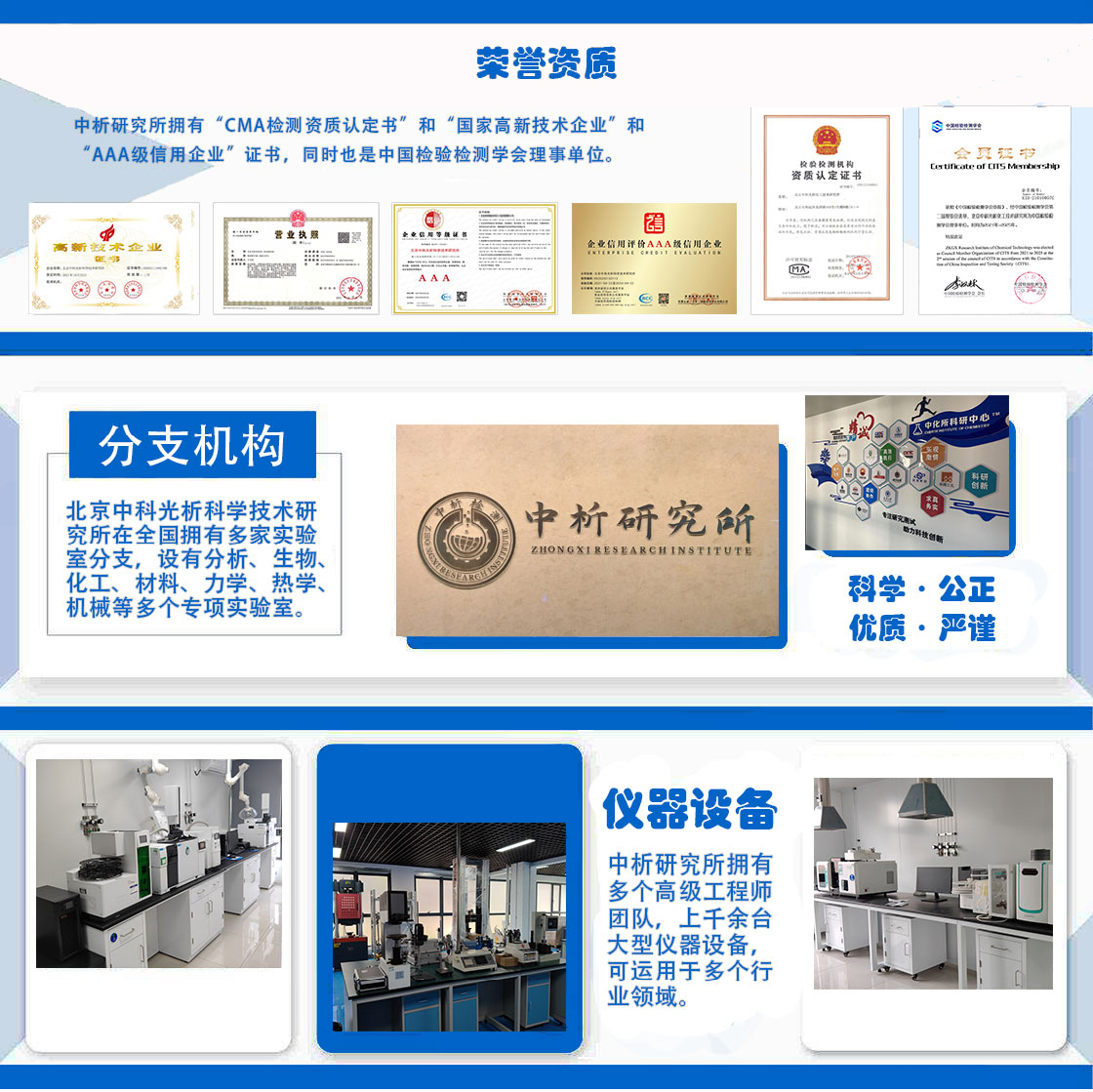
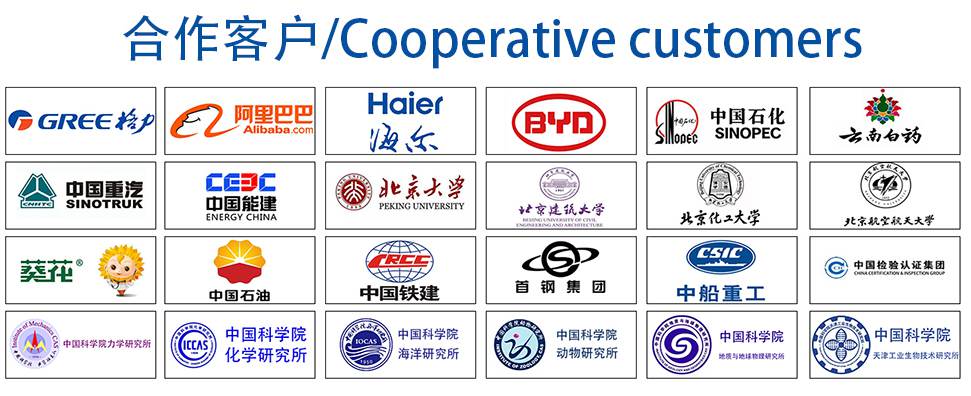