制造安装质量检测的重要性与实施要点
在工业生产和建筑工程领域,制造安装质量检测是保障设备安全运行、延长使用寿命的核心环节。随着现代制造业对精度和可靠性要求的不断提升,检测范围已从传统的目视检查扩展至材料性能分析、工艺参数监控、安装精度验证等系统性工程。通过科学规范的检测流程,企业可有效规避因制造缺陷或安装偏差引发的安全隐患,同时降低后期运维成本,提升项目整体效益。
关键检测项目解析
1. 原材料及配件质量检验
针对钢材、焊接材料、紧固件等关键原料,需进行化学成分分析、力学性能试验(如拉伸、冲击测试)及金相组织检测。例如压力容器制造需符合GB/T 150标准,对钢板进行-20℃低温冲击韧性验证。
2. 制造工艺过程监控
包括焊接工艺评定(按NB/T 47014执行)、无损检测(UT/RT/MT/PT)、热处理曲线验证等。重点检查焊缝熔深、气孔率及残余应力分布,确保制造阶段工艺参数符合设计规范。
3. 安装精度专项检测
设备就位后需执行水平度、垂直度、同心度测量(精度达0.02mm/m),管道系统进行激光对中检测。动设备安装需完成轴对中校验,静态偏差≤0.05mm,动态跑偏量控制在0.1mm以内。
4. 功能性测试验证
包括压力试验(1.5倍设计压力保压30分钟)、密封性检测(氦检漏或气泡法)、设备空载/负载试运行(连续72小时监测振动、温升等参数)。电气系统需完成绝缘电阻(≥500MΩ)、接地电阻(≤4Ω)等专项测试。
5. 文件与标识完整性审核
核查材料质量证明书(MTC)、无损检测报告、压力试验记录等文件的完整性和可追溯性。设备铭牌信息应符合TSG 21法规要求,包含最大工作压力、设计温度等关键参数。
常见问题与解决方案
Q1:如何确定检测项目的实施频次?
A:依据设备风险等级制定检测计划,关键承压部件建议实施100%检测,普通结构件按10%比例抽检。
Q2:现场检测设备如何选型?
A:优先选用具备CMA/ 认证的仪器,如数字超声波探伤仪需满足JB/T 10061标准,测厚仪精度应达±0.1mm。
Q3:发现质量缺陷后的处理流程?
A:建立三级响应机制——轻微缺陷记录备案、中度缺陷限期整改、严重缺陷启动质量回溯程序并重新进行工艺评定。
通过建立覆盖全生命周期的质量检测体系,企业可实现从原材料到成品安装的全流程质量管控,为项目安全运行提供坚实保障。
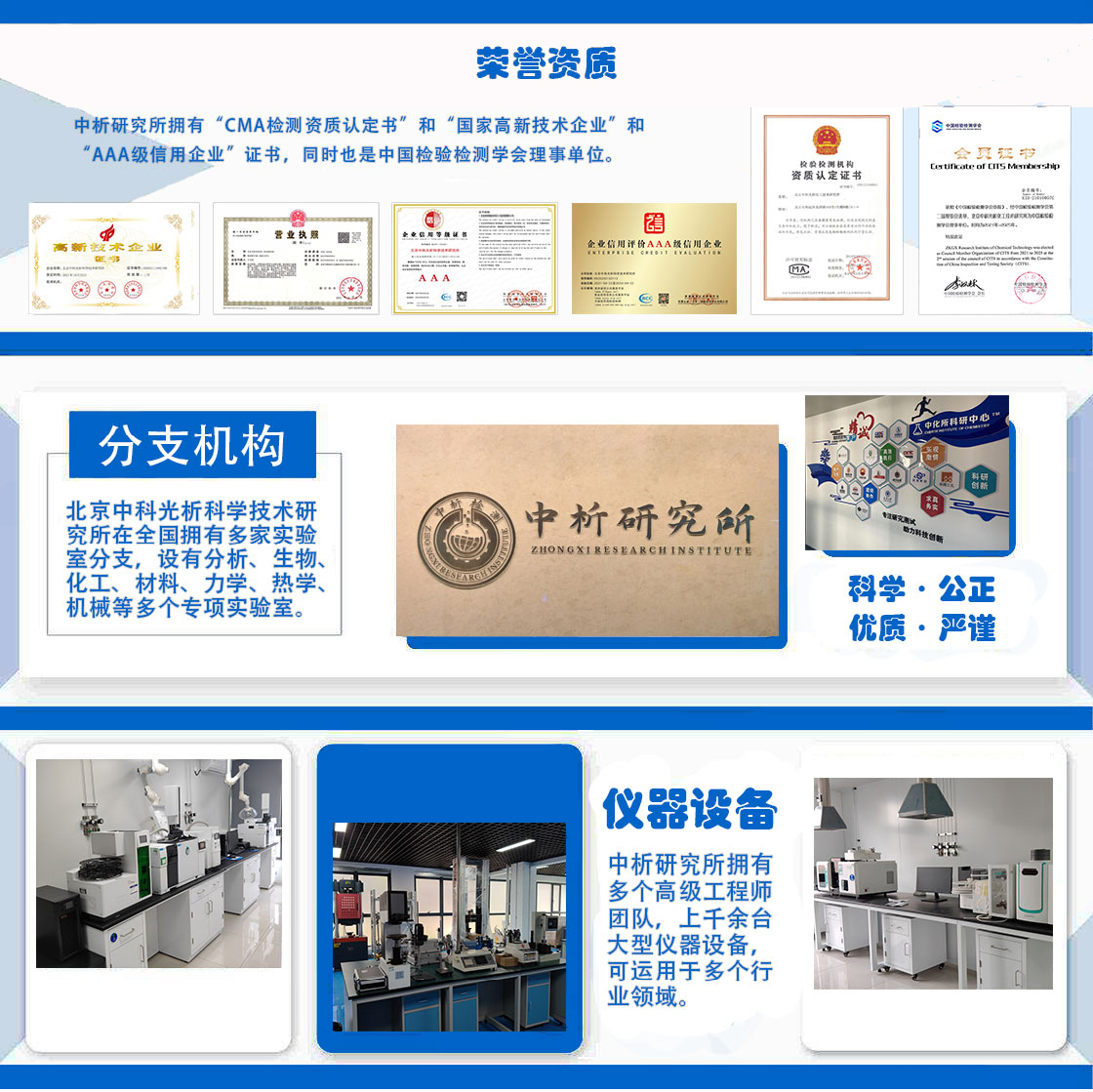
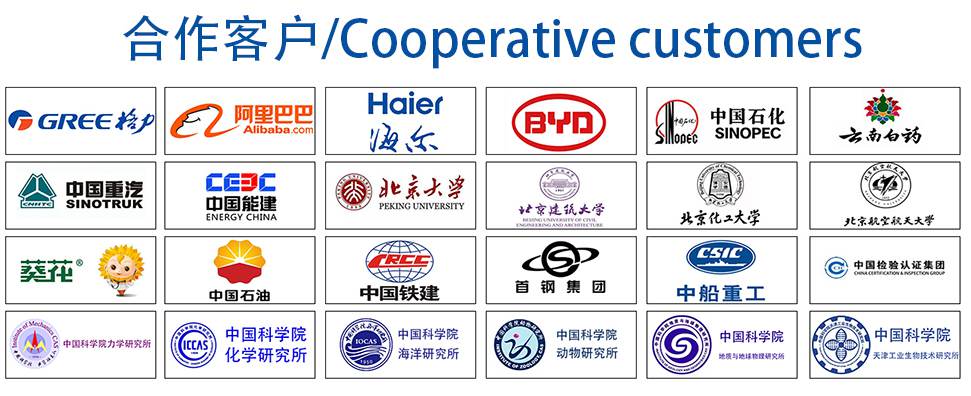