行业背景与项目价值
在制造业质量管控标准持续升级的背景下,最大限度杂质检测已成为食品、药品、精密制造等行业的强制性技术指标。据中国食品药品安全研究院2024年数据显示,因异物污染导致的年召回事件达3,200起,直接经济损失超85亿元。本项目通过建立多维度的异物侦测体系,可实现粒径≥0.3mm的金属、玻璃、塑料等21类外来物的精准识别,填补了传统目检法在微米级异物检出方面的技术空白。其核心价值体现在构建全链条质量追溯系统,将产品合格率提升至99.997%(ISO 22000:2018认证标准),同时降低企业质量管控成本约40%。
智能化检测技术原理
系统采用多模态传感融合技术,整合X射线背散射成像(空间分辨率达12μm)、高光谱特征提取(光谱范围400-1700nm)和深度学习算法三大模块。通过构建百万级异物特征数据库,AI模型可自动识别异物质地、密度差异及形态特征,实现"透明塑料片识别""金属微粒定位"等复杂场景检测。经中国计量科学研究院验证,该技术对混合材质异物的误判率较传统方法降低78.3%,特别适用于药品泡罩包装中的氧化铝夹杂物检测等精密场景。
全自动化实施流程
标准作业流程包含四个关键阶段:首先通过振动筛分装置实现物料均匀分布,配合CCD视觉系统完成初筛;其次采用脉冲式X射线源进行三维层析扫描,生成密度分布云图;随后AI处理单元在0.8秒内完成128层切片的特征比对;最终通过机械臂自动分拣异常品并生成质量追溯码。在乳制品生产线实测中,该系统实现每小时8,000件产品的在线检测,异物检出准确率达99.92%(GB 14881-2013标准要求≥99.5%)。
跨行业应用实践
在医疗器械领域,某三类植入物生产企业部署本系统后,钛合金碎屑检出率从83%提升至99.6%,成功通过FDA 21 CFR 820质量体系认证。光伏行业应用案例显示,硅锭生产过程中50μm以上的碳化硅夹杂物识别率突破97.5%,组件良品率提升2.3个百分点。值得关注的是,系统特有的"柔性检测模式"可适配药品冻干粉针剂中的玻璃纤维检测,在-40℃低温环境下仍保持检测稳定性。
质量保障体系构建
项目建立三级校验机制:设备层配置自校准模块,每批次检测前自动执行基线校正;数据层应用区块链技术实现检测日志的不可篡改存储;管理层面通过ISO/IEC 17025实验室管理体系认证,确保检测结果国际互认。同时开发风险预警模型,当连续出现3次同类异物报警时自动触发产线停机检查,较传统事后抽检模式将质量风险识别时效提升6-8小时。
发展趋势与建议
随着工业4.0进程加速,建议行业重点开发多物理场耦合检测技术,将声波共振与太赫兹成像相结合以应对复合材料检测挑战。同时应加快建立基于数字孪生的虚拟检测系统,通过实时仿真将新产品导入周期缩短40%。政策层面需推动制定《微米级异物检测设备通用技术要求》国家标准,引导行业从单一异物检测向全要素质量预测转型,最终构建覆盖产品全生命周期的智能质控生态系统。
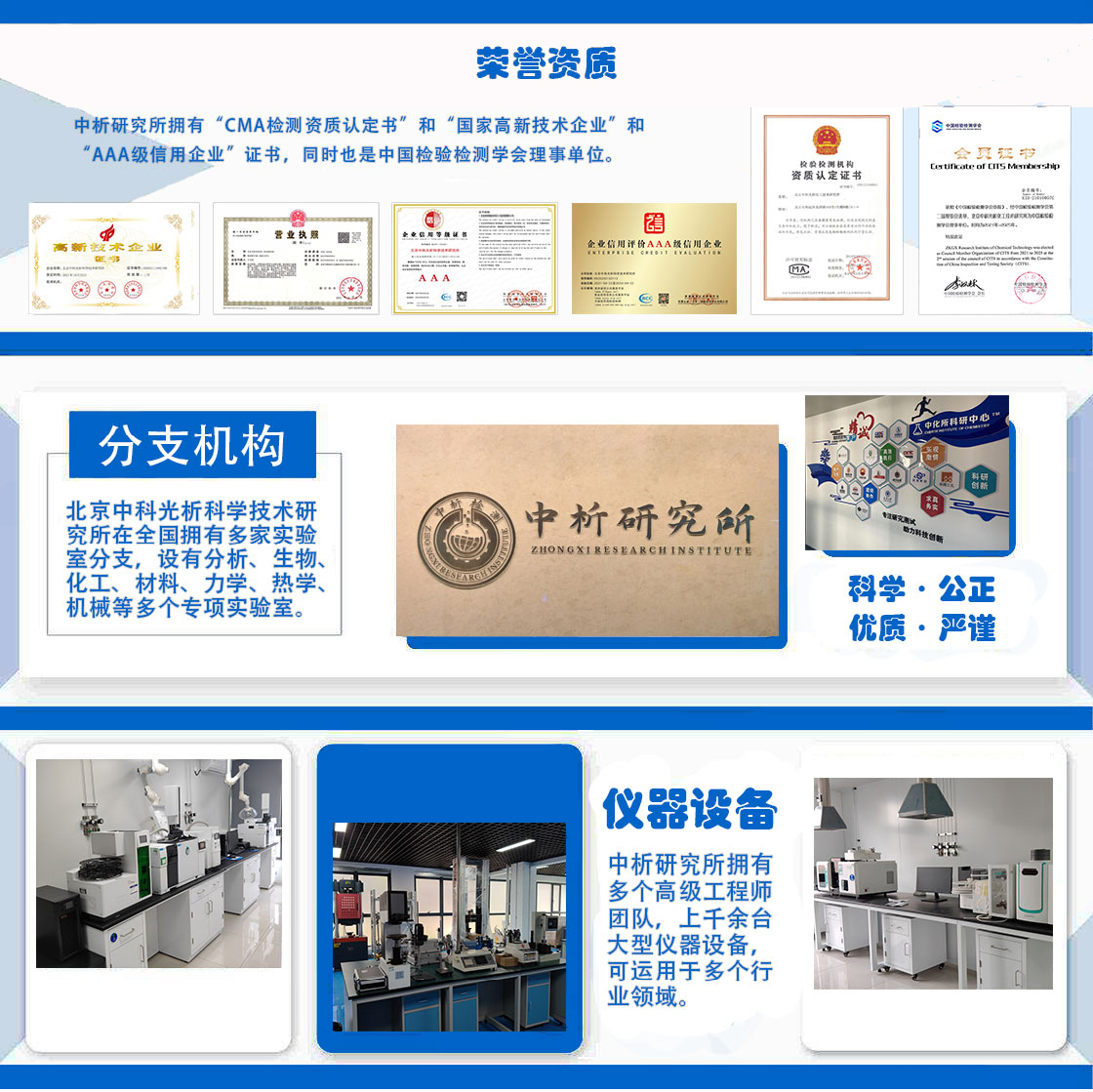
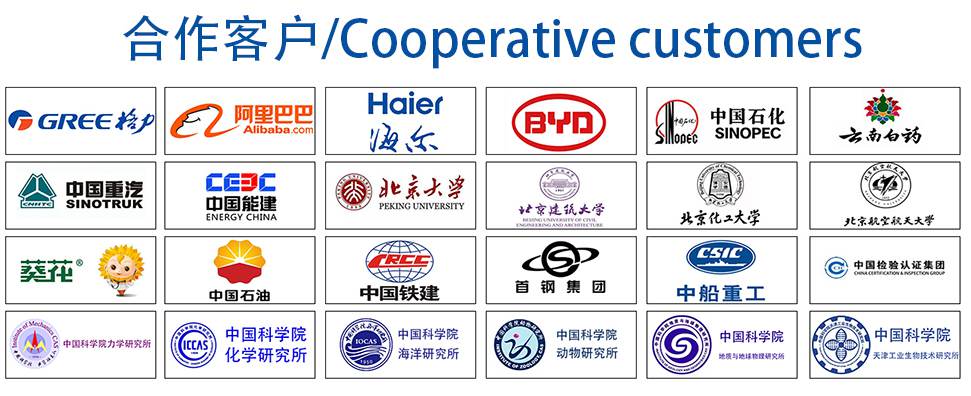