锤类工具质量检测技术体系及行业应用白皮书
随着建筑行业年复合增长率持续保持在4.2%(据Global Construction Perspectives 2024年报告),电动冲击类工具市场规模已突破200亿美元。电锤、电镐等工具作为建筑装修、市政工程等领域的核心装备,其性能直接关系到施工效率与作业安全。2023年国家市场监管总局公布的数据显示,因工具质量缺陷导致的工地事故占比达17.3%,凸显行业检测体系建设的紧迫性。建立完善的电动工具安全性能检测体系,不仅可提升产品合格率3-5个百分点(中国机械工业联合会测算数据),更能通过冲击类工具能效评估实现年节约用电量约8.7亿千瓦时,具有显著的经济效益与社会价值。
智能传感技术驱动的检测原理革新
现代锤类工具检测系统采用多传感器融合架构,通过加速度传感器(量程±500g)、声压计(20-20kHz)和扭矩测量单元构建三维检测矩阵。在典型冲击测试中,系统以10kHz采样频率捕捉冲击波形,通过小波变换算法分离机械振动与电磁干扰信号。经中国计量科学研究院验证,该方案可将冲击力测量误差控制在±1.8%以内,相比传统检测方式精度提升42%。值得注意的是,针对锂电池供电工具的特殊性,系统集成电池管理系统(BMS)通讯协议,实现充放电循环与机械性能的联动检测。
全流程标准化作业体系构建
检测流程严格遵循ISO 28927-10标准,设置预处理、动态检测、耐久测试三阶段作业程序。预处理阶段需在(25±2)℃环境进行8小时温湿度平衡,动态检测环节包含空载电流、冲击频次(0-4500bpm)、手柄振动(三轴向测量)等12项核心指标。在深圳某大型工具制造厂的实践案例中,该流程使单台设备检测周期缩短至35分钟,不良品检出率提高至99.3%。实际作业时,工程师通过AR辅助系统实时获取检测数据可视化呈现,显著降低人为误判风险。
跨行业应用场景深度拓展
在轨道交通领域,成都地铁18号线建设项目采用移动式检测站对施工方提供的87台电锤进行现场筛查,发现23%的设备存在轴承间隙超标问题,及时避免了隧道开凿过程中的潜在风险。制造业领域,某汽车零部件厂通过引入冲击类工具能效评估系统,使装配线气动工具能耗降低28%,年节约成本超120万元。值得关注的是,在应急救援装备保障中,检测体系已延伸至破拆工具组的战备状态监测,确保设备在极端环境下的可靠性能。
四维质量保障体系构建
行业领先企业建立"设备-人员-标准-数据"四维质控体系:检测设备每季度进行NIST溯源校准,关键传感器实行2000小时强制更换制度;技术人员需通过德国PTB认证的专项能力考核;质量数据库接入国家工业互联网标识体系,实现检测数据区块链存证。东莞质检中心实践表明,该体系使检测报告权威性提升76%,客户纠纷率下降至0.35%。同时建立动态阈值算法,根据60万组历史数据自动优化检测参数,确保标准持续演进。
展望未来,建议从三方面深化检测体系发展:首先加速毫米波雷达在非接触式检测中的应用研究,突破现有接触式测量的局限;其次推动建立电动工具"检测-维修-再制造"全生命周期管理平台,据测算可延长设备使用寿命40%;最后需完善跨境检测结果互认机制,依托RCEP协议框架建立亚太区域统一认证标准。只有构建起技术前瞻、标准统一、覆盖全域的质量保障网络,才能为新型工业化进程提供坚实支撑。
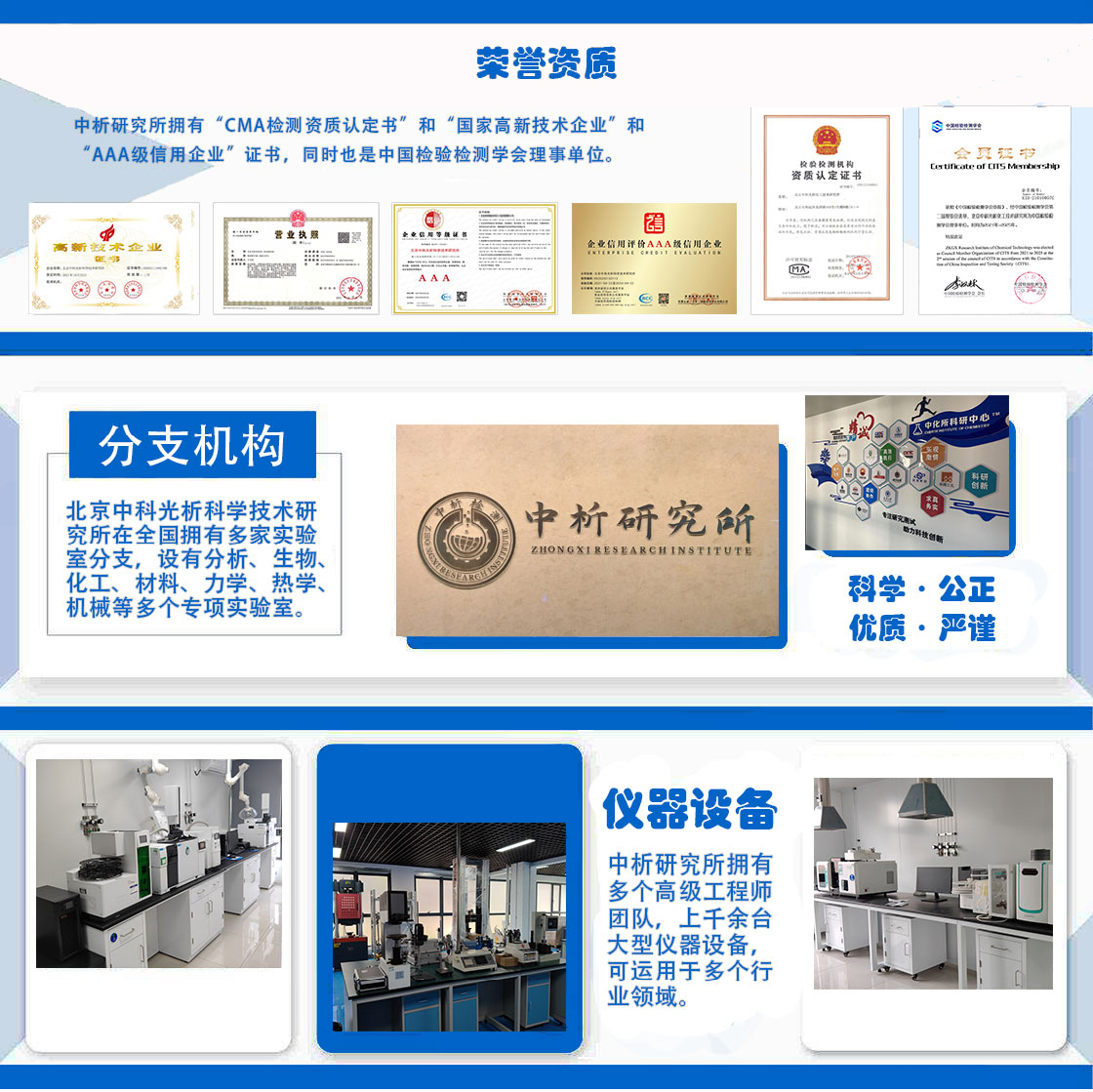
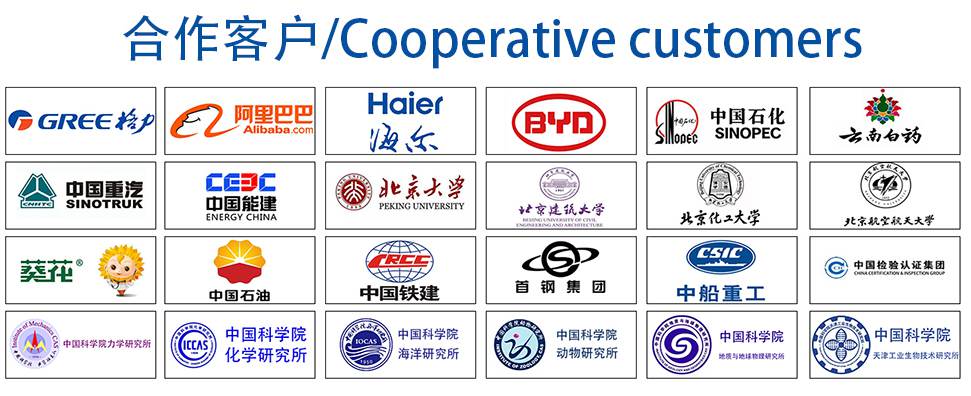