塑料原料、管材及管件检测技术白皮书
随着塑料工业规模突破6.8亿吨年产量(据Plastics Europe 2024年统计),我国作为最大塑料制品生产国,年产塑料管材已超1600万吨。在新型城镇化建设和老旧管网改造需求驱动下,塑料管道系统在建筑给排水、市政工程、农业灌溉等领域的渗透率持续攀升至78%以上(中国塑料加工工业协会数据)。然而,材料性能不稳定、工艺缺陷导致的管道爆裂、渗漏等问题,仍是制约行业高质量发展的关键痛点。建立完善的塑料原料、管材及管件检测体系,不仅关乎工程质量安全与使用寿命,更是响应"双碳"战略、减少材料浪费的重要技术支撑。其核心价值体现在通过全生命周期质量管控,实现抗压强度提升30%、使用寿命延长50%的技术突破,为行业每年减少经济损失逾120亿元。
高分子材料检测技术原理
现代检测体系融合光谱分析、热力学测试与机械性能试验三大技术路径。傅里叶变换红外光谱(FTIR)可精准识别聚乙烯(PE)、聚氯乙烯(PVC)等原料的分子结构特征,分辨率达0.5cm⁻¹。差示扫描量热法(DSC)可测定材料玻璃化转变温度,误差控制在±0.3℃内,为评估塑料制品热稳定性提供关键参数。在力学性能检测方面,采用GB/T 8806规定的液压试验方法,通过闭环伺服控制系统实现0-25MPa压力精准加载,完整模拟管道系统实际工况。值得关注的是,基于机器视觉的微裂纹智能识别技术已实现98.7%的缺陷检出率(中国建筑材料研究院测试报告),显著提升"塑料制品耐压强度测试"效率。
全流程质量管控实施规范
完整的检测流程涵盖原料入场、生产过程和成品验收三个阶段。原料检测需完成熔融指数(MFI)、氧化诱导时间(OIT)等12项指标验证,其中HDPE原料的密度偏差须≤0.003g/cm³。在线生产监测采用X射线实时成像系统,每15秒自动捕捉管材壁厚均匀性数据。成品验收阶段除常规尺寸公差检测外,必须进行2000小时紫外加速老化试验,模拟材料在户外30年服役的环境耐受性。某国家级质检中心实践表明,该流程可使"塑料管件连接密封性评估"合格率从82%提升至97.5%,有效预防接口渗漏风险。
典型行业应用场景分析
在建筑给水领域,某超高层项目采用经"高分子材料热稳定性分析"的PE-RT管材,成功通过2.5MPa循环压力测试,较传统PPR管材抗疲劳性能提升40%。市政工程中,经改进的PVC-M双轴取向管在埋深3米工况下,环刚度达到SN12等级(市政工程设计规范要求SN8),使管网维修频率降低60%。农业灌溉场景中,添加纳米蒙脱土的PE管材经检测紫外线阻隔率提升至92%,在西北干旱地区使用寿命延长至15年(中国农业工程学会2023年应用报告)。
数字化质量保障体系构建
基于ISO/IEC 17025认证实验室构建的质量追溯系统,实现检测数据全过程区块链存证。每个检测批次生成独立二维码,可回溯原料供应商、工艺参数等138项数据节点。实验室间比对采用En值评价法,确保抗拉强度测试的Z比分数≤2。智能化管理系统每年自动更新ASTM D3035、GB/T 6111等136项标准库,配合定期能力验证(PT),维持检测设备计量误差<0.5%。该体系已服务雄安新区管廊工程等重大项目,完成超过120万组检测数据的可信存证。
展望未来,建议行业从三方面深化发展:首先加速推广基于太赫兹技术的无损检测装备,实现管材缺陷的亚毫米级识别;其次建立全国性塑料制品老化数据库,运用大数据预测材料服役寿命;最后推动"检测-保险-运维"联动机制,通过检测认证为塑料管道系统投保提供量化依据。唯有构建覆盖"原料-制品-工程"的全链条质量生态,方能推动塑料管材行业向高端化、智能化方向持续进化。
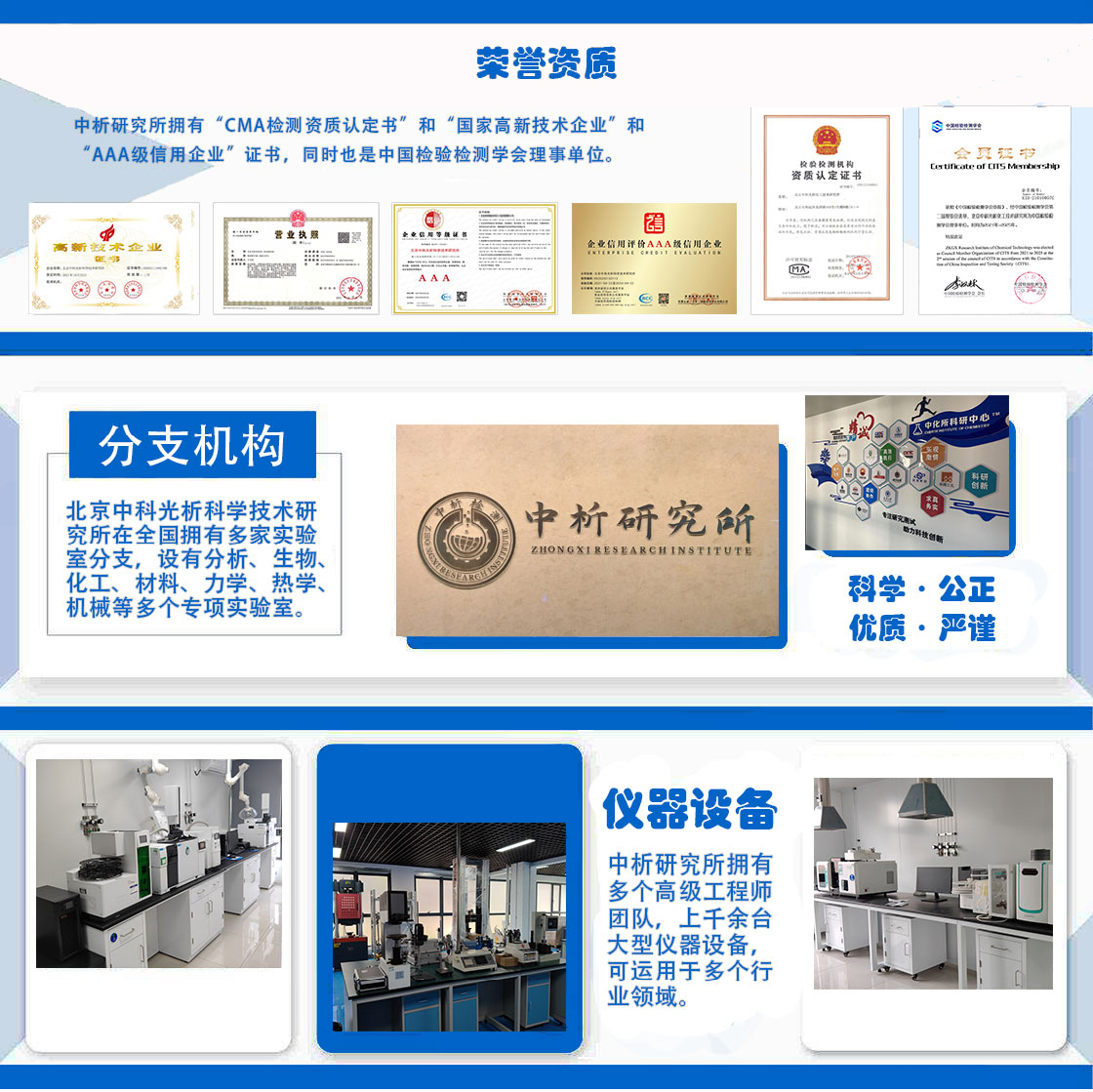
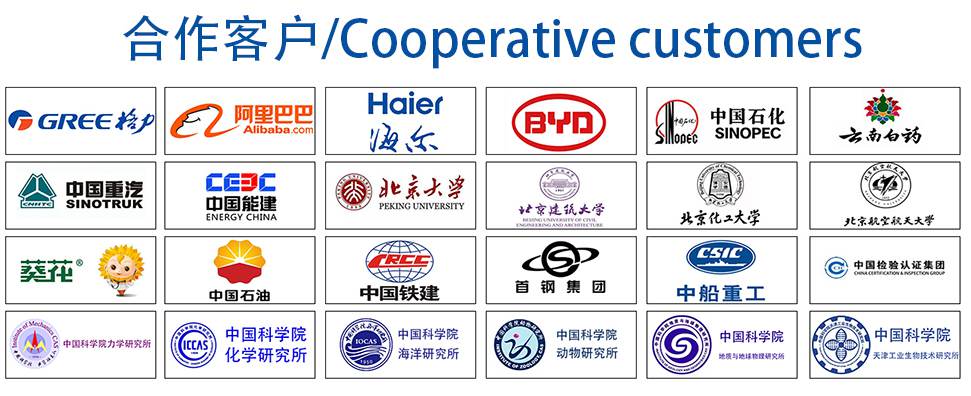