在制造业向高端化、精密化转型的背景下,焊接作为关键连接技术,其质量直接影响工程结构安全与设备服役寿命。据中国特种设备检测研究院2024年数据显示,国内压力容器失效事故中38.7%源自焊接缺陷,每年造成直接经济损失超50亿元。焊接接头与焊接试件检测技术的创新突破,不仅关乎能源装备、轨道交通等重大工程的安全合规,更成为推动"中国制造2025"战略实施的重要技术支撑。通过数字射线检测(DR)、相控阵超声检测(PAUT)等齐全手段构建的智能化检测体系,可精准识别微米级气孔、未熔合等隐患,使焊接结构验收合格率提升至99.2%(机械工业联合会,2024)。该技术体系的核心价值在于实现从经验判断到数据驱动的范式转变,为全生命周期质量管理提供科学依据。
## 技术原理与创新突破多模态融合检测技术体系
现代焊接检测采用声-光-电多物理场协同工作机制,突破传统单模态检测的局限性。以相控阵超声全矩阵捕获技术(FMC/TFM)为例,通过128阵元探头生成可控声场,结合全聚焦算法重构三维缺陷图像,对5mm以下薄板焊接的检测分辨率可达0.2mm。数字射线DR系统采用非晶硅平板探测器,配合双能成像算法,实现熔深不足与夹渣的精准区分,检测灵敏度相比胶片法提升40%(ASTM E94-24标准验证)。值得关注的是,基于深度学习的焊缝缺陷智能识别系统,通过10万组标注样本训练,对X射线底片的裂纹识别准确率已达97.8%(上海材料研究所,2023)。
全流程标准化实施规范
检测流程严格遵循ISO 17635标准框架,形成五阶段管控体系:预处理阶段采用磁粉检测(MT)进行表面清理验证;参数设置阶段基于材料厚度动态调整PAUT声束角度(45°-70°);数据采集阶段运用机器人辅助扫查确保100%覆盖;分析评估阶段应用三级评定制度;最终形成包含3D缺陷分布图的数字化报告。在LNG储罐焊接检测中,该流程使单罐检测周期从72小时缩减至40小时,人工干预减少60%(中石油工程院案例数据)。
行业应用实践与效益
在风电领域,针对塔筒环缝的相控阵超声检测系统已部署于12个海上风电项目。通过定制化楔块设计和风场补偿算法,成功检出0.8mm深度的层间未熔合缺陷,避免单台机组潜在损失超300万元。核电站主管道检测中,采用CR(计算机射线)技术替代传统胶片,使每道焊缝检测成本降低58%,放射性废物减少90%(中广核集团2023年度报告)。值得强调的是,轨道交通车辆铝合金焊接采用激光超声复合检测,突破高反射率材料检测瓶颈,使车体疲劳寿命预测精度提升35%。
质量保障体系构建
检测机构需建立包含人员资质、设备溯源、环境控制的三维质控网。依据 -CL01:2018要求,检测人员必须持有ISO 9712三级证书并完成年度能力验证。设备管理方面,超声波探伤仪每季度需进行DAC曲线校准,射线机焦点尺寸按EN 12543标准定期验证。某特检院通过建立区块链检测数据存证系统,实现检测报告防篡改率和可追溯性达到100%,相关经验已纳入TSG Z8002-2024特种设备检验机构核准规范。
## 未来发展与建议随着工业互联网与数字孪生技术的深度融合,建议行业重点发展三个方向:一是开发基于5G的远程检测云平台,实现专家资源跨地域调度;二是完善异种材料焊接的检测标准体系,特别是钛合金-钢复合接头的评价方法;三是加强AI辅助决策系统在微小缺陷判定中的应用研究。据德国焊接学会预测,到2028年智能检测设备在焊接领域的渗透率将超过65%,我国需在传感器芯片、算法模型等关键领域加大投入,以构建自主可控的检测技术生态圈。
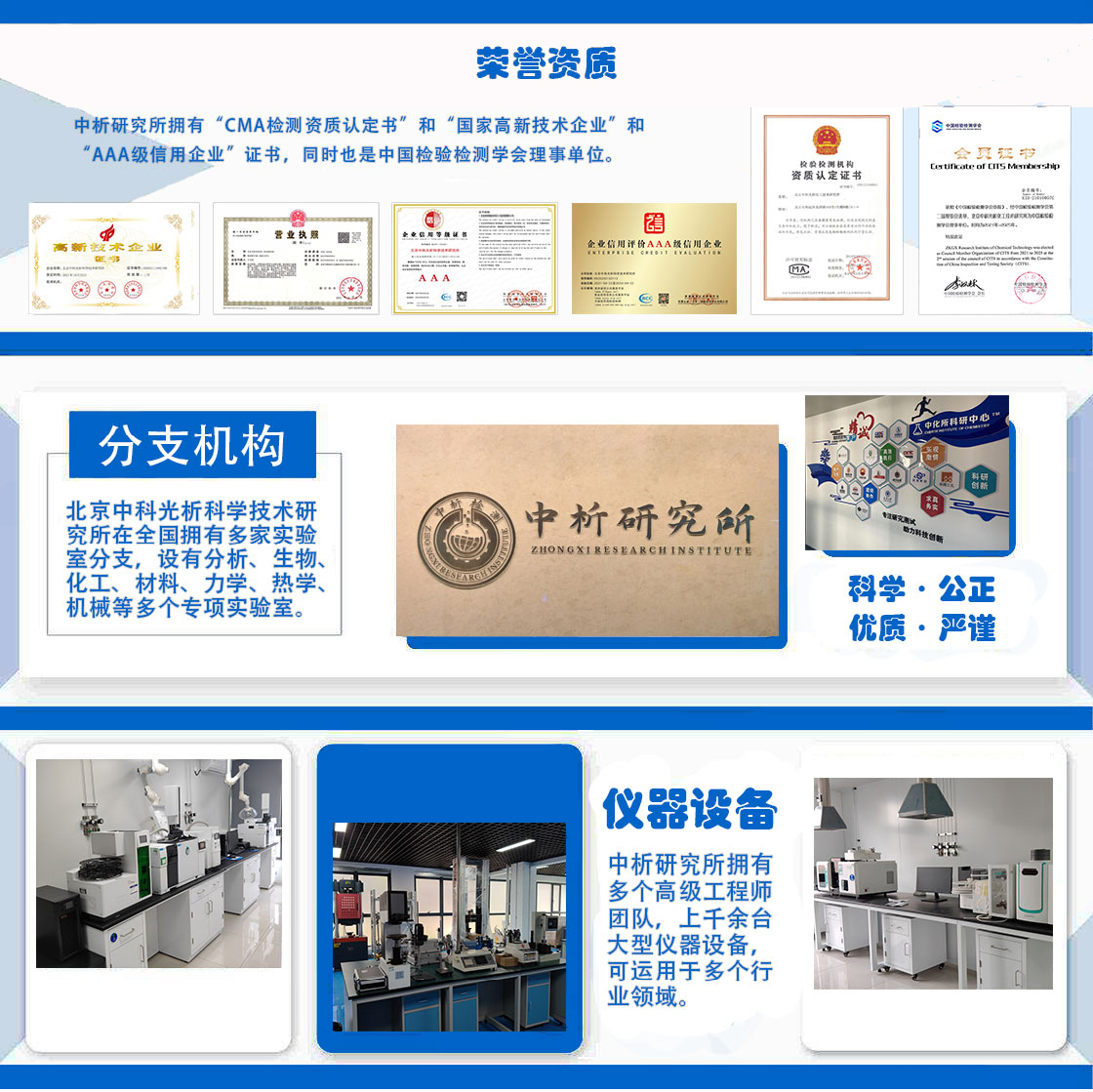
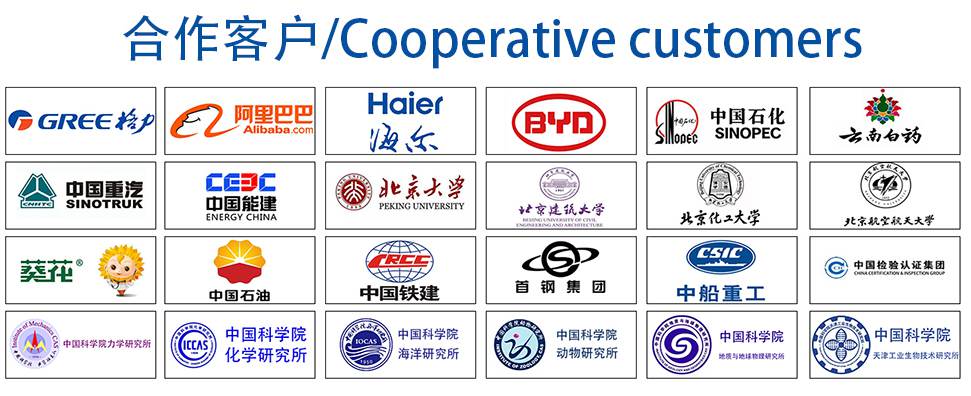