高压管汇检测的重要性与核心内容
高压管汇作为石油、天然气、化工等工业领域的重要输送设备,承担着高压介质的传输任务。其长期处于高温、高压、腐蚀等恶劣工况下,若出现泄漏、裂纹或结构失效等问题,可能导致严重的安全事故、环境污染及经济损失。因此,定期开展高压管汇检测是保障生产安全、延长设备寿命的关键环节。检测过程需结合结构特点、运行环境及行业标准,通过多维度技术手段对管体、焊缝、连接件等部位进行全面评估。
高压管汇核心检测项目解析
1. 外观与几何尺寸检查
通过目视和测量工具检查管汇表面是否存在腐蚀、变形、磨损或机械损伤,重点核查法兰、弯头、三通等关键部位的尺寸是否符合设计要求。同时评估防腐层完整性,确认是否存在剥落或老化现象。
2. 无损检测技术应用
采用超声波检测(UT)探查管壁厚度及内部缺陷,磁粉检测(MT)或渗透检测(PT)用于发现表面裂纹,射线检测(RT)则用于焊缝质量评估。对于复杂结构部位,可结合相控阵超声等齐全技术进行三维缺陷定位。
3. 压力与密封性能测试
执行水压试验或气压试验,验证管汇在1.5倍工作压力下的承压能力,同时通过保压测试检测密封件的有效性。采用氦气检漏仪对阀门、法兰连接处进行微泄漏检测,灵敏度可达10-9 mbar·L/s。
4. 材料性能退化分析
通过金相分析、硬度测试和化学成分检测,评估材料在长期服役后的性能变化,特别是氢致开裂(HIC)和硫化物应力腐蚀(SSCC)风险。对高风险区域取样进行应力腐蚀敏感性试验。
5. 动态工况监测与评估
安装振动传感器监测管汇的振动频率和幅度,分析脉动压力对结构的影响。结合流体动力学模拟,评估冲刷腐蚀对管壁的减薄效应,制定预防性维护策略。
检测周期与标准依据
依据API 6A、ASME B31.3等国际规范,常规检测周期为12-36个月。对于含硫介质或极端工况环境,应缩短至6-12个月。检测数据需建立数字化档案,通过趋势分析实现寿命预测,为设备更新决策提供科学依据。
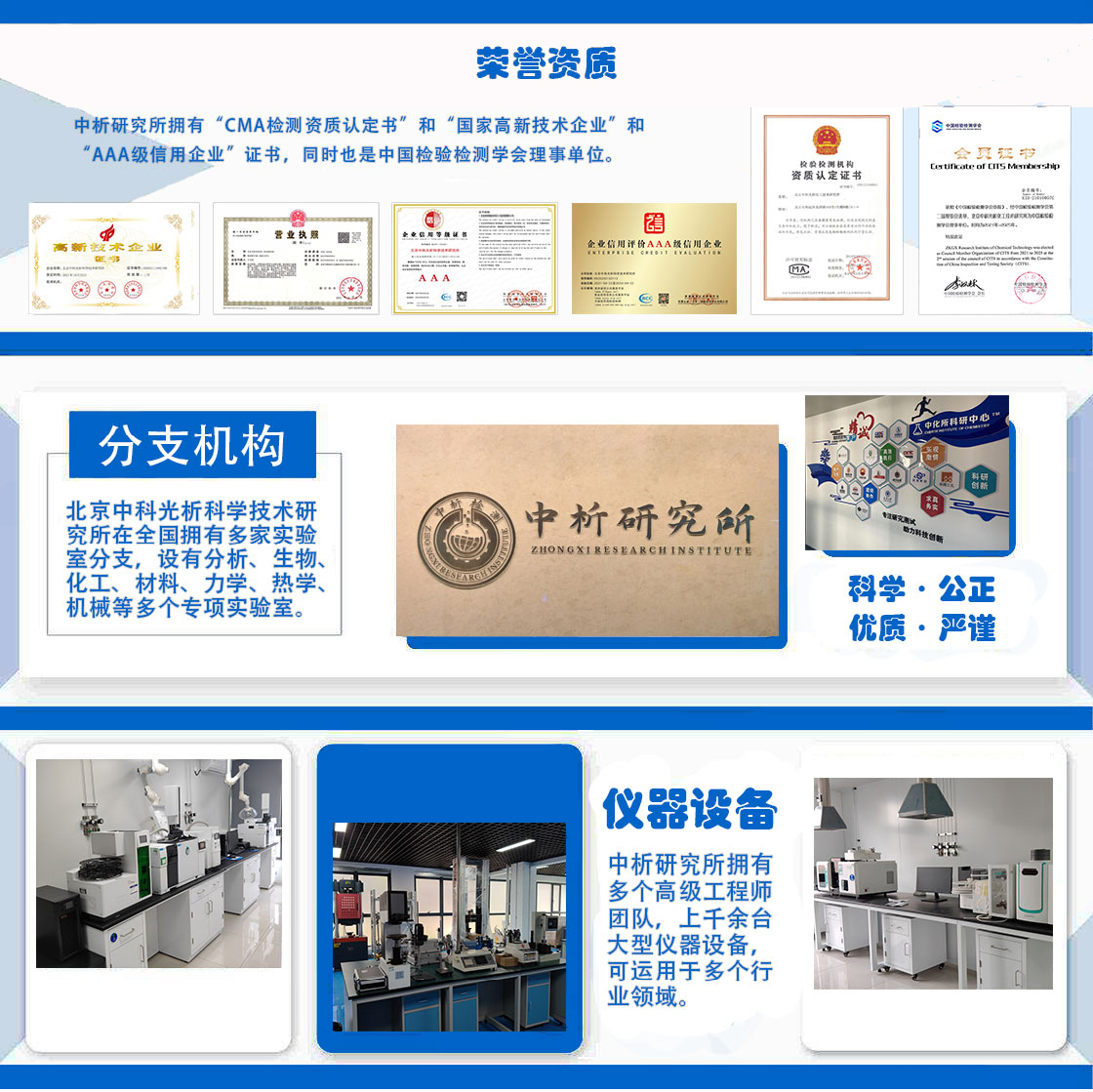
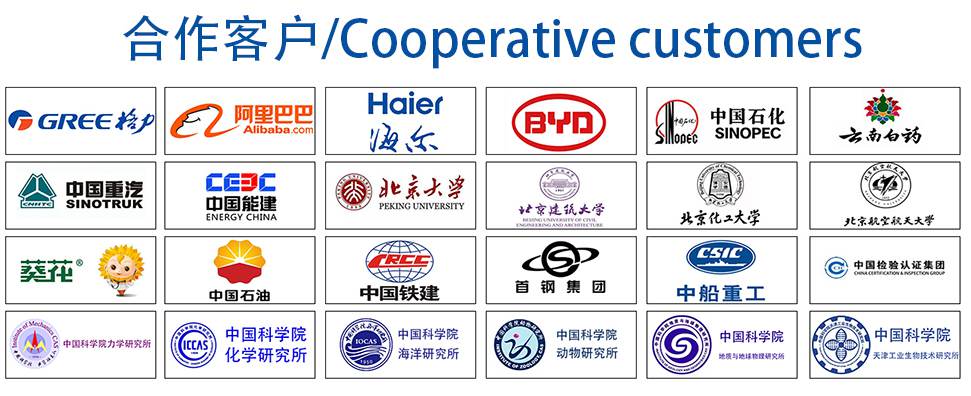