钢质管道液体环氧涂料检测的重要性
钢质管道液体环氧涂料作为管道防腐保护的核心材料,其性能直接影响管道的使用寿命和安全性。在石油、天然气、化工等工业领域,管道长期暴露于潮湿、酸碱、高温或高压等复杂环境中,若涂层存在缺陷或性能不达标,可能导致腐蚀泄漏、环境污染甚至重大事故。因此,开展系统化的检测项目是确保涂料质量、验证施工效果的必要环节。检测内容需覆盖涂料的物理性能、化学稳定性及环境适应性,同时结合行业标准(如ISO 21809、GB/T 23257等)进行科学评估。
关键检测项目及方法
1. 物理性能检测
包括涂层厚度、附着力、硬度及耐磨性测试。使用磁性测厚仪测定干膜厚度是否符合设计要求;通过划格法或拉拔法(ASTM D4541)评估附着力等级;采用铅笔硬度计(GB/T 6739)和耐磨试验机验证涂层的机械强度。
2. 化学耐性检测
模拟实际工况进行耐盐雾(GB/T 1771)、耐酸碱(GB/T 9274)及耐溶剂浸泡试验,检测涂层的抗渗透性和耐化学腐蚀能力。重点关注涂层表面是否出现起泡、剥落或变色现象。
3. 电化学性能测试
通过电化学阻抗谱(EIS)和阴极剥离试验(SY/T 0315),分析涂层对金属基体的保护效果及抗阴极剥离能力,预判长期服役中的失效风险。
4. 环境适应性检测
针对高低温循环(GB/T 1735)、紫外线老化(GB/T 14522)等极端条件,验证涂层的抗开裂性、耐候性及热稳定性,确保其在温差变化或光照下的耐久性。
5. 施工质量验收
包括湿膜厚度控制、表干/实干时间测定及漏点检测(电火花检漏仪)。重点排查针孔、流挂等施工缺陷,保障涂层的连续性和完整性。
检测结果分析与标准化要求
所有检测数据需对照国家标准或工程合同指标进行合格性判定。例如,附着力需达到1级(划格法)或≥5MPa(拉拔法),阴极剥离半径应≤8mm(28天试验)。检测报告应明确标注不合格项并提出改进建议,为涂层修复或工艺优化提供依据。
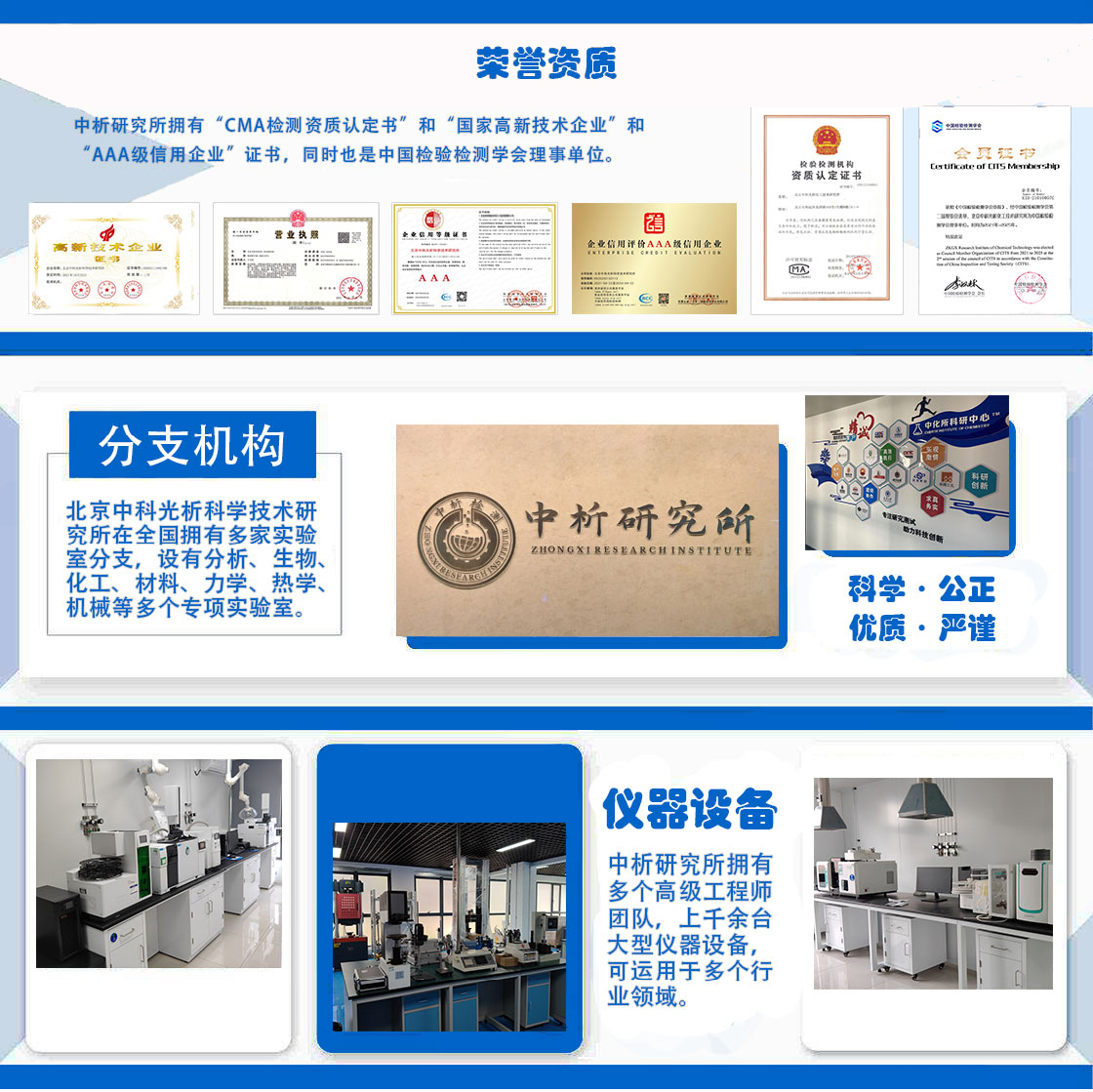
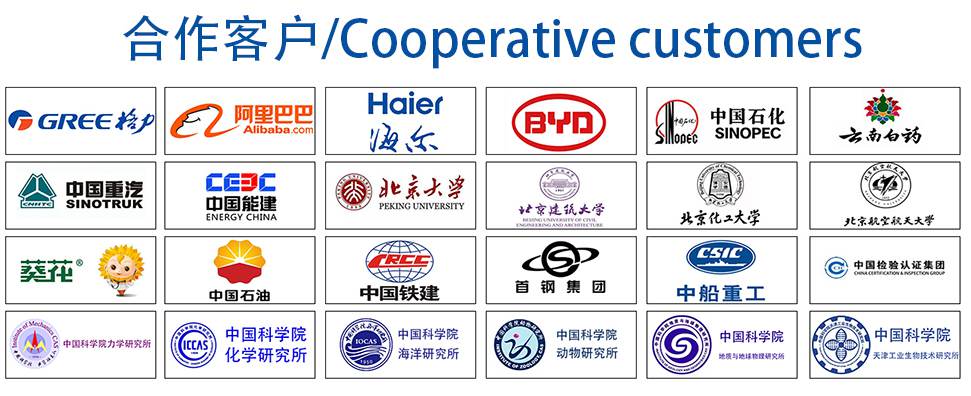