油气输送用钢制感应加热弯管检测的重要性
在油气长输管道工程中,钢制感应加热弯管作为管道转向的核心组件,承担着输送介质转向、补偿位移及适应地形变化的重要作用。其质量直接关系到管道的安全运行和使用寿命。由于弯管在制造过程中需经历高温加热、塑性成形及冷却工艺,可能产生材料性能劣化、几何缺陷或残余应力等问题。因此,针对油气输送用钢制感应加热弯管的检测项目需涵盖材料性能、工艺质量及安全可靠性等多维度指标,以确保其满足API 5L、GB/T 29168等国内外标准要求。
关键检测项目及方法
1. 材料性能检测
包括化学成分分析(光谱检测法)、拉伸试验(屈服强度、抗拉强度)、冲击韧性测试(夏比V型缺口试验)及硬度检测(布氏/洛氏硬度计),重点关注加热区域与母材的性能一致性,确保弯管在高压、低温等工况下的力学稳定性。
2. 工艺质量检测
通过三维激光扫描或专用量具对弯管尺寸公差(弯曲半径、椭圆度、壁厚减薄率)进行精确测量,同时检验表面裂纹、褶皱等缺陷。弯曲角度偏差需控制在±0.5°以内,过渡区曲率半径应符合设计要求。
3. 无损检测(NDT)
采用超声波检测(UT)排查内部夹杂、分层缺陷;射线检测(RT)验证焊缝质量;磁粉检测(MT)和渗透检测(PT)用于表面及近表面裂纹筛查。重点检测加热区、背弧减薄区等高风险部位。
4. 防腐层检测
对环氧涂层或3PE防腐层进行厚度测量(磁性测厚仪)、附着力测试(划格法)及耐阴极剥离试验,确保防腐体系在土壤应力、湿度变化等环境下的完整性。
5. 型式试验与出厂检验
包括水压试验(1.5倍设计压力保压)、疲劳试验(模拟交变应力)及金相组织分析(观察奥氏体晶粒度变化)。出厂前需逐件进行外观检查、尺寸复核及硬度抽检,并出具符合ASME B16.49的检测报告。
检测技术的发展趋势
随着智能管道建设的推进,数字射线成像(DR)、相控阵超声波检测(PAUT)等齐全技术逐步应用,结合大数据分析可实现缺陷的智能判读。同时,残余应力测定(X射线衍射法)和应力腐蚀试验(慢应变速率试验)等专项检测,为高钢级弯管的性能评估提供更全面支撑。
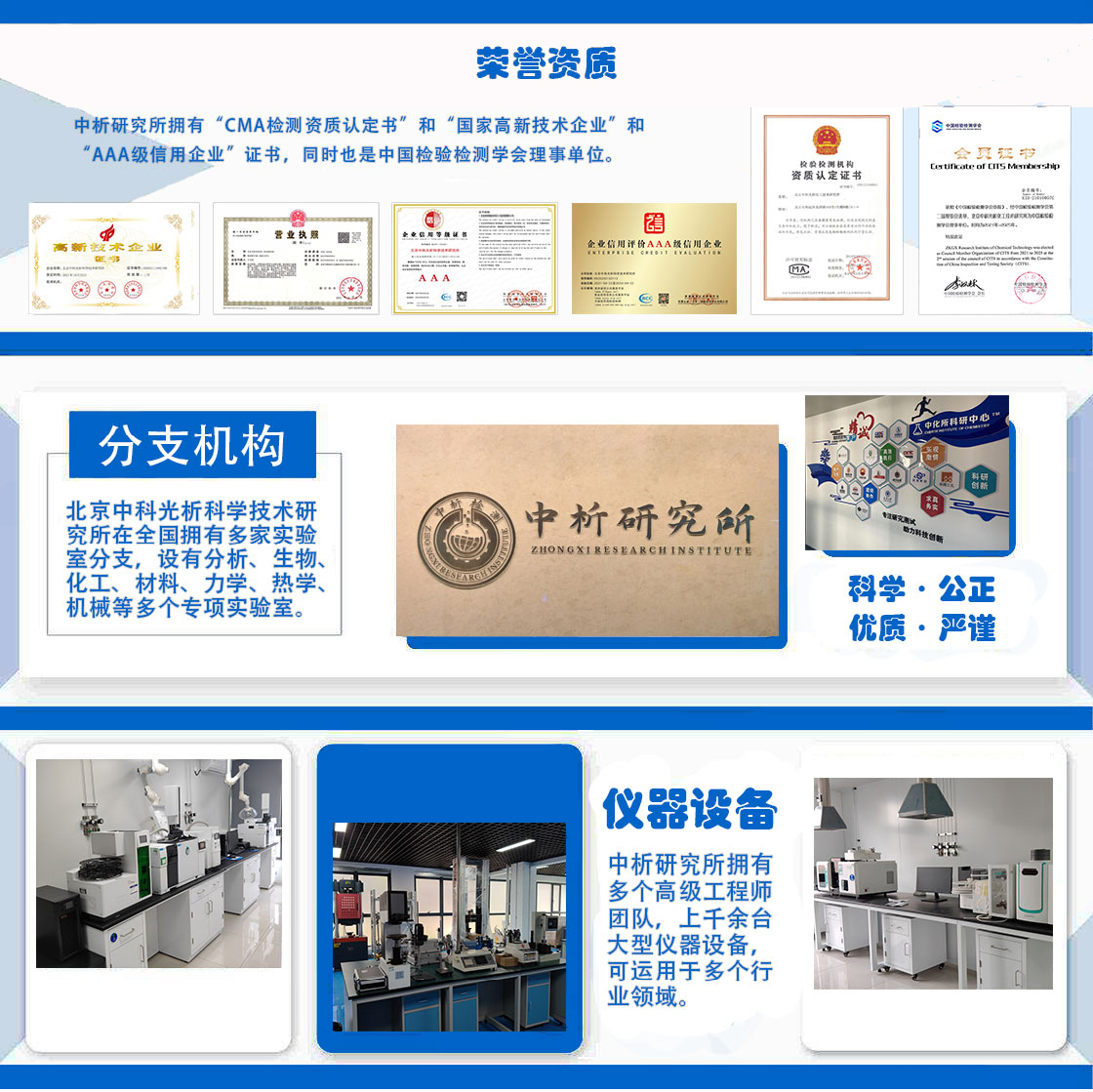
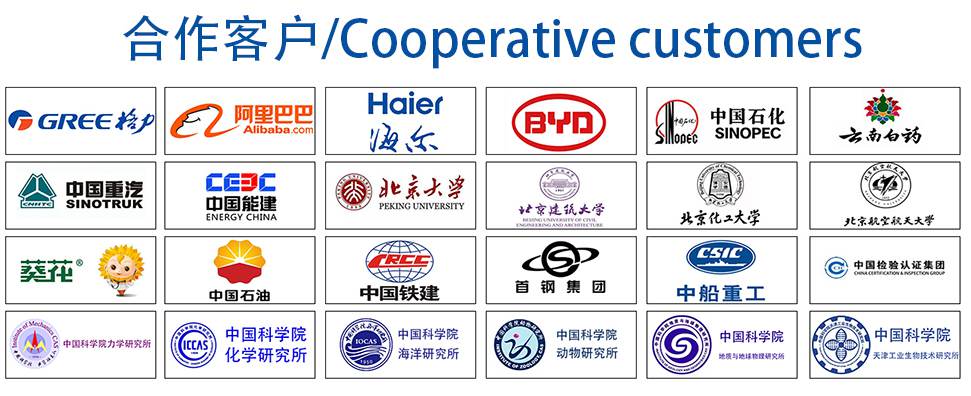