牺牲阳极检测的重要性与应用场景
牺牲阳极是一种通过自身腐蚀来保护金属结构的电化学防护技术,广泛应用于船舶、海底管道、储罐、码头等易受腐蚀的设施中。其核心原理是利用阳极材料(如锌、镁、铝合金)与受保护金属之间的电位差,形成电流回路,使阳极优先腐蚀以延缓主体结构的损耗。然而,随着时间推移和工作环境的变化,牺牲阳极的性能可能逐渐衰减,因此定期检测其状态至关重要。通过科学检测,可以评估阳极的剩余寿命、安装有效性以及整体保护效果,从而避免因阳极失效导致的结构安全隐患和经济损失。
牺牲阳极检测的核心项目
1. 阳极材料成分与尺寸检测
首先需验证阳极材料的化学成分是否符合标准(如ASTM B418或GB/T 4948),确保其电化学活性满足要求。同时需测量阳极的几何尺寸(长度、宽度、厚度)及重量,比对设计参数以确认是否因腐蚀导致体积显著减少。若阳极损耗超过30%,通常需考虑更换。
2. 电化学性能测试
通过开路电位(OCP)、闭路电位(CCP)和电流输出能力等参数评估阳极性能。使用万用表或恒电位仪测量阳极与被保护金属间的电位差,确保其处于-800mV至-1100mV(相对于铜/硫酸铜参比电极)的有效保护范围。电流输出值需与理论设计值匹配,若偏差超过20%则需进一步分析原因。
3. 阳极腐蚀状况检查
采用目视检查与无损检测(如超声波测厚)相结合的方式,观察阳极表面是否均匀腐蚀、有无局部穿孔或脱落。异常腐蚀形态(如晶间腐蚀或点蚀)可能暗示材料质量问题或环境条件异常。
4. 安装状态与接地电阻检测
检查阳极与被保护结构的电气连接是否牢固,测量接地电阻值(通常要求≤0.1Ω)。若连接点氧化或松动,会导致电流分布不均,显著降低保护效果。
5. 剩余寿命评估
通过消耗率公式计算剩余寿命: 剩余寿命(年)=(初始重量-当前重量)/(消耗率×年腐蚀时间) 其中消耗率需结合现场环境数据(如海水盐度、温度)进行修正,最终给出维护或更换建议。
检测技术与标准规范
现代检测常结合电化学工作站、微距摄影和三维扫描技术,提升数据精度。主要依据标准包括ISO 15589-1(油气管道阴极保护)、NACE SP0387(海洋结构物阳极检测)以及各行业专用规范。对于高风险设施(如LNG储罐),建议每2年进行一次全面检测,并结合实时监测系统实现动态管理。
结语
牺牲阳极检测是保障阴极保护系统有效运行的核心环节,需从材料性能、安装质量和环境适应性多维度开展综合分析。通过标准化检测流程与数据驱动的评估方法,可显著延长设施寿命,降低维护成本,为工业设备的安全运行提供可靠保障。
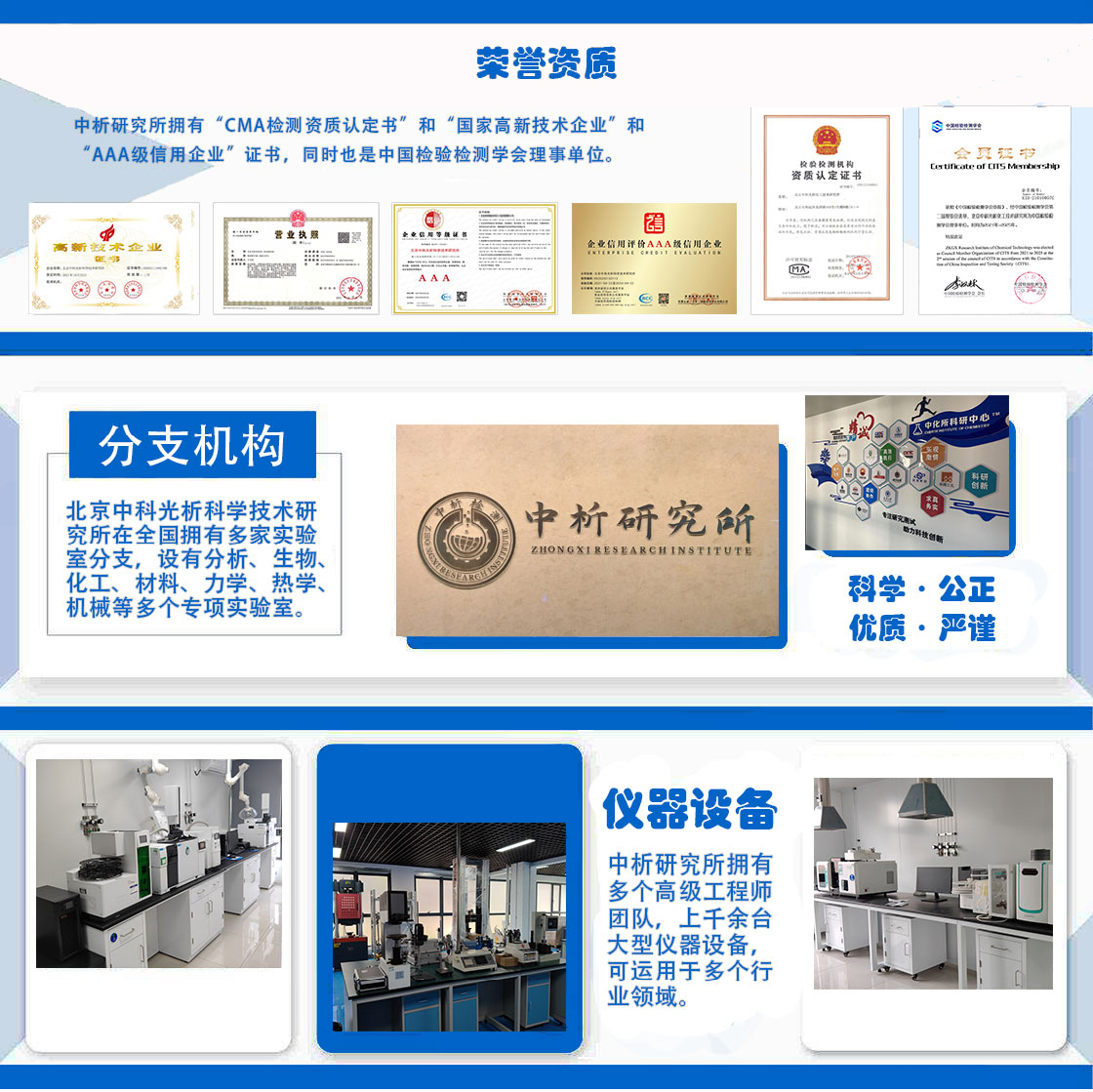
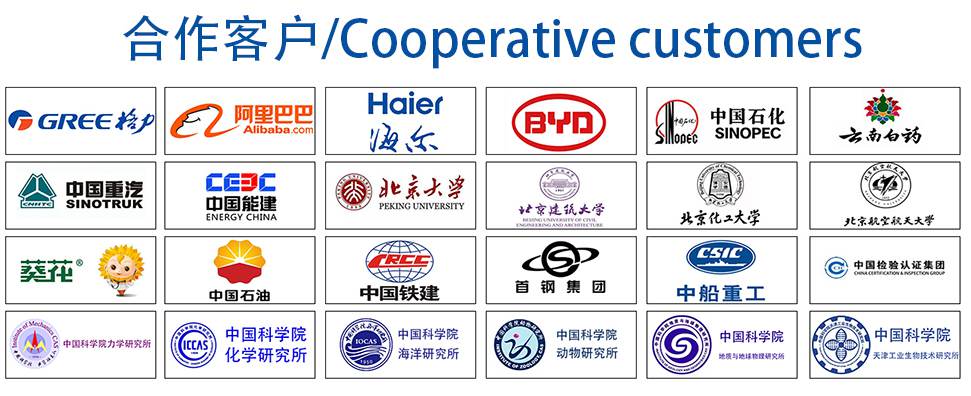