焊缝及熔敷金属检测的重要性
焊缝及熔敷金属检测是确保焊接结构安全性和可靠性的核心环节。在工业制造、建筑工程、管道输送及压力容器等领域中,焊缝质量直接关系到设备的承压能力、抗疲劳性能和使用寿命。熔敷金属作为焊接过程中形成的金属层,其成分、力学性能和微观组织直接影响焊缝的整体性能。因此,通过科学的检测手段评估焊缝及熔敷金属的质量,能够有效避免因焊接缺陷导致的应力集中、裂纹扩展甚至结构失效,对保障工程安全、降低运维成本具有重要意义。
主要检测项目及方法
1. 化学成分分析
通过光谱仪或化学滴定法检测熔敷金属的化学成分,确保其符合设计要求的合金元素比例(如C、Mn、Si等)。例如,在低合金钢焊接中,需严格控制硫、磷等杂质含量以避免热裂纹。
2. 力学性能测试
包括拉伸试验(测定抗拉强度、屈服强度)、冲击试验(评估低温韧性)及弯曲试验(检验塑性变形能力)。依据标准如GB/T 2651-2008,通过试样模拟实际工况验证焊缝的承载能力。
3. 金相组织检验
采用金相显微镜或扫描电镜(SEM)观察焊缝及热影响区的微观组织,分析晶粒尺寸、相组成及夹杂物分布,判断是否存在过热、未熔合等冶金缺陷。
4. 无损检测(NDT)
综合应用超声波检测(UT)、射线检测(RT)及磁粉检测(MT)等技术,定位焊缝内部的裂纹、气孔、夹渣等缺陷。例如,射线检测可发现尺寸≥2%壁厚的体积型缺陷,灵敏度达ISO 17636标准。
5. 宏观与微观缺陷分析
通过宏观腐蚀试验(如酸蚀法)检查焊缝截面是否存在咬边、焊瘤等宏观缺陷,同时结合微观硬度测试(维氏硬度计)评估热影响区的软化或硬化现象。
6. 耐腐蚀性评估
针对特定工况(如海洋环境、高温高压),开展盐雾试验、晶间腐蚀试验或应力腐蚀试验,验证熔敷金属的耐蚀性能是否符合NACE MR0175等标准要求。
检测标准与技术发展
国内外主流标准如ASME BPVC Section IX、ISO 5817及GB/T 3323-2005,均对检测方法和验收指标作出明确规定。近年来,随着智能检测技术(如相控阵超声、数字射线成像)及大数据分析的应用,检测效率和精度显著提升,为焊接质量控制提供了更可靠的技术保障。
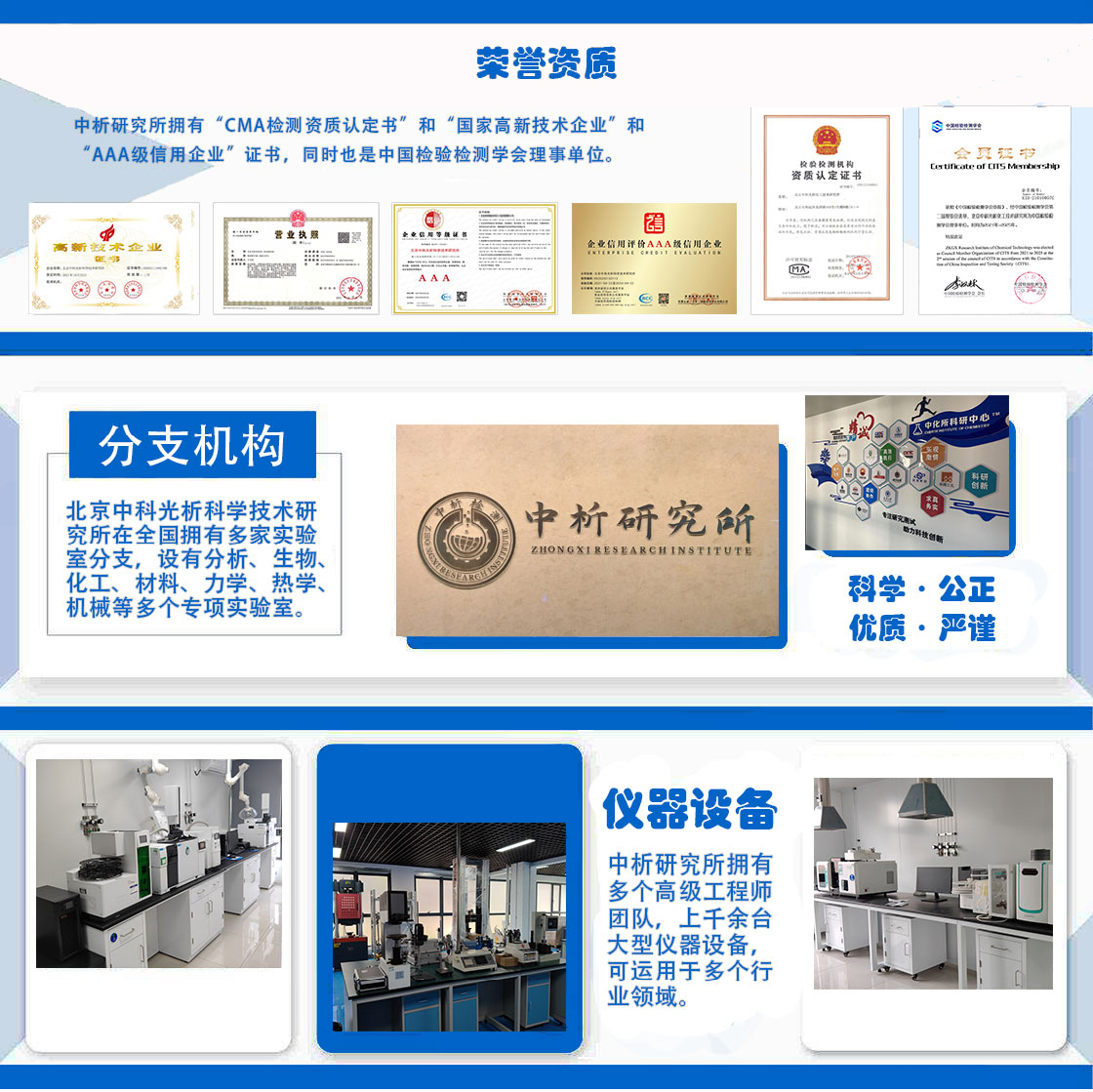
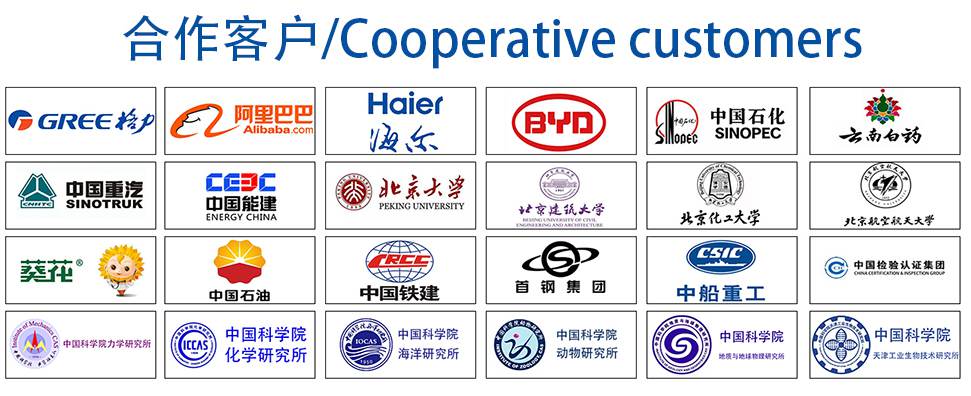