塑料部件检测:确保产品质量与安全的核心环节
在塑料制品广泛应用于汽车、电子、医疗器械、包装等领域的今天,塑料部件的质量控制已成为企业生产过程中不可忽视的关键环节。塑料部件检测通过系统性验证材料的物理性能、化学特性及功能表现,不仅能有效预防因材料缺陷导致的产品失效风险,还能帮助企业在激烈的市场竞争中建立质量口碑。尤其在精密工业领域,微小的尺寸偏差或材料老化都可能引发连锁质量问题,因此建立覆盖原材料、生产过程到成品的全流程检测体系至关重要。
核心检测项目解析
1. 尺寸与形位公差检测
采用三坐标测量仪(CMM)进行三维尺寸扫描,检测长度、直径、角度等基础尺寸参数,同时验证平面度、圆度、同轴度等形位公差。对于微结构部件,需使用激光扫描显微镜进行μm级精度测量。检测标准依据ISO 2768或客户定制技术规范。
2. 机械性能检测
包含四大核心测试:
拉伸强度测试:按ASTM D638标准测定断裂伸长率、弹性模量等参数
冲击韧性测试:通过悬臂梁(IZOD)或简支梁(CHARPY)冲击试验机验证抗冲击性能
弯曲强度测试:依据ISO 178测定材料在受力弯曲时的变形抗力
压缩性能测试:评估部件在持续压力下的变形恢复能力
3. 热学性能检测
通过热变形温度测试(HDT)、维卡软化点测试评估材料耐热性,使用差示扫描量热仪(DSC)分析玻璃化转变温度(Tg)和熔融指数(MFI)。热老化测试模拟长期高温环境下的性能变化趋势。
4. 化学兼容性检测
针对不同应用场景,测试塑料部件在接触燃油、润滑油、清洁剂等化学物质时的溶胀、脆化现象。采用FTIR红外光谱分析材料成分,GC-MS检测塑化剂等添加剂的迁移量。
5. 环境可靠性测试
包含三阶段模拟实验:
- 紫外线老化测试:模拟户外暴晒环境(ASTM G154)
- 湿热循环测试:验证高湿度环境下的尺寸稳定性
- 盐雾腐蚀测试:评估海洋环境或含盐介质的耐腐蚀性能
6. 功能性验证测试
根据产品实际使用场景设计专项检测:
• 密封件进行气密性/水密性加压测试
• 传动部件实施动态疲劳试验(50万次循环以上)
• 光学部件测量透光率与雾度值
• 食品接触材料进行FDA或EU 10/2011迁移量检测
检测技术发展趋势
随着工业4.0的推进,在线检测系统(SPC)与AI视觉检测技术开始普及,X射线断层扫描(X-CT)可实现内部缺陷的无损检测。同时,基于大数据的质量预测模型正逐步应用于工艺优化,推动塑料部件检测向智能化、预防性方向发展。
通过建立完整的塑料部件检测体系,企业不仅能有效控制质量成本,更能为产品创新提供可靠的数据支撑。选择具备 、CMA资质的专业检测机构,结合数字化质量管理系统,将成为塑料制品企业提升核心竞争力的关键路径。
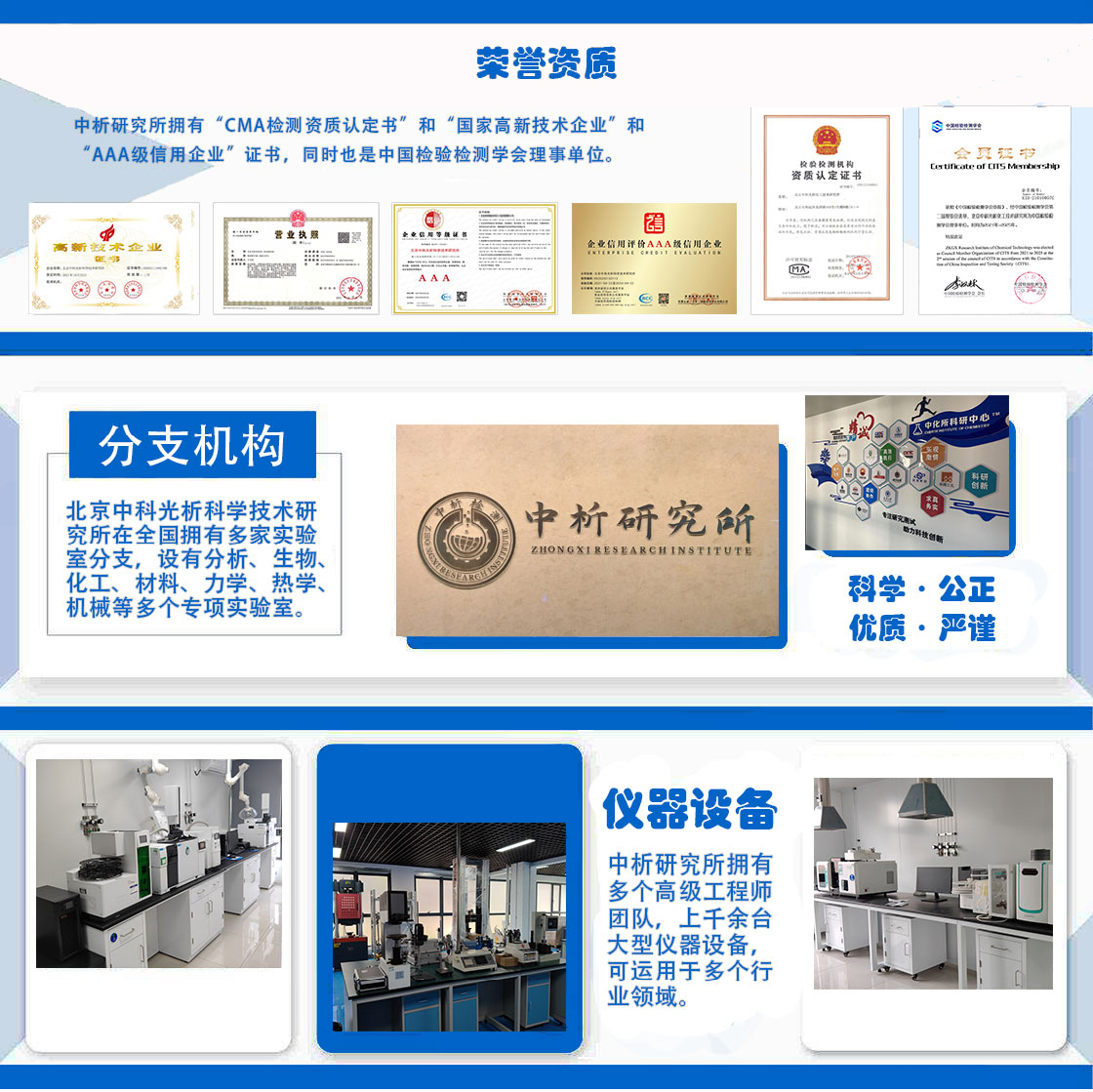
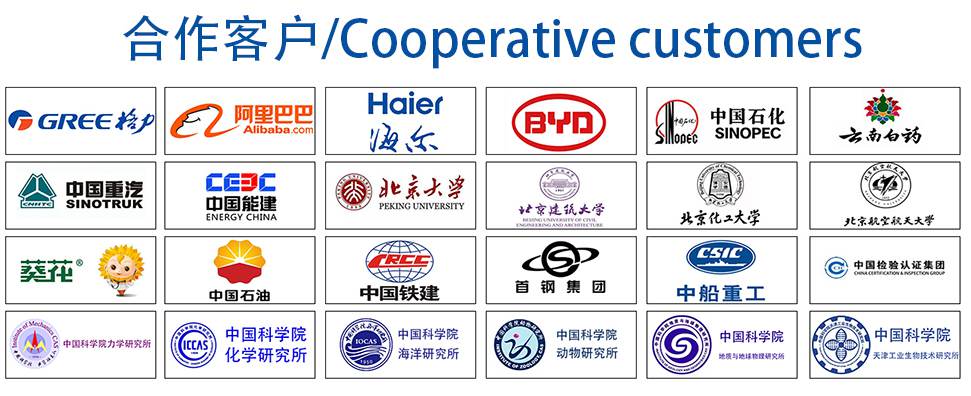